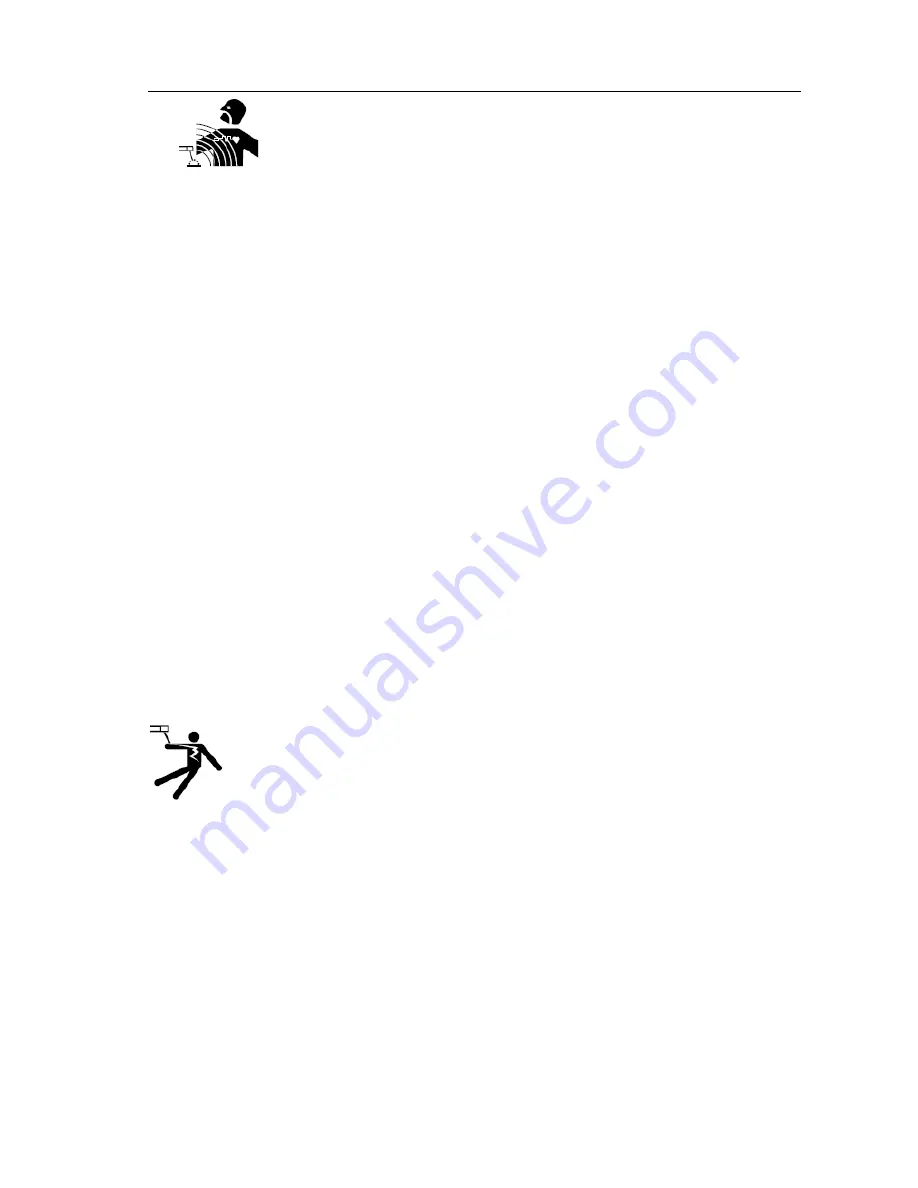
INARC-1000 I/ 1250 I
·2·
ELECTRIC AND MAGNETIC FIELDS may be dangerous
2.a.
Electric current flowing through any conductor causes localized Electric and Magnetic
Fields(EMF). Welding current creates EMF fields around welding cables and welding
machines.
2.b. EMF fields may interfere with some pacemakers, and welders having a pacemaker should
consult their physician before welding.
2.c. Exposure to EMF fields in welding may have other health effects which are now not
known.
2.d. All welders should use the following procedures in order to minimize exposure to EMF
fields from the welding circuit:
2.d.1. Route the electrode and work cables together-Secure them with tape when possible.
2.d.2. Never coil electrode lead around your body.
2.d.3. Do not place your body between your electrode and work cables. If the electrode
cable is on your right side, the work cable should also be on your right side.
2.d.4. Connect the work cable to the work piece as close as possible to the area being
welded.
2.d.5. Do not work next to welding power source.
ELECTRIC SHOCK can kill
3.a. The electrode and work (or ground) circuits are electrically “hot” when the welder is on.
Do not touch these “hot” parts with your bare skin or wet clothing. Wear dry, hole-free
gloves to insulate hands.
3.b. Insulate yourself from work and ground using dry insulation. Make certain the insulation is
large enough to cover your full area of physical contact with work and ground.
In addition to the normal safety precautions, if welding must be performed under
electrically hazardous conditions (in damp locations or wearing wet clothing; on metal
structures such as floors, gratings or scaffolds; when in cramped positions such as sitting,