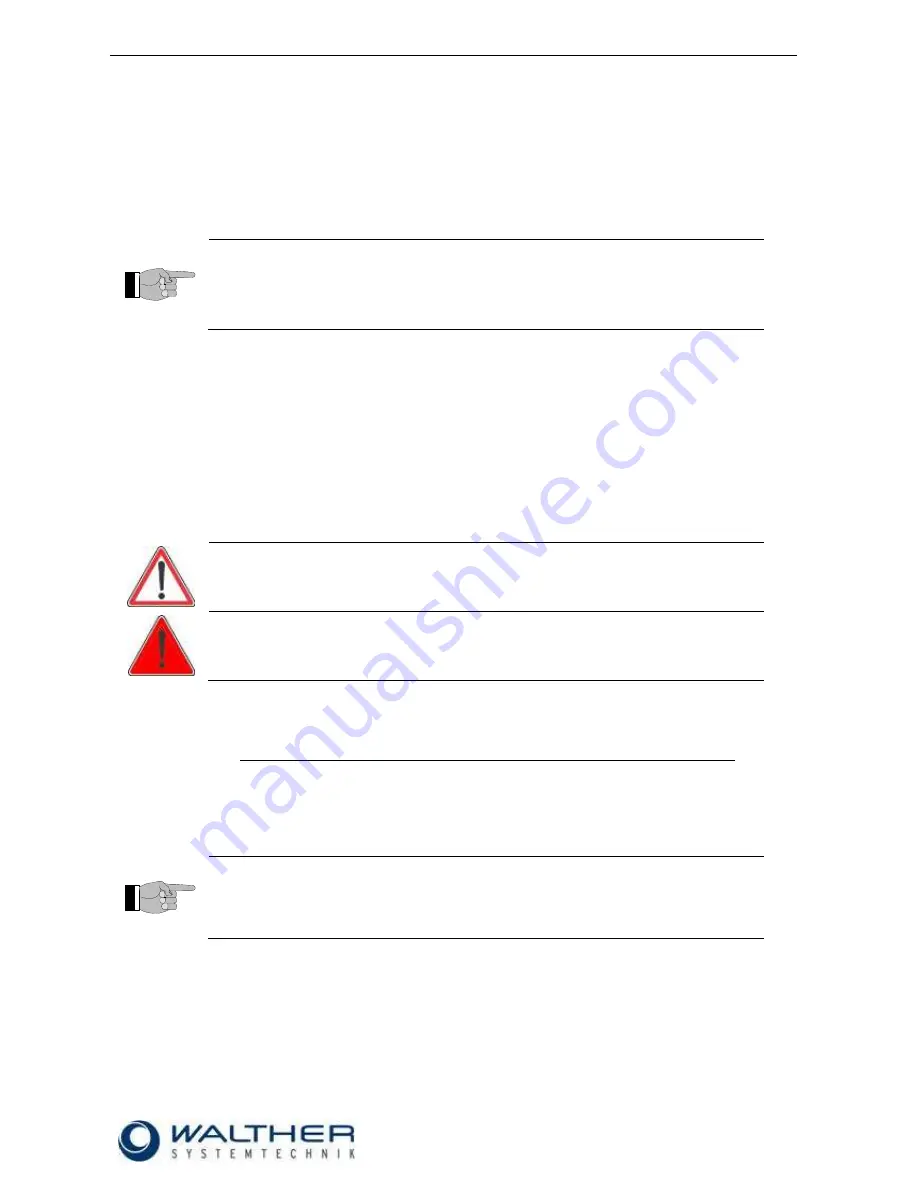
Rev. 1.1
Assembly Instructions - Hand-Spray Valve SMS-15
Page 10 of 18
Walther Systemtechnik GmbH
– D 76726 Germersheim
Telefon: +49 (0)7274-7022-0 Telefax: +49 (0)7274-7022-91
http://www.walther-2000.de
6 Operation
6.1 General Information
This device may only be operated if the safety-related equipment is permanently effective and not suspend-
ed during operation or altered in its intended effectiveness.
IMPORTANT
Please do strictly observe the following information for the set-up of devices!
Each spraying valve must be equipped with its own pressure regulator for atomizing air.
In case several spraying valves are supplied by one and the same material pressure tank, these
valves must not spray simultaneously.
The supply route for the material between material pressure tank and spraying valve must not exceed
2 m.
If the pause time is a multiple of the spray time, the valve must be sprayed free in a separate location
or the spray valve should be operated several times to optimize the application.
After standstills of 15 min. and more, the valve must be sprayed free by pressing the switch 3 to 5
times.
6.2 Operating Instructions / Operation Conditions
CAUTION
Never point the jet at people. The wearing of eye protection is strongly recommended.
The spraying process can create noise depending on the air and fluid pressures used.
Ear protection should be worn, if required.
WARNING
Danger caused by flammable, harmful fluid. Always follow the safety instructions on the
container or the safety data sheet for the fluid.
Spray valves of the
SMS-15
series generally operate with a control pressure of 4.5 - 6 bar. The atomizer
pressure has to be lower than the material pressure in order to avoid a repulse of the material. Atomized air
pressure and material pressure should be closely correlated. In case high material pressures are required,
make sure that the accident prevention regulations of the trade associations will be strictly followed.
The application can be controlled as intermitting or continuous. Depending on the individual use, the control
pressure has to be adjusted to the set switching frequency on the one hand and to the higher or lower
material pressures on the other. Under appropriate operating conditions (material pressure, control pressure,
needle stroke, and short supply lines) a total of 50 strokes per second can be reached.
IMPORTANT
A device-specific set-up is required for an optimum adjustment of the application im-
age. Basic results from lab tests can be used. Of course, these may have to be adjust-
ed for the individual device. The parameters nozzle size, opening time, opening stroke,
material pressure and if required, also temperature have to be combined.
For longer standstills, the material can remain in the valve, if it remains under pressure (no contact to outside
air).