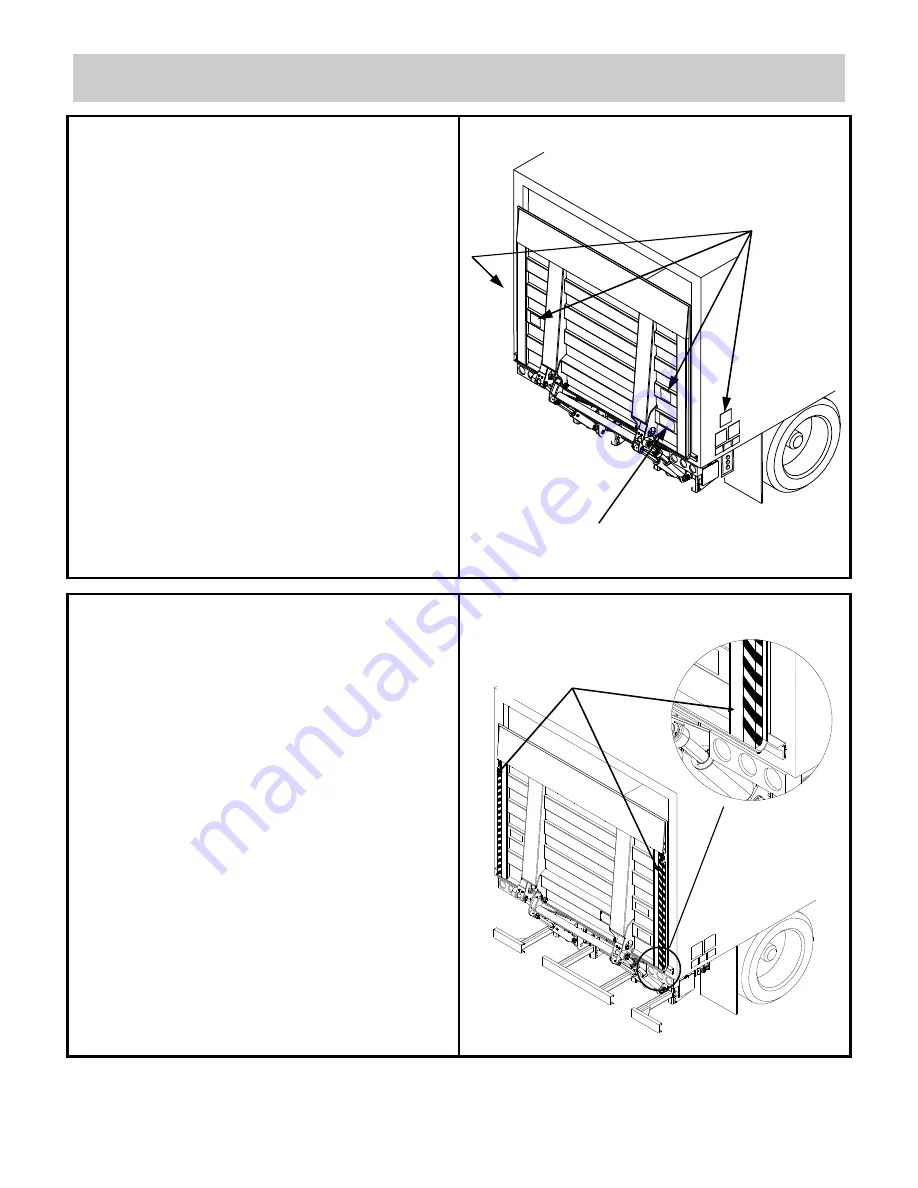
Chapter 5 Placement of Decals
INSTALLATION OF PLATFORM DECALS
The following decals are to be placed on the underside
of the platform and both sides of vehicle as shown.
75089296 – Stand Clear Decal (4)
One (1) of the following three (2) decals is to be
positioned in a conspicuous place on the bottom of the
platform as shown
80101415 – BZ-33 Capacity Decal
80101416 – BZ-44 Capacity Decal
GR00511
INSTALLATION OF SAFETY TAPE
Tape (Z20290) is to be placed on the sides of platform
so it is visible from the side and back of vehicle as
shown.
IMPORTANT!
Safety tape must wrap around side of
platform as shown.
GR00511
STAND CLEAR
DECALS HERE
IMPORTANT!
Safety
tape must wrap
around side of
platform as shown.
CAPACITY DECAL HERE
page 48
Summary of Contents for BZ-33
Page 17: ...Chapter 4 Liftgate Installation Electric and Hydraulic Diagram G page 17...
Page 18: ...Chapter 4 Liftgate Installation Electric and Hydraulic Diagram with Auto tilt G page 18...
Page 61: ...Add silicone caulk to seal gaps between tracks and vehicle body page 61...