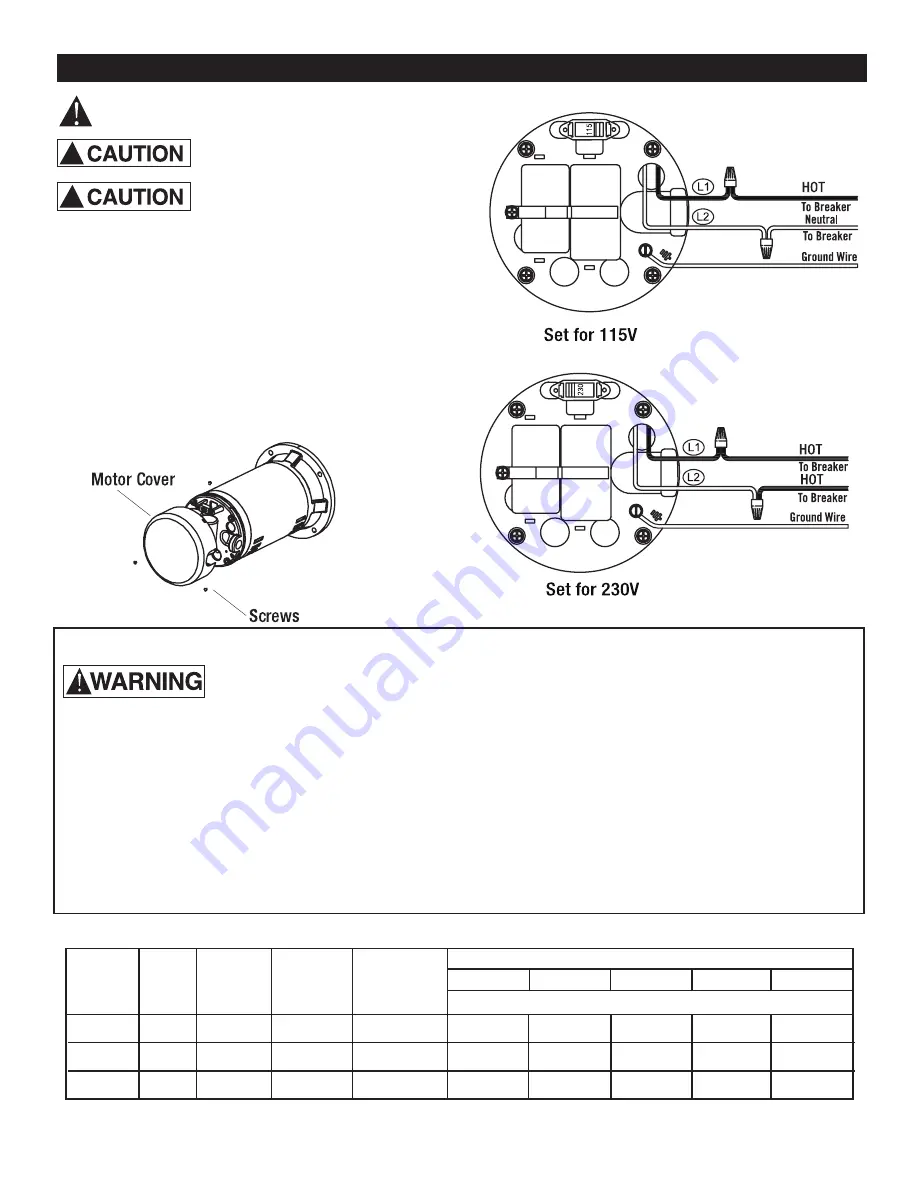
6
ELECTRICAL
Disconnect power before working on
pump, motor, pressure switch or wiring
Motor may be hot. Allow to cool 20
minutes.
Water pressure may have built up in
the pump, pipes and/or tank. Drain
water to relieve pressure.
!
!
4. Use wire size specified in Wiring Chart (below). If
possible, connect pump to a separate branch circuit
with no other appliances on it.
5. Do not ground to a gas supply line.
6. Wire motor according to diagram on motor nameplate.
If nameplate diagram differs from diagrams above,
follow nameplate diagram.
7. If this procedure or the wiring diagrams are
confusing, consult a licensed electrician.
NOTICE
Pump must be on dedicated circuit
not shared by any other equipment
.
Wiring Connections
Risk of electric shock. Electricity
can shock, burn or kill.
1. To avoid dangerous or fatal electrical shock, turn OFF
power to motor before working on electrical
connections.
2. Ground motor before connecting to electrical power
supply. Failure to ground motor can cause severe or
fatal electrical shock hazard.
3. Supply voltage must be /- 10% of nameplate
voltage. Incorrect voltage can cause fire or damage
motor and voids warranty. If in doubt consult a
licensed electrician.
Motor Voltage Settings
Motors are designed to run on either 115 volt or 230 volt
current. Be sure the motor’s current is set to match the
current being supplied to your motor from the electrical
source.
To set your motor to the correct voltage, first remove the
rear cover plate. Next slide the voltage conversion switch
to the correct voltage. WIRING THE PUMP FOR THE
INCORRECT VOLTAGE WILL DAMAGE THE PUMP.
Wiring Chart Recommended Wire and Fuse Sizes for 115 and 230 volts
BRANCH
AWG
DISTANCE IN FEET FROM MOTOR TO SUPPLY
FULL LOAD
FUSE/BREAKER
MIN. WIRE
0-100
101-200
201-300
301-400
401-500
MOTOR HP VOLTS
AMPS RATING AMP SIZE (mm
2
)
AWG WIRE SIZE (mm
2
)
1
115/230
18.5/9.25
30/15
10/14 (5.5/2)
10/14 (5.5/2)
8/14 (2/2)
6/14 (14/2)
6/12 (14/3) 4/10 (21/5.5)
1-1/2
115/230
22/11
30/15
10/14 (5.5/2)
10/14 (5.5/2) 8/14 (8.4/2)
6/12 (14/3) 4/10 (21/5.5) 4/10 (21/5.5)
2
115/230
27.0/13.5
35/20
8/12 (8.9/3)
8/12 (8.9/3)
8/12 (8.4/3) 6/10 (14/5.5) 4/10 (21/5.5) 4/10 (21/5.5)
Summary of Contents for WA10PLS
Page 8: ...WA10PLS WA15PLS WA20PLS ...