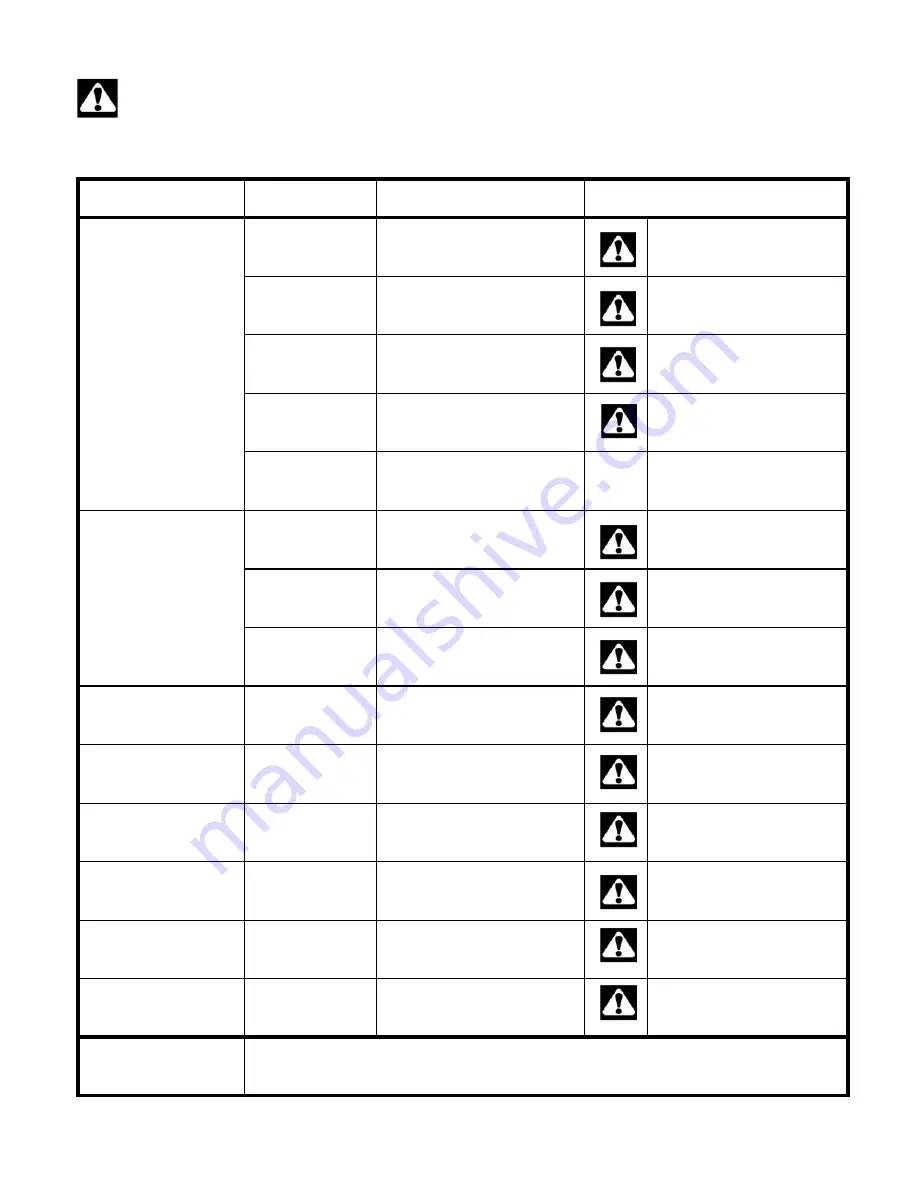
41
No pressurized
hydraulic oil.
Oil filter plugged. Change filter.
Ensure machine is off and cooled
down.
No pressurized
hydraulic oil
Low hydraulic oil level, top up
Ensure machine is off and cooled
down
Wood jammed around
wedge.
Shut machine off and safely remove
wood.
Ensure machine is off
Not enough pressure.
Call technician, system relief setting
may be low (below 2750 psi).
Ensure machine is off and call
hydraulic technician.
Low engine speed.
Check that choke is off, check
throttle is set to maximum.
Detent set too tight.
Call technician, adjustment required
with detent on valve.
Ensure machine is off and call
hydraulic technician.
Hydrualic fluid too
cold.
Allow machine to warm up.
Hydrualic fluid is too
old or contaminated.
Change hydraulic fluid and filter
Ensure machine is off and cooled
down.
Control handle goes to
neutral before rod is fully
retracted.
Detent set too loose.
Call technician, adjustment required
with detent on valve.
Ensure machine is off and call
hydraulic technician.
Control handle does't go to
neutral when released.
Control may be
damaged.
Call technician, control may need
service or be replaced.
Ensure machine is off and call
hydraulic technician.
Cylinder stops on contact
with wood.
Second stage on pump
not functioning.
Call technician, pump may need
service or be replaced.
Ensure machine is off and call
hydraulic technician.
Wedge jumps.
Wedge frame
jamming.
Lubricate wedge frame wear plates.
Ensure machine is off.
Leaking hydraulic hose.
Hose worn or
damaged.
Replace hose.
Ensure machine is off and cooled
down.
Leaking cylinder.
Seals worn.
Call technician, seal replacement
may be required.
Ensure machine is off and call
hydraulic technician.
Engine related issues.
CAUTION
Refer to your engine instruction manual for specific trouble shooting instructions / requirements.
Cylinder rod moves slowly or
doesn't move.
Control handle doesn't go to
neutral after rod is fully
retracted.
PROBLEM
CAUSE
SOLUTION
6.1 TROUBLE SHOOTING CHART
Always wear the appropriate safety gear when trouble shooting, performing maintenance or working around the
machine� This includes but is not limited to:
• Hard hat for protection to the head�
• Face mask for protection to the face and eyes�
• Heavy gloves for hand protection�
• Safety shoes with slip resistant soles and steel toes