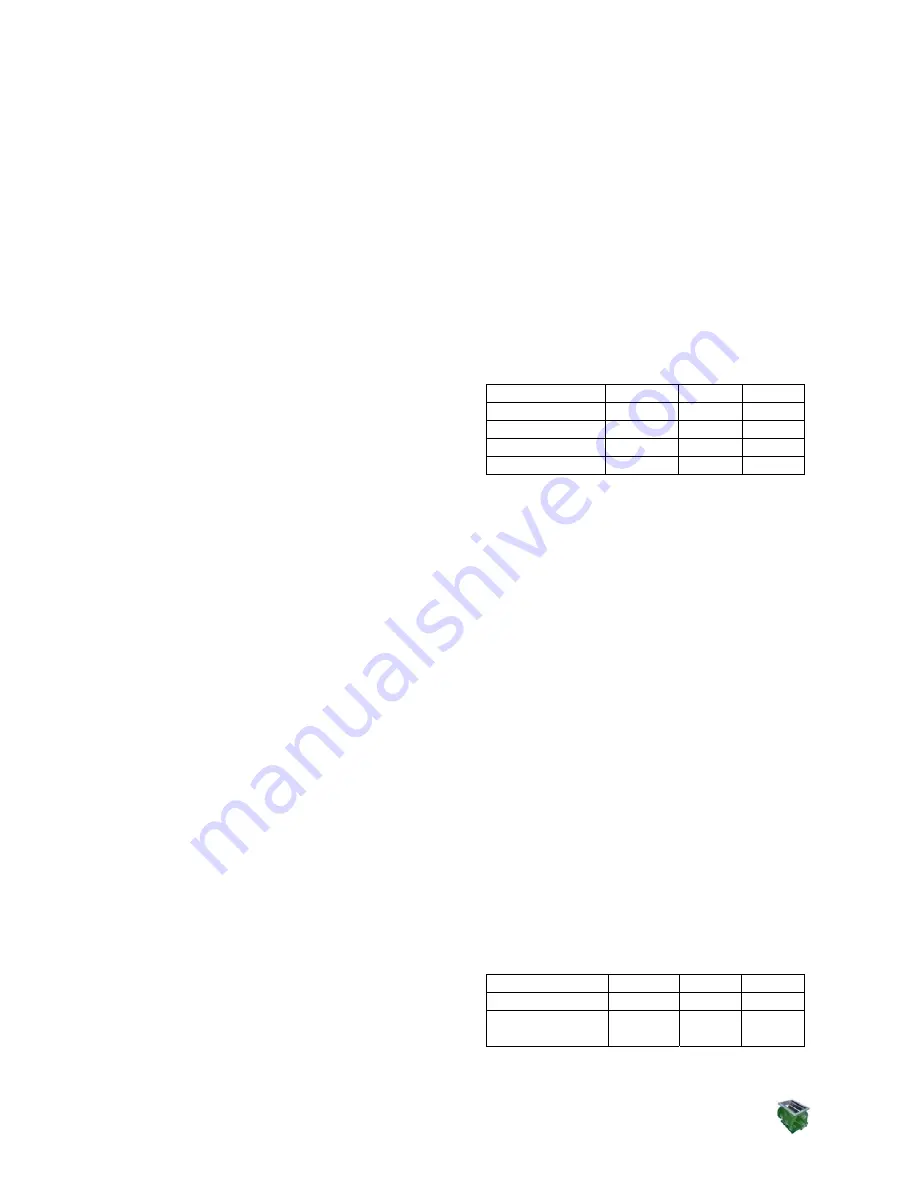
5
1
INTRODUCTION
1.1 Operating Principles
Walinga Rotary Airlocks use a multi-bladed
rotor to move material. The rotor picks up
material in the pocket between each 2 blades
as it rotates past the top feed inlet area. It
then transfers the feed through the airlock
casing to either a ‘blow-through’ or ‘drop-
through’ chamber at the bottom.The airlock
often features low clearance wear tips on
each rotor. These are both adjustable &
replaceable and usually made of high-wear
material. Other tip materials and designs may
be used for specialized applications. The tips
deliver a high degree of sealing between the
material supply chamber and the outlet
area.During operation the multi-bladed rotor
fills with material at the inlet (top) side of the
unit. This material moves with the rotating
blades and drops through to either the' blow-
through' or 'drop-through' chamber below.
‘Blow- Through’ designs use a pressurized
air-stream entering the inlet port to move
material through the chamber to a pneumatic
transfer line connected to the outlet port.
‘Drop- Through’ designs drop the product out
of the airlock under gravity through a large
rectangular discharge port under the unit.
1.2 Airlocks
&
Rotary Seals
The terms ‘airlock’ / ‘rotary valve’ and 'rotary
seal' are sometimes used to describe the
same item of equipment. In general an
‘airlock' provides a higher level of sealing and
is more easily adjusted than a 'rotary seal'.
Their heavy duty cast construction and high
level of sealing suit them well to commercial
applications - especially when using
pressurized delivery line.
2 KEY OPERATING GUIDELINES
2.1 Direction of Rotation
The airlock rotor
MUST MOVE COUNTER -
CLOCKWISE WHEN VIEWED FROM THE
DRIVEN END.
Do not operate for extended periods in reverse
direction.
PROLONGED OPERATION IN REVERSE
DIRECTION OF ROTATION RESULTS IN HIGH
WEAR RATES IN THE CASING AND LOSS OF
PERFORMANCE.
Operating for short periods in reverse direction is
acceptable but only to assist in clearing objects
jammed between the blades and casing. Reverse
operation also increases product damage because
the flexible tip wiper is not effective when the rotor
moves in a clock-wise direction (viewed from the
driven end).
2.2
Tip Clearances
MODEL 1314
1618
2224
Maximum 0.014
0.016
.020
Minimum 0.005
0.006
.008
Preferred 0.006
0.007
.009
Max. Reset
0.009
0.010
.010
An adjustable tip fits at the outer edge of each rotor
blade. These tips provide a seal as the rotor
transfers material from the intake to the outlet area.
Efficient operation requires a close fit between the
top of each blade tip and the airlock casing.
Excessive clearance allows ‘blow-back' of air
through the airlock causing uneven flow and
reduced performance. Check and adjust airlock
blade tip clearances regularly as part of a scheduled
maintenance program. Routine maintenance of tip
clearances is especially important in materials with
high abrasion characteristics.
2.3 Rotor Clearances
Airlock rotors are not adjustable, so clearances can
not be changed. If the clearance between the rotor
and the endplate is too high, no amount of tip
adjustment will improve performance. If the
rotor/endplate clearance total is at or greater than
the total clearance in the chart below, the airlock
should be replaced.
Model 1314
1618
2224
Clearance/side
0.010 0.012 0.015
Total
Clearance
0.020 0.024 0.030
Summary of Contents for AL 1314
Page 1: ...OPERATOR S MANUAL FOR DROP THROUGH ROTARY AIRLOCKS MODELS AL 1314 AL 1618 AL 2224...
Page 2: ...2...
Page 11: ...11...
Page 12: ...12 6 1 ROTARY AIRLOCK MODEL AL 1314 COMPONENTS...
Page 13: ...13 6 1 ROTARY AIRLOCK MODEL AL 1314 COMPONENTS CONT D...
Page 14: ...14 6 2 ROTARY AIRLOCK MODEL AL 1618 COMPONENTS...
Page 15: ...15 6 2 ROTARY AIRLOCK MODEL AL 1618 COMPONENTS CONT D...
Page 16: ...16 6 3 ROTARY AIRLOCK MODEL AL 2224 COMPONENTS...
Page 17: ...17 6 3 ROTARY AIRLOCK MODEL AL 2224 COMPONENTS CONT D...