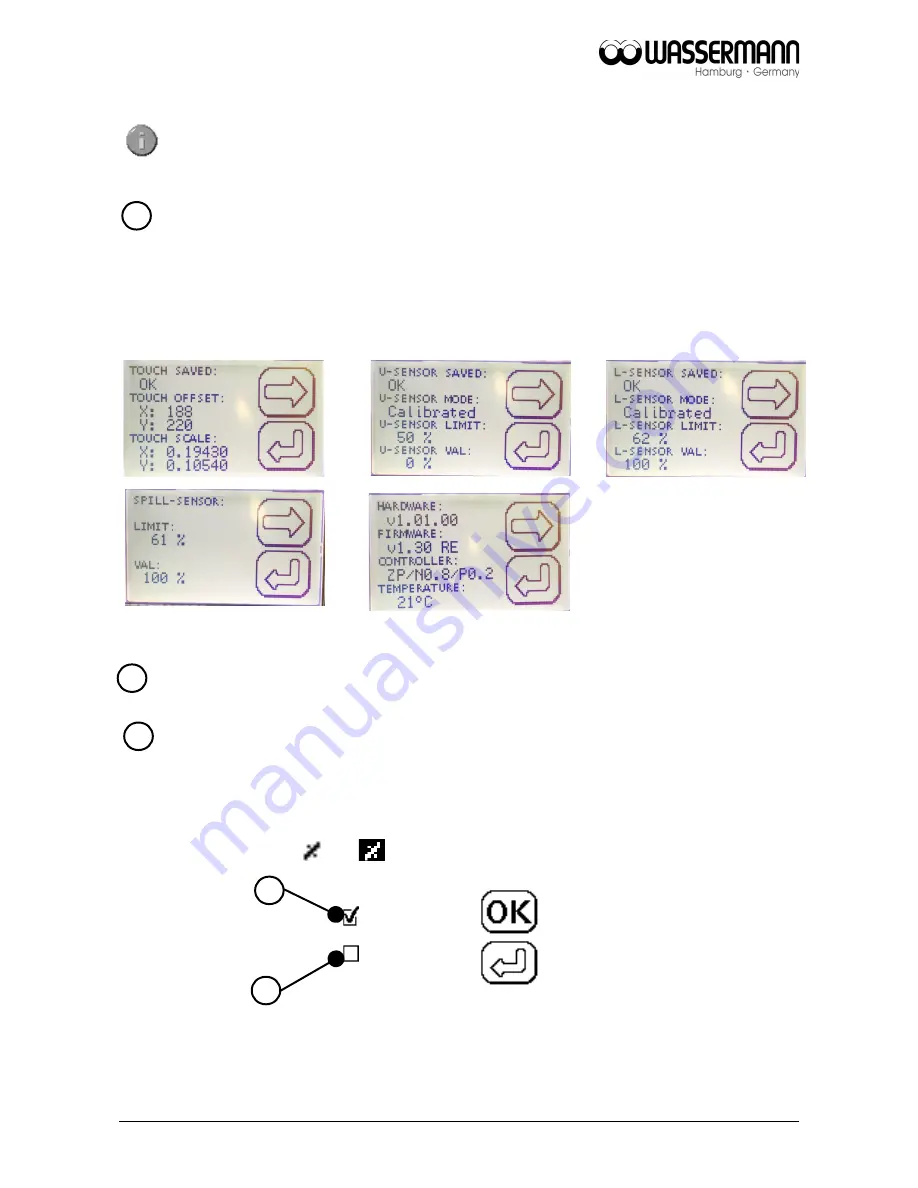
Please note that, owing to the scalding process, the temperature can fall by
several degrees. The higher the set temperature, the higher the deviation.
Information
Here the parameters from the touch screen, sensors, hardware and software are
displayed.
„Back to start menu“
Automatic wax removal
The automatic wax removal process is conducted before or after the scalding process
once a minimum temperature of
80 °C
has been reached. The removal/rolling mode is
indicated by the symbol . or
if it is active. Parameters for rolling control.
DEF
MAN
(a) Default: 3 min
ON
/ 3 min
OFF
.
(b) Manuel: 1-29 min
ON
/ time-off = time-on.
18
17
a
b
15
16
Summary of Contents for Wapo-Ex 12 II
Page 1: ...Boil Out Unit Wapo Ex 12 II USER MANUAL...
Page 36: ......