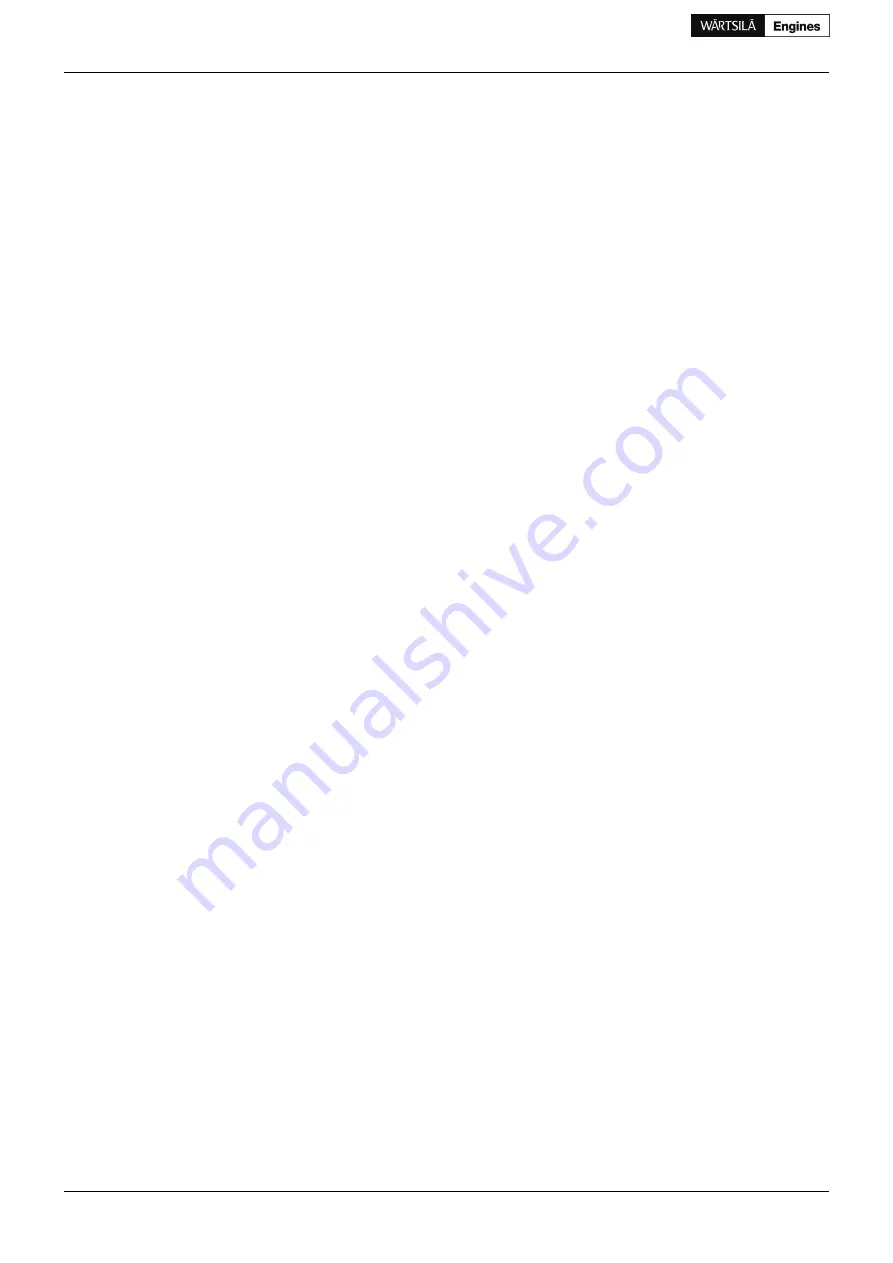
The twin injection valve is a combined main fuel oil injection and pilot fuel oil injection valve, which is centrally
located in the cylinder head. The main diesel injection part of the valve uses traditional spring loaded needle
design.
The hotbox encloses all main fuel injection equipment and system piping, providing maximum reliability
and safety. The high pressure side of the main injection system is thus completely separated from the exhaust
gas side and the engine lubricating oil spaces. Any leakage in the hot box is collected to prevent fuel from
mixing with lubricating oil. For the same reason the injection pumps are also completely sealed off from
the camshaft compartment.
Pilot fuel injection system
The pilot fuel injection system is used to ignite the air-gas mixture in the cylinder when operating the engine
in gas mode. The pilot fuel injection system uses the same external fuel feed system as the main fuel oil
injection system.
The pilot fuel system comprises the following built-on equipment:
•
Pilot fuel oil filter
•
Common rail high pressure pump
•
Common rail piping
•
Twin fuel oil injection valve for each cylinder
The pilot fuel filter is a full flow duplex unit preventing impurities entering the pilot fuel system. The fineness
of the filter is 10 µm.
The high pressure pilot fuel pump is of an engine-driven radial piston type mounted in the free end of the
engine. The delivered fuel pressure is controlled by the engine control system and is approximately 100
MPa.
Pressurized pilot fuel is delivered from the pump unit into a small diameter common rail pipe. The common
rail pipe delivers pilot fuel to each injection valve and acts as a pressure accumulator against pressure
pulses. The high pressure piping is of double wall shielded type and well protected inside the hot box. The
feed pipes distribute the pilot fuel from the common rail to the injection valves.
The pilot diesel injection part of the twin fuel oil injection valve has a needle actuated by a solenoid, which
is controlled by the engine control system. The pilot diesel fuel is admitted through a high pressure connection
screwed in the nozzle holder. When the engine runs in diesel mode the pilot fuel injection is also in operation
to keep the needle clean.
4.2.12
Exhaust pipes
The exhaust manifold pipes are made of special heat resistant nodular cast iron alloy. The connections to
the cylinder head are of the clamp ring type. The complete exhaust gas system is enclosed in an insulating
box consisting of easily removable panels fitted to a resiliently mounted frame. Mineral wool is used as in-
sulating material.
4.2.13
Lubricating oil system
The engine internal lubricating oil system include the engine driven lubricating oil pump, the electrically
driven prelubricating oil pump, thermostatic valve, filters and lubricating oil cooler. The lubricating oil pumps
are located in the free end of the engine, while the automatic filter, cooler and thermostatic valve are integ-
rated into one module.
4.2.14
Cooling system
The fresh water cooling system is divided into a high temperature (HT) and a low temperature (LT) circuit.
The HT-water cools cylinder liners, cylinder heads and the first stage of the charge air cooler. The LT-water
cools the second stage of the charge air cooler and the lubricating oil.
4.2.15
Turbocharging and charge air cooling
The SPEX (Single Pipe EXhaust system) turbocharging system combines the advantages of both pulse and
constant pressure systems. The complete exhaust gas manifold is enclosed by a heat insulation box to
ensure low surface temperatures.
24
Product Guide Wärtsilä 34DF - 3/2012
Product Guide
4. Description of the Engine