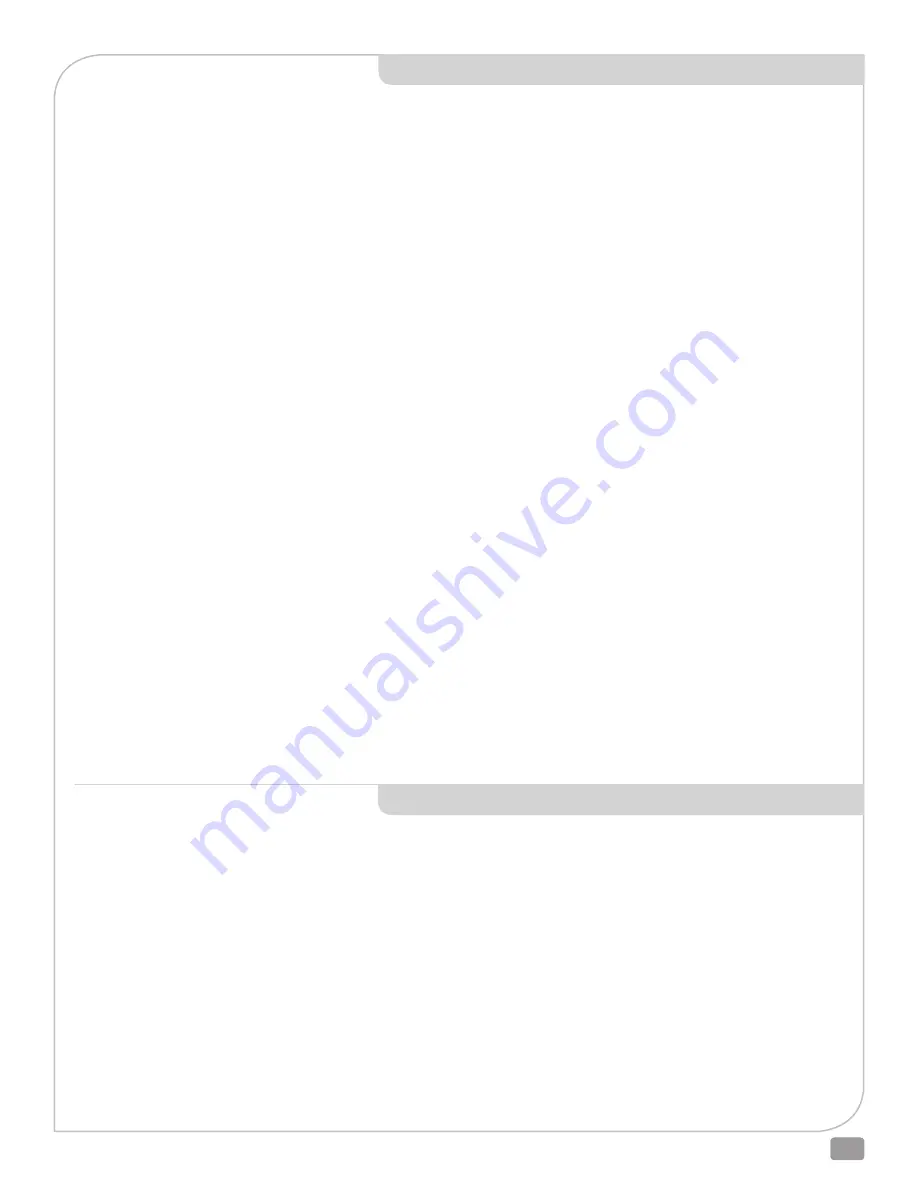
AmurAct AMURACT_IOM_RevK_0415
15
A.
No valve movement:
1. Check that operating power and signal are present at the
motor terminals.
2. Check fuse for continuity. Shut the isolation valves and then
press the Reset push button. Observe that the valve travels
fully open then shut.
3. Review WIRING AND STARTING ( page 5-8) to confirm wiring
and switch positioning.
4. Remember to press the Reset pushbutton to perform the
AutoStroke calibration cycle. It will optimize performance
and maximize motor life.
B
.
Valve and Motor are “out of sync” ie: the linkage or
motor do not both reach their ends of travel, or they arrive at
different times.
1. Check for indication of slippage between the motor output
clamp and the linkage input shaft. If slipping is detected, the
linkage and motor must be re-calibrated. See pages 10-14
as necessary to review both procedures. Pay close attention
to tightening the two 10 mm hex nut on the motor output
clamp, and remember to press the Reset pushbutton to
perform the Autostroke calibration cycle. It will optimize
performance and maximize motor life.
C.
After extensive usage, valve closure tightness appears to
have diminished.
1. Remove the motor (see page 8) and then perform LINKAGE
CALIBRATION (see page 11-13) and MOTOR CALIBRATION
(see page 10). This will restore seat-closing force to its original
high value, correcting for normal linkage wear.
2. Remember to press the Reset pushbutton to perform the
Autostroke calibration cycle. It will optimize performance and
maximize motor life.
D.
If the actuator does not respond correctly to the control
signal, does not provide full valve travel as the control signal
increases and decreases throughout its full range, complete
the following steps until correct operation is restored.
1. Verify the dipswitch settings are correct.
2. Verify the wiring connections are correct.
3. Verify the power supply voltage is correct and there is power
to the actuator.
4. Verify fuse continuity.
5. Verify circuit board status. If status is normal, after the fail safe
capacitors have fully charged and the LED goes out, the LED
will flash about once every 15 to 20 seconds.
6. Verify the control signal is correct and properly calibrated.
7. Verify the control signal minimum and maximum. For a
4-20 mAdc control signal the control signal minimum must
reach 4.00 mAdc; the control signal maximum must reach
20.00 mAdc. For a 2-10 Vdc control signal, the control signal
minimum must reach 2.00 Vdc; the control signal maximum
must reach 10.00 Vdc.
8.Verify the AmurAct linkage is installed and calibrated correctly.
9. Verify the AmurAct motor is installed correctly.
10. Initate an AUTOSTROKE CALIBRATION CYCLE. STOP You must
wait for the AUTOSTROKE CALIBRATION CYCLE to finish
before going on to the next step.
11. Reset the actuator programming to the factory default.
12. Contact the factory for assistance.
E.
Resetting the actuator programming to the factory
default
1. Remove line presure and isolate valve in piping.
2. Remove power and control signal.
3. Record the position of all dipswitches.
4. Place all dipswitches in the OFF position.
5. Apply power and within 10 seconds quickly press and release
the RESET pushbutton.
The LED should flash 1 flash/second. If the LED is lit solid and
does not go out, turn power off then repeat this step.
6. While the LED is flashing, move dipswitch #2 ON then OFF.
7. Wait for the LED to go out.
8. Restore all dipswitches to the correct position for the
application.
9. Initiate an AUTOSTROKE CALIBRATION CYCLE. STOP You
must wait for the AUTOSTROKE CALIBRATION CYCLE to finish
before going on to the next step.
10. Restore control signal.
11. Return line pressure to valve.
F.
For more information or advice, contact your Warren
Controls sales representative, or our factory at (610) 317-0800.
TROUBLESHOOTING
AmurAct control valves are designed to operate for extended
periods of time without maintenance or operator action.
1. No operator action is needed after a power outage sends
AmurAct into its fail-safe position. It will resume normal
operation when power is restored. Recall that nothing
happens until completion of the Enerdrive recharging
process which may take up to 60 seconds. It will then respond
to a control signal input.
2. Initiate the motor’s AutoStroke calibration cycle each time
AmurAct is placed into service following any intentional
shutdown, adjustment, calibration or maintenance. Failure to
do so can cause inaccuracy of control and premature failure
of the motor.
3. Fail safe position on loss of signal can be verified during
normal operation by interrupting the control signal. Fail-safe
position on loss of power can be verified when the Enerdrive
circuit is fully charged by interrupting the normal power
supply.
4. Improper calibration of the electric controller by others may
cause the control valve to “hunt”, causing abnormal wear and
premature failure.
5. The safe and preferred way to wire a high temperature limit
device to an AmurAct control valve is use the relays of the
High Limit device to interrupt the CONTROL SIGNAL to the
actuator. Power to the actuator should remain ON at all times.
By interrupting the signal, the internal default Fail-Safe circuit
will force the valve closed upon loss of signal (when the
high limit is tripped). When the high limit releases the relay,
the AmurAct can INSTANTLY respond and begin controlling
again.
OPERATING TIPS