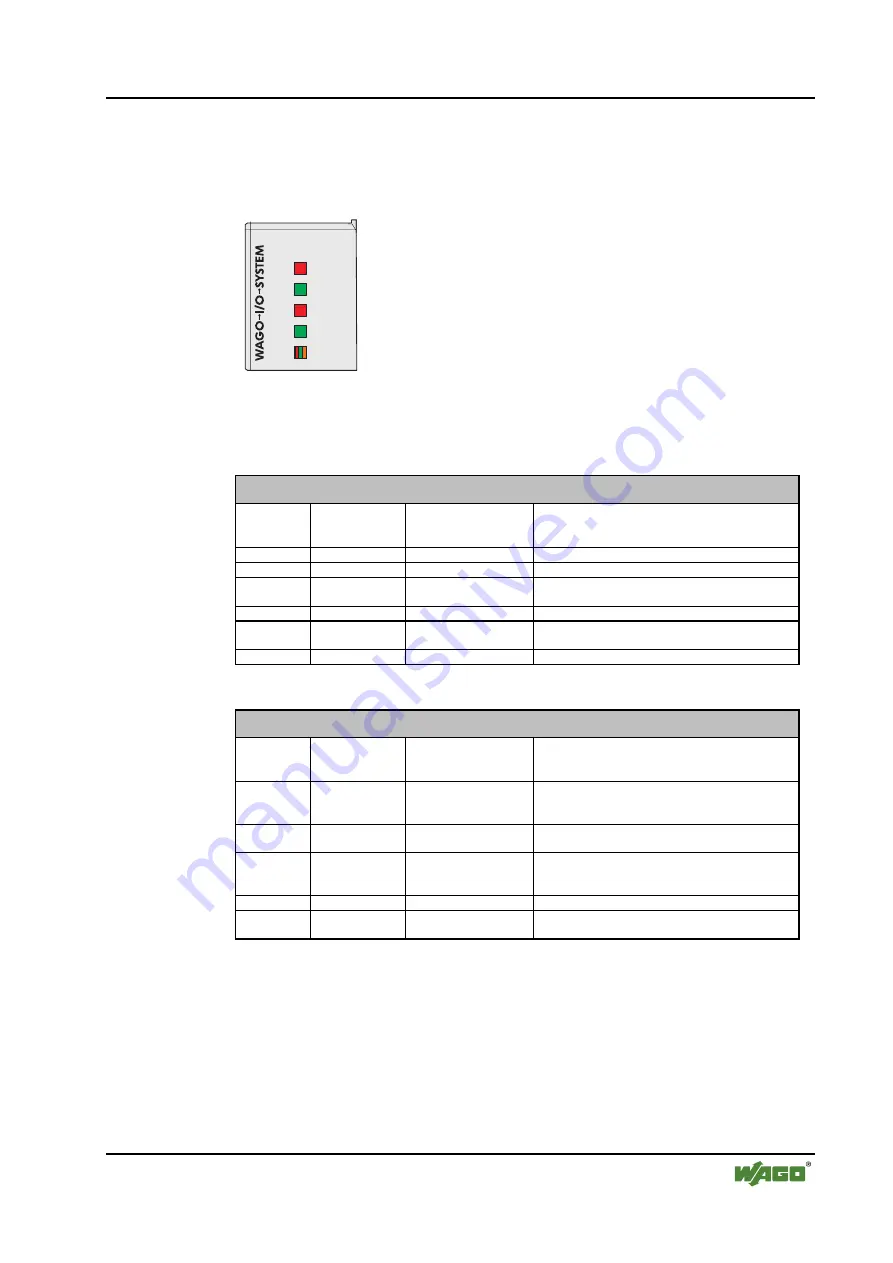
Fieldbus Coupler • 59
Fieldbus Coupler 750-346
WAGO-I/O-SYSTEM 750
DeviceNet
3.1.8 LED Display
The coupler possesses several LEDs for on site display of the coupler operat-
ing status or the complete node.
750-346
OVERFL
RUN
BUS OFF
DEVICENET
CONNECT
I/O
NS
MS
Fig. 3-18: Display elements 750-346
g034602x
The module status (MS) and the network status (NS) can be displayed by the
top 4 LED’s. They react as described in the table.
Module status
OVERFL
(red)
RUN
(green)
State of device
Meaning
off
off
no power
No power supply to the device.
off
on
device operational
The device operates correctly.
off
blinking
device in standby
The device needs to be configured or has been partly
configured.
blinking
off
minor fault
A minor fault has occurred. It exists a diagnostics.
on
off
unrecoverable fault
The device is defective, needs to be serviced or
replaced.
blinking
blinking
device self testing
The device performs a built-in check.
Table 3-1: Fault and status displays: MS
Network status
BUSOFF
(red)
CONNECT
(green)
State of device
Meaning
off
off
not powered, not online No power supply to the device / fieldbus supply /
DeviceNet cable not connected and „Duplicate MAC
ID detection“ is not yet completed.
off
blinking
online, not connected
The device operates correctly at the fieldbus. How-
ever, it has not yet been integrated by a scanner.
off
on
link ok online, con-
nected
The device operates correctly at the fieldbus. At
least one connection to another device has been
established.
blinking
off
connection time out
A minor fault has occurred.
on
off
critical link failure
The device has detected a fault. It is unable to per-
form any more functions in the network.
Table 3-2: Fault and status displays: NS