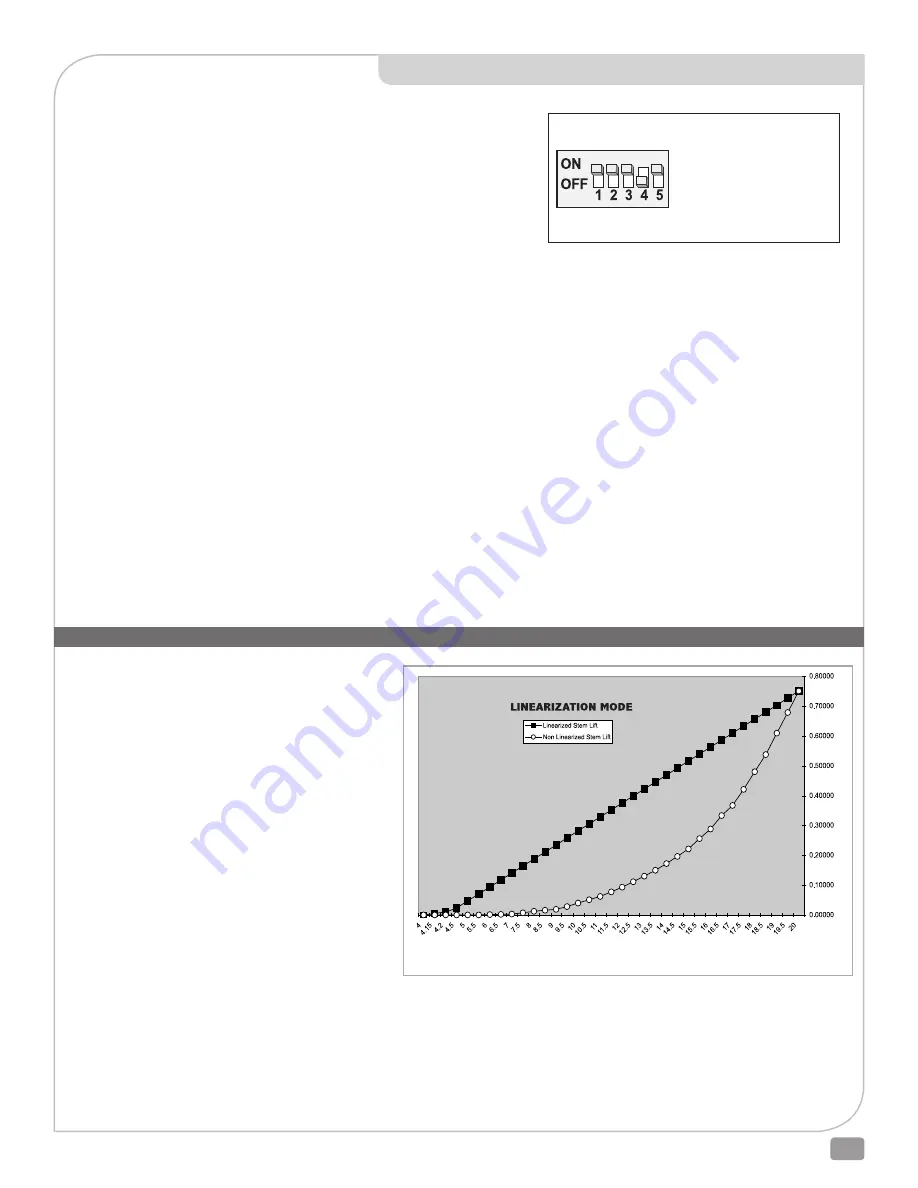
AmurAct AMURACT_IOM_RevK_0415
7
Factory default configuration of the five dipswitches is shown below.
Switch #1
Factory default - ON
An increasing control
signal causes the valve stem to drive up, opening
a two-way valve, or opening the L (lower) port and
closing the U (upper) port of a three-way valve. The
valve stem will drive down upon loss of signal. When
Switch 1 is in the OFF position an increasing control
signal causes the valve stem to drive down, closing a
two-way valve, or closing the L (lower) port and opening the U (upper) port of a three way valve. The valve stem will drive up
upon loss of signal.
Switch #2
Factory default - ON
Upon loss of power the Enerdrive® circuit will drive the valve stem down, closing a two-way
valve, or closing the L (lower) port and opening the U (upper) port of a three-way valve. When Switch #2 is in the OFF position,
upon loss of power the Enerdrive® circuit will drive the valve stem up, opening a two-way valve or opening the L (Lower) port
and closing the U (upper) port of a three-way valve.
Switch #3
Factory default - ON
The motor will accept a 4-20 mAdc control signal connected to terminals 1(-) and 3(+) on
terminal block 1. When Switch #3 is in the OFF position the motor will accept a 2-10 vdc signal.
Switch #4
Factory default - OFF The motor will provide a 4-20 mAdc feedback output at terminals 1(-) and 5(+) on terminal
block 1. When Switch #4 is in the ON position the motor will provide a 2-10 vdc output.
Switch #5
(2-Way) Factory default - ON
This establishes a linear relationship between the control signal and valve stem lift. When
Switch #5 is in the OFF position a “non-linear” relationship is established between the control signal and valve stem lift. This is
uniquely applicable only on 3-way valve linkages.
(3-Way) Factory default - OFF The 3-way linkage has a different signal to lift relationship and should not use the linearization
feature. For 3-way valves, switch #5 should always be OFF.
DIPSWITCHES
Switch #1: Action &
Signal Loss
Switch #2: Power Fail
Switch #3: Signal
Switch #4: Feedback
Switch #5: Linearization
CONFIGURATION OF DIPSWITCHES
mA Signal
St
em L
ift
Placing dipswitch #5 in its ON (Linearizing) position
accomplishes several objectives that may be helpful in
specific control valve installations. One result is that the
entire input signal range is applied to modulating the valve
opening. Only at the very end of the signal range does the
AmurAct linkage drive into lockup. Another result is that
the inherent characteristic of the control valve is preserved.
“Linearizing” operation can provide linear flow control
when using a valve having linear trim.
Placing dipswitch #5 on its OFF (Non-Linear) position causes
the valve stem to rise very slowly in the beginning of its
stroke, and to rise increasingly rapidly as the valve opens.
This mode uses the first 25% of the control signal to move
the linkage into and out of lockup. “Non-Linear” operation
may be useful when additional control is needed at low
flow rates, and additional response is required for changes
in higher flow rates.
Selection of the linearization mode (dipswitch #5) can be
made during operation, and dipswitch #5 should be left in
the position that produces the better system control result.
FOR 2-WAY ONLY