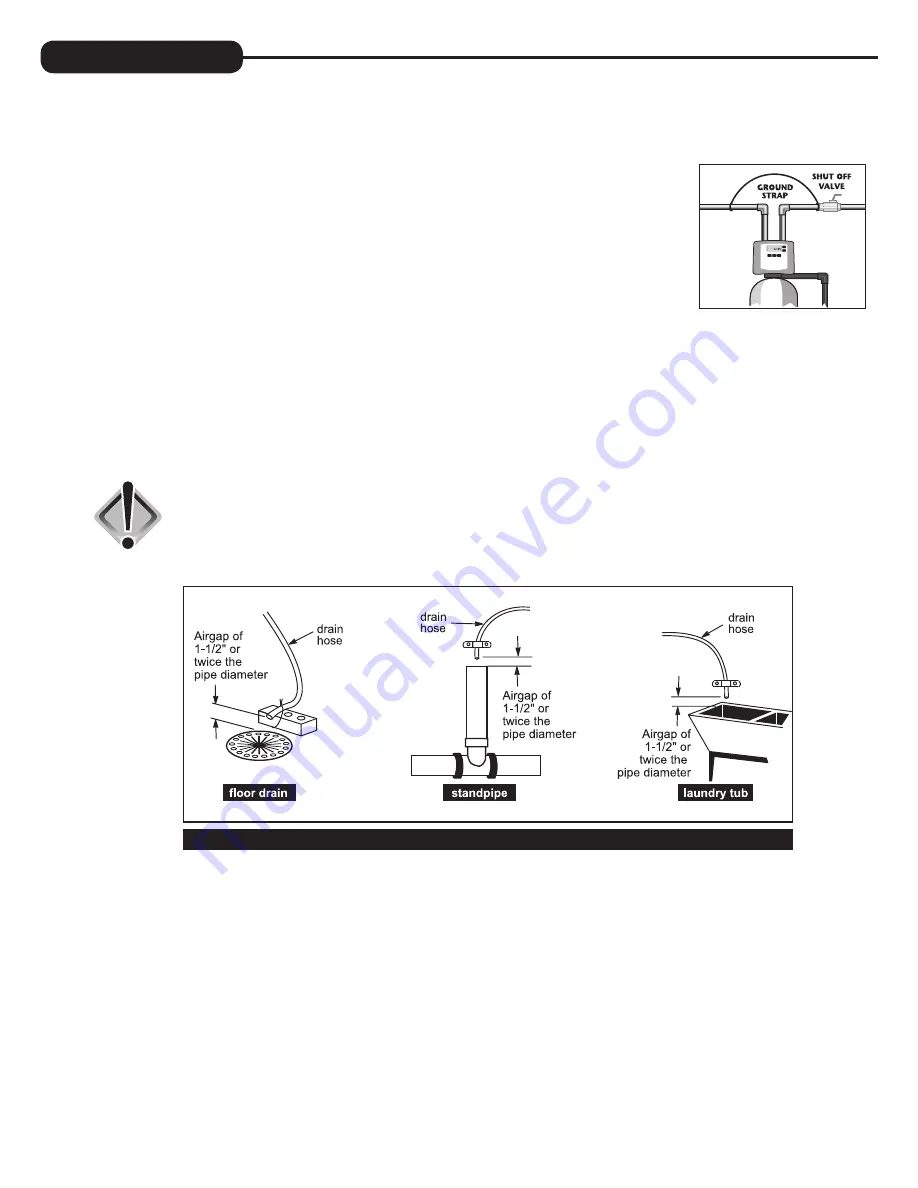
6
7
should be set before installing the nut, split ring and “O” Ring . Avoid getting solder flux, primer, and solvent cement on any
part of the “O” Rings, split rings, bypass valve or control valve . If the building’s electrical system is grounded to the plumbing,
install a copper grounding strap from the inlet to the outlet pipe . Plumbing must be done in accordance with all applicable
local codes .
7 .
INSTALLING GROUND:
To maintain an electrical ground in metal plumbing of a home’s
cold water piping (such as a copper plumbing system), install a ground clamp or jumper wiring .
NOTE:
If replacing an existing softener, also replace the ground clamps/wire . If removing a
softener, replace the piping with the same type of piping as the original to assure plumbing
integrity and grounding .
8 .
DRAIN LINE:
First, be sure that the drain can handle the backwash rate of the system . Solder
joints near the drain must be done prior to connecting the drain line flow control fitting . Leave
at least 6” between the drain line flow control fitting and solder joints . Failure to do this could
cause interior damage to the flow control . Install a 1/2” I .D . flexible plastic tube to the Drain Line Assembly or discard the
tubing nut and use the 3/4” NPT fitting for rigid pipe (recommended) . If the backwash rate is greater than 7 gpm, use a 3/4”
drain line . Where the drain line is elevated but empties into a drain below the level of the control valve, form a 7” loop at the
discharge end of the line so that the bottom of the loop is level with the drain connection on the control valve . This will provide
an adequate anti-siphon trap . Piping the drain line overhead <10 ft is normally not a problem . Be sure adequate pressure is
available (40-60 psi is recommended) . Where the drain empties into an overhead sewer line, a sink-type trap must be used
with appropriate air gap (see drawing) . Run drain tube to its discharge point in accordance with plumbing codes . Pay special
attention to codes for air gaps and anti-siphon devices .
CAUTION:
Never insert a drain line into a drain, sewer line, or trap. Always allow
an air gap of 1-1/2” or twice the pipe diameter, whichever is greater,
between the drain line and the wastewater to prevent the possibility
of sewage being back-siphoned into the softener.
TYPICAL DRAIN LINE INSTALLATIONS
INSTALLATION