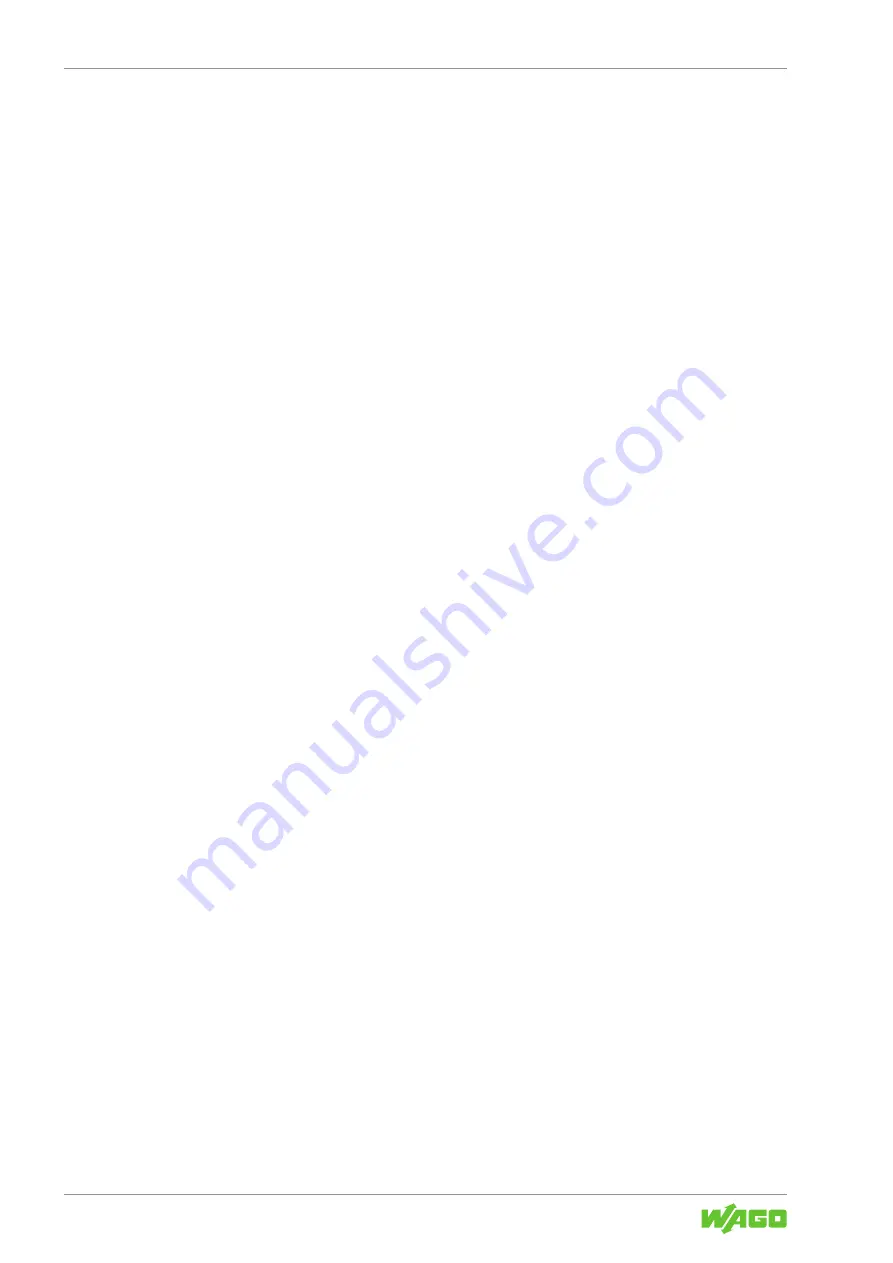
765-1103/100-000
Connection
46
Product manual | Version: 2.2.0
16DO FLD PN DC 24V 2.0A
9
Connection
9.1 General Information on Installation
When laying cables, the local conditions and the applicable regulations are crucial for im-
plementation.
Be sure to maintain the minimum clearances between the cabling and possible sources
of interference (including machines, welding equipment and power lines) to prevent loss
and corruption of data. For planning and installation of a system, observe the regulations
and standards.
Mechanical Stress
Protect the cables against mechanical stress. Observe the following information:
• Select the correct type of cable for the application Ensure a sufficient wire cross-sec-
tion
• Take the minimum bending radius into account
• Ensure that cables cannot get in the shearing zone of movable machine parts
• Do not lay the cables across transport paths and the paths of machine movements
• Use cable ducts or cable bridges
Interference
Follow the following instructions to reduce interference:
• Lay network cables (e.g., fieldbus cables) in their own cable ducts
• Do not lay network cables parallel to power supply cables through which high power
flows
• When installing shielded pluggable connectors (screws, cap nuts), ensure the best
possible contact between the shielding and ground. Before initial commissioning,
check the grounding or shielding connection of the cables for low-resistance conductiv-
ity.
Protective Caps
Cover all unused connections with protective caps to protect the connections and ensure
compliance with the requirements of protection type IP67.
Grounding Concept
There are basically two grounding options, which can also be used simultaneously:
• Via cable
• Via the housing
The I/O System Field operates in the extra-low voltage range (SELV/PELV). In these de-
vices, interference is discharged via functional ground (FE). Functional ground (FE) is
merely for discharging interference. It does not provide touch-proof protection for per-
sons. Functional grounding is essential for fault-free operation of the device.
If you wish to perform additional grounding via the metal housing:
• Use conductive mounting screws on the mounting holes and ensure there is a good
contact there
• Ensure that the mounting surface is level