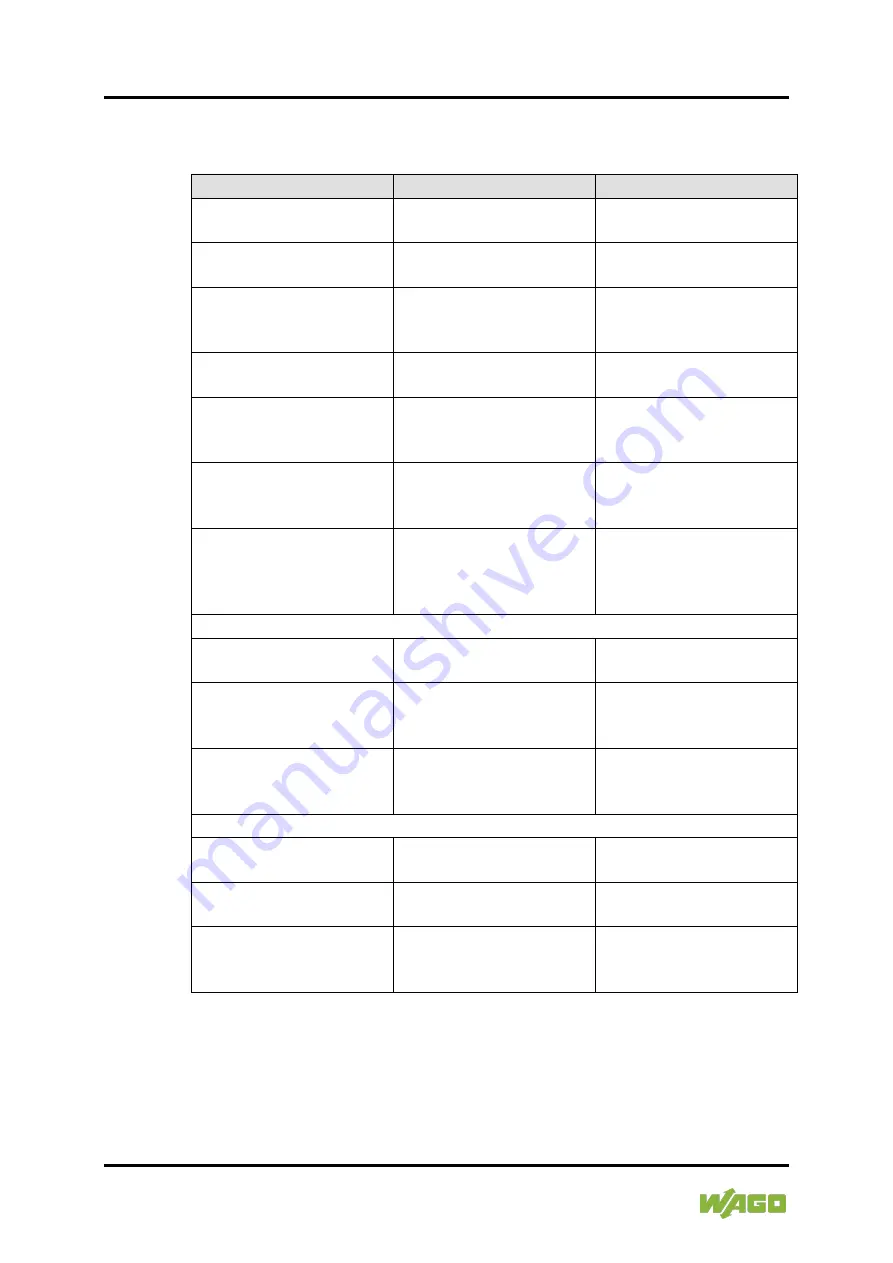
296 Diagnostics
WAGO-I/O-SYSTEM 750
750-8215 PFC200; G2; 4ETH CAN USB
Manual
Version 1.2.0, valid from FW Version 03.02.02(14)
The CAN LED indicates following diagnostics:
Table 207: Diagnostics CAN LED
Status
Explanation
Solution
Off
The CAN interface has
not been configured
---
Alternating red 50 ms /
green 50 ms
Configuration in progress ---
Alternating red 200 ms /
green 200 ms
Configuration invalid
Check the configuration in
the CODESYS
Configurator.
Green 200 ms / off 800
ms
The CANopen interface
has the status
“Stop”.
---
Green 200 ms / off 200
ms
The CANopen interface
has the status
“Preoperational”.
---
Green
The CANopen interface
has the status
“Operational”.
---
Red
The CANopen interface
has the status
“Bus Off”
(short-circuit or other
major fault).
Check the bus
connections and the baud
rate.
Error in the status
“Preoperational”
1* red flashing / 2 * green
flashing
“Bus Warning Level”
exceeded.
Check the wiring for the
CAN bus.
2* red flashing / 2 * green
flashing
“Guarding Error”, slave
incorrectly configured or
not available.
Check the slaves and the
configuration.
3* red flashing / 2 * green
flashing
“Sync Error”
Change the time interval
for the synchronization
message.
Error in the status
“Operational”
1* red flashing / green
800 ms on
“Bus Warning Level”
exceeded.
Check the wiring for the
CAN bus.
2* red flashing / green
800 ms on
“Guarding Error”
Check the slaves and the
configuration.
3* red flashing / green
800 ms on
“Sync Error”
Change the time interval
for the synchronization
message.