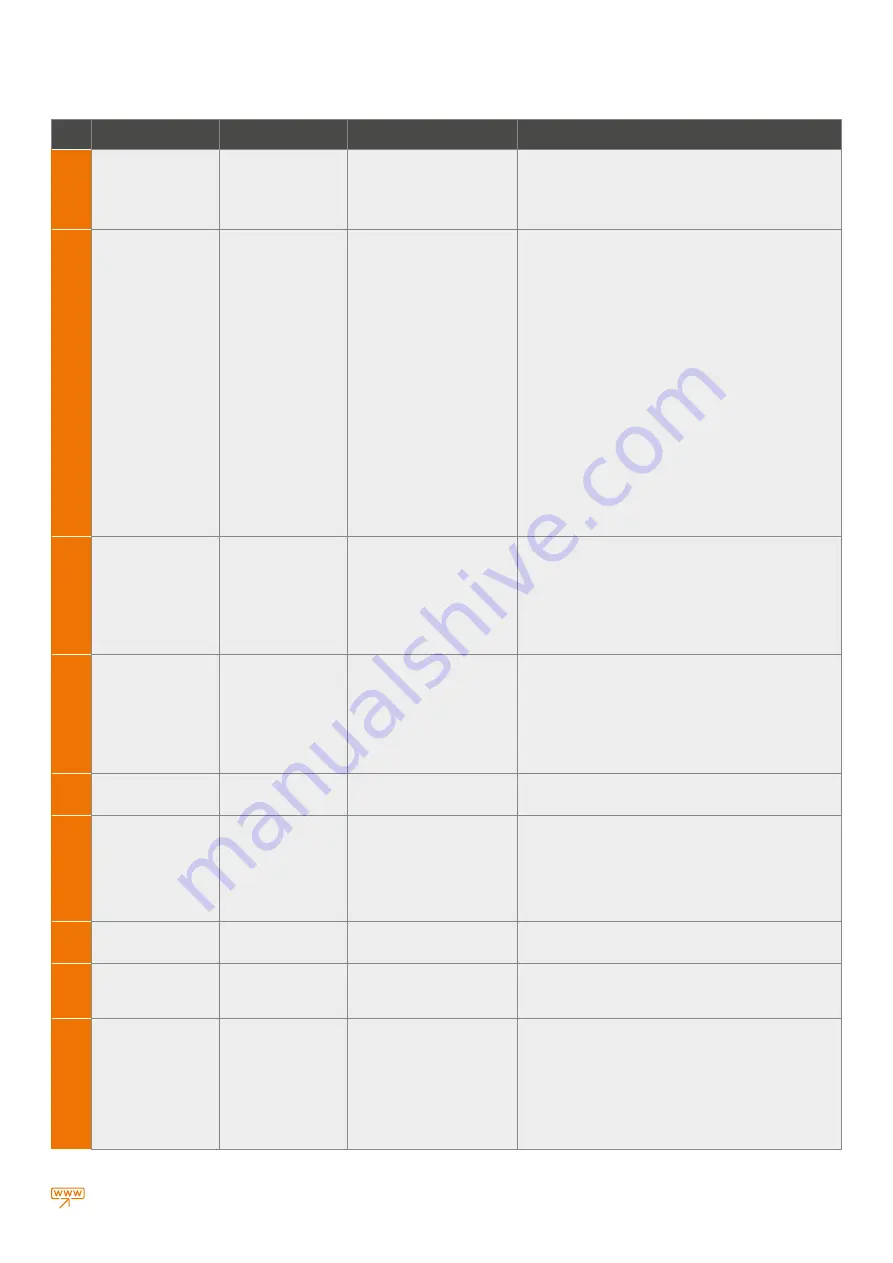
33
warmhaus.com
Error
Code
Description of the Error
Malfunction
Probable Cause
Solution(s)
E 74
Second CH temperature
Probe faulty
Boiler does not work,
E74 error code flashing on
the screen
> FLOW and LIMIT Sensor (double
NTC ) faulty
1-) Call for authorised service at first
2-) Check CH temperature probe ressistance (double CH ntc probe is
used as high temperature limit device) according to page 94 at section
4.29 if its out of tolerance replace double NTC
3-) Check cabeling and connectors between double NTC and board
4-) Reset & Restart boiler
E 77
Absolute current values
reached
Boiler does not work,
E77 error code flashing on
the screen
> Gas inlet pressure
> Aging or rust on the electrode
> Recirculation on fluegas path
> Blokage on flue or wrong flue
> Electrode position
> Cabeling disconnections
> Combustion calibration
> Electronic board
> Gas valve failiure
1-) Call for authorised service at first
2-) Check gas supply pressure must be 20-17 mBar. Gas pressure must
be in between on this values while boiler on operational
3-) Check wrong flue OR flue gas blockage
4-) Check recirculation ( flue gas leak ) from flue gas path to fresh air
side, check flue gas sealings specially
5-) Check any problems on the ionisation electrode, (like condensation,
rust etc.), and control poistioning of the electrode, if electrode poistion
wrong calibrate electrode according to user manual page 118 or 119
6-) Check if the heat exchanger coils clogged or not
7-) Check for condensation on the cabling AND/OR on board
8-) Check earth connection between board and electrode
9-) Check electrode cabeling between board and electrode
10-) Check combustion CO2 or O2 values on HI and LO mode at sweeper
mode according to direction of manual page 67- 70
11-) Perform Auto Calibration according to page 76 or 77
12-) If fault still persists Replace board, but use original service key
from the board dismantled to keep original parameters and calibration
points. If original service key not used aslo adjust P15 releated to the
default value of boiler power and perform Au-To calibration according
to page 76 or 77
13-) if not successfull replace gas valve, and Perform Au-To calibration
according to page 76 or 77 Attention: Only authorised service must
perform Au-To calibration
E 78
Max regulation current
value reached
Boiler does not work,
E78 error code flashing on
the screen
> Gas inlet pressure
> Aging or rust on the electrode
> Recirculation on fluegas path
> Blokage on flue or wrong flue
> Electrode position
> Cabeling disconnections
> Combustion calibration
> Electronic board
> Gas valve failiure
1-) Call for authorised service at first
E 79
Min regulation current
value reached
Boiler does not work,
E79 error code flashing on
the screen
> Gas inlet pressure
> Aging or rust on the electrode
> Recirculation on fluegas path
> Blokage on flue or wrong flue
> Electrode position
> Cabeling disconnections
> Combustion calibration
> Electronic board
> Gas valve failiure
1-) Call for authorised service at first
E 80
Problem on electronic gas
valve driver
Boiler does not work,
E80 error code flashing on
the screen
> Electronic board
> Gas valve failiure
1-) Call for authorised service at first
E 81
Lock-out for combustion
problem at starting (1)
Boiler does not work,
E81 error code flashing on
the screen
> Strong flue blokage
> Combustion problem
> Wrong flue
> Gas inlet pressure
> Aging or rust on the electrode
> Recirculation on fluegas path
> Electrode position
> Combustion calibration
1-) Call for authorised service at first
E82
Lock-out for combustion
problem on Lawa / Lawa
Plus models
Boiler does not work,
E82 error code flashing on
the screen
> Recirculation on fluegas path
> Blokage on flue or wrong flue
> Combustion calibration
1-) If there is strong wind (ie.wind storm) wait until the wind storm stop
then RESET the boiler
2-) IF problem persist Call for authorised service
E83
Temporary bad
combustion fault problem
on Lawa / Lawa Plus
models
Boiler does not work,
E83 error code flashing on
the screen
> Recirculation on fluegas path
> Blokage on flue or wrong flue
> Combustion calibration
1-) If there is strong wind (ie.wind storm) wait until the wind storm stop
then RESET the boiler
2-) IF problem persist Call for authorised service
E 84
Capacity reduction for
detected (supposed) low
gas inlet pressure
Boiler does not work,
E84 error code flashing on
the screen
> Gas inlet pressure
> Combustion problem
1-) If there is strong wind (ie.wind storm) wait until the wind storm stop
then RESET the boiler
2-) IF problem persist Call for authorised service
3-) Check gas supply pressure must be 20-17 mBar. Gas pressure must
be in between on this values while boiler on operational
4-) Check combustion CO2 or O2 values on HI and LO mode at sweeper
mode according to direction of manual page 67- 70
5-) Perform Auto Calibration according to page 76 or 77, IF combustion
values are out of tolerances measured one step before
Attention:
Only authorised service must perform Au-To calibration