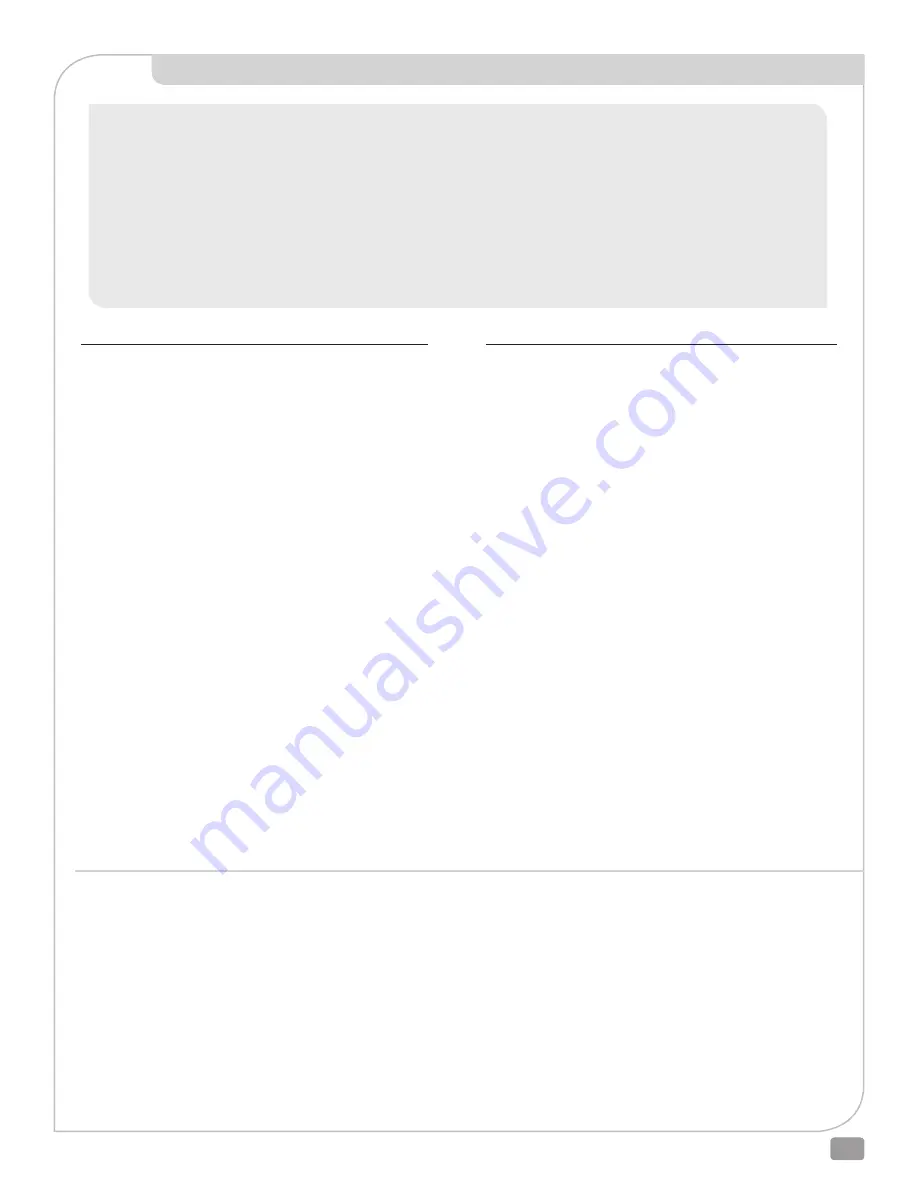
AmurAct AMURACT_IOM_RevK_0415
11
REMOVING AN AmurAct LINKAGE (all versions)
1.
After the motor has been removed according to instructions
on page 8, and with the line isolation valves securely shut,
remove the c-clamp from the crank and base. Manually
rotate the crank clockwise to release stem force.
_______________________________________
2.
Remove the lower shoulder screw, nut and washer from the
stem connector. Remember to retain all removed parts for
reassembly.
_______________________________________
3.
Using a drift pin or blunt chisel and striking hammer, loosen
and remove the large nut that secures the linkage base to
the threaded valve bonnet. Lift the entire AmurAct linkage
assembly from the bonnet. Store it safely for re-use.
NOTE
Care must be taken to avoid rotating the valve
plug while it is in contact with the valve seat to
avoid damaging the valve’s seating surfaces.
_______________________________________
4.
If the valve is to be re-packed, hold the jam nuts and remove
the stem connector. Measure and record the distance from
the top of the jam nuts to the end of the valve stem. This will
facilitate re-assembly. Loosen and remove the jam nuts.
_______________________________________
INSTALLING AN AmurAct LINKAGE (all versions)
1.
Loosely install the valve stem jam nuts to the dimension
recorded earlier, or ½” from the end of the valve stem.
_______________________________________
2.
Thread the stem connector onto the stem into loose contact
with the top jam nut.
_______________________________________
3.
Lower the linkage assembly over the valve stem and bonnet
then slide the bonnet nut over the connector and loosely
thread the nut onto the threaded bonnet until it contacts
the linkage base.
_______________________________________
4.
Rotate the linkage base to the desired orientation and tighten
the bonnet nut using a drift pin or blunt chisel and striking
hammer to ensure that it is securely fastened.
_______________________________________
5.
Rotate the stem connector so the stem connector links can
straddle it. Rotate the crank until the link bearings align with
the stem connector opening and install the shoulder screw
and washers. Tighten the nut securely.
_______________________________________
6.
The linkage is ready to be calibrated in accordance with
instructions specific to the linkage version (see definitions
above).
_______________________________________
There are currently three ways in which AmurAct linkages are employed. It is necessary to identify which version is applicable before
proceeding.
VERSION A: Two-way valves with ¾” stem travel. This applies to all two-way AmurAct control valves, with the exception of:
VERSION B: Two-way valves with 1 1/8” stem travel, currently limited to the 4” Type 20 and 23.
VERSION C: Three-way valves with ¾” stem travel. This applies to all three-way valves currently listed in the AmurAct product line.
While the difference between ¾” (A) and 1 1/8” (B) stem travels is accounted for by linkage calibration, the three-way linkage (C) is
mechanically distinct as well as being calibrated differently.
REMOVING/INSTALLING/CALIBRATING AN AMURACT LINKAGE