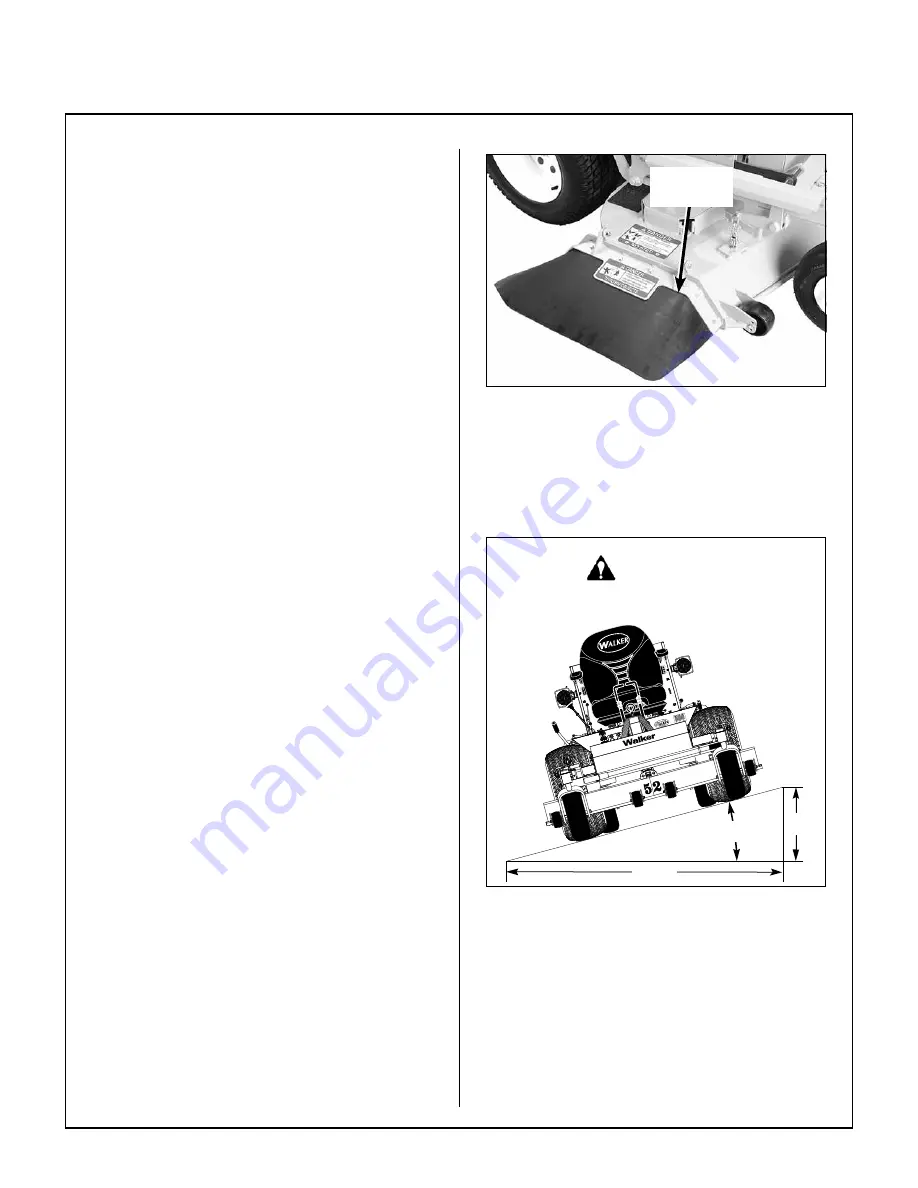
Operating Instructions
39
•
When mowing, operate the engine at
full throttle
for the best cutting action. Mowing with a lower en-
gine RPM causes the mowing blade to not cut clean
and tear the grass. The engine is
designed to be
operated at full speed.
•
When mowing in adverse conditions (tall and/or
wet grass), mow the grass twice. Raise the mower to
the highest setting - 5 in. (127 mm) - for the first pass
and then make a second pass cutting to the desired
height.
•
Use a
slow
setting on the FSC for
trimming
op-
erations.
•
Make sure the mower is
leveled properly
for a
smooth cut. Refer to
Deck Leveling
in
Assembly In-
structions
.
•
Use an alternating
stripe mowing pattern
for
best appearance
and vary the direction of the stripe
each time the grass is mowed to avoid wear patterns
in the grass.
•
Avoid damage to the grass by slipping and skid-
ding of the drive tires. Use
smooth control move-
ments
of the steering levers since the transaxles are
“power boosted controls” and jerking the levers can
easily slip the tires. For sharp turns, do not allow the
inside wheel to stop and twist on grass; pull inside
steering lever into reverse for a smooth “rolling” turn
(one wheel rolling forward while the other rolls back-
ward).
•
When using the DSD60 deck, or other side dis-
charge decks, the side discharge shield
must not be
removed
and must be kept in the lowest possible
position to deflect grass clippings and thrown objects
down ward. Orient the side discharge away from
side walks or streets to minimize cleanup of clippings.
When mowing close to obstacles, orient the side dis-
charge away from obstacles to reduce the chance of
damage to property by thrown objects.
Discharge
Shield
Side Discharge Shield in Lowest Position
•
When operating on a slope,
reduce speed and
use caution
to start, stop, and maneuver. Avoid
sharp turns or sudden changes in direction. The
maximum recommended side slope operating
angle is 15 degrees or 26% grade.
52 in.
16 in.
15°
Maximum Recommended
Side Slope - Do Not Operate
on Steep Slopes
Maximum Recommended Side Slope