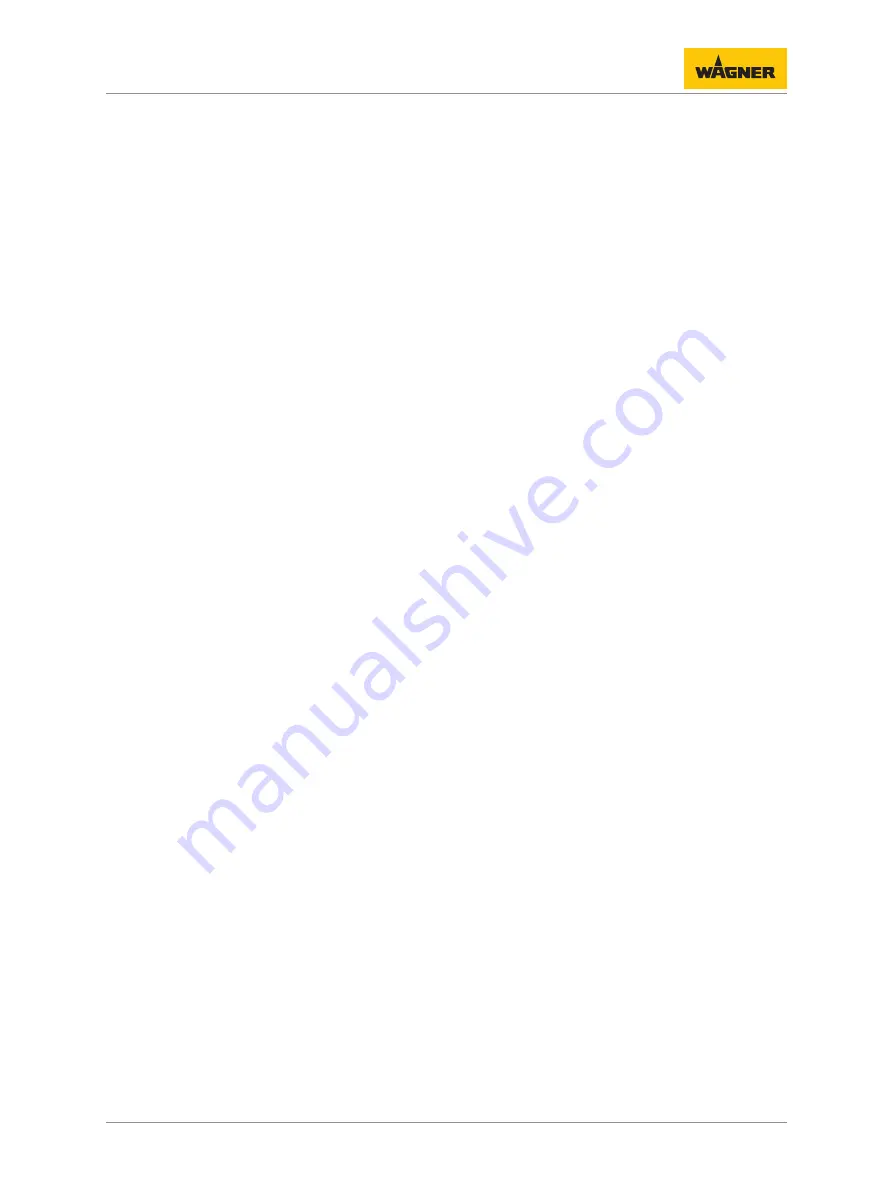
Operating manual Pneumatic double diaphragm pump ZIP52 (PF Eco) Finishing
8 Cleaning and Maintenance
38
Order number 2332848 | Edition 08/2020
8 CLEANING AND MAINTENANCE
8.1 CLEANING
8.1.1 Cleaning Personnel
Cleaning work should be undertaken regularly and carefully by qualified and trained
personnel. They should be informed of specific hazards during their training.
The following hazards may arise during cleaning work:
– risk to health from inhaling solvent vapors,
– use of unsuitable cleaning tools and aids.
8.1.2 Decommissioning and Cleaning
The device should be cleaned for maintenance purposes, etc. Ensure that no remaining
product dries on and sticks to the device.
1. Interrupt the work sequence in accordance with Chapter Pressure Relief / Work
35].
2. Carry out basic flushing in accordance with Chapter Basic Flushing [
3. Empty system in a controlled manner according to Chapter Emptying Pump [
4. Service spray gun in accordance to its operating manual.
5. Clean and check the suction system and the suction filter.
6. Clean the outside of the system.
7. Fully assemble the system.
8. Fill the system with flushing agent in accordance with Chapter Filling the Empty Pump
42].
8.1.3 Long-term Storage
If storing the system for a prolonged period of time, thorough cleaning and corrosion
protection are necessary. Replace the water or solvent in the product pump with a suitable
preserving oil.
1. Carry out decommissioning and cleaning (steps 1 to 7) in accordance with Chapter
Decommissioning and Cleaning [
2. Fill the system with preservation agent in accordance with Chapter Filling the Empty
3. Empty the system in a controlled manner in accordance with Chapter Emptying Pump
41] and seal the openings.
8.2 MAINTENANCE
8.2.1 Maintenance Personnel
Maintenance work should be undertaken regularly and carefully by qualified and trained
personnel. They should be informed of specific hazards during their training.
The following hazards may arise during maintenance work:
– risk to health from inhaling solvent vapors,
– use of unsuitable tools and aids.
A skilled person must ensure that the device is checked for being in a reliable state after
maintenance work is completed.