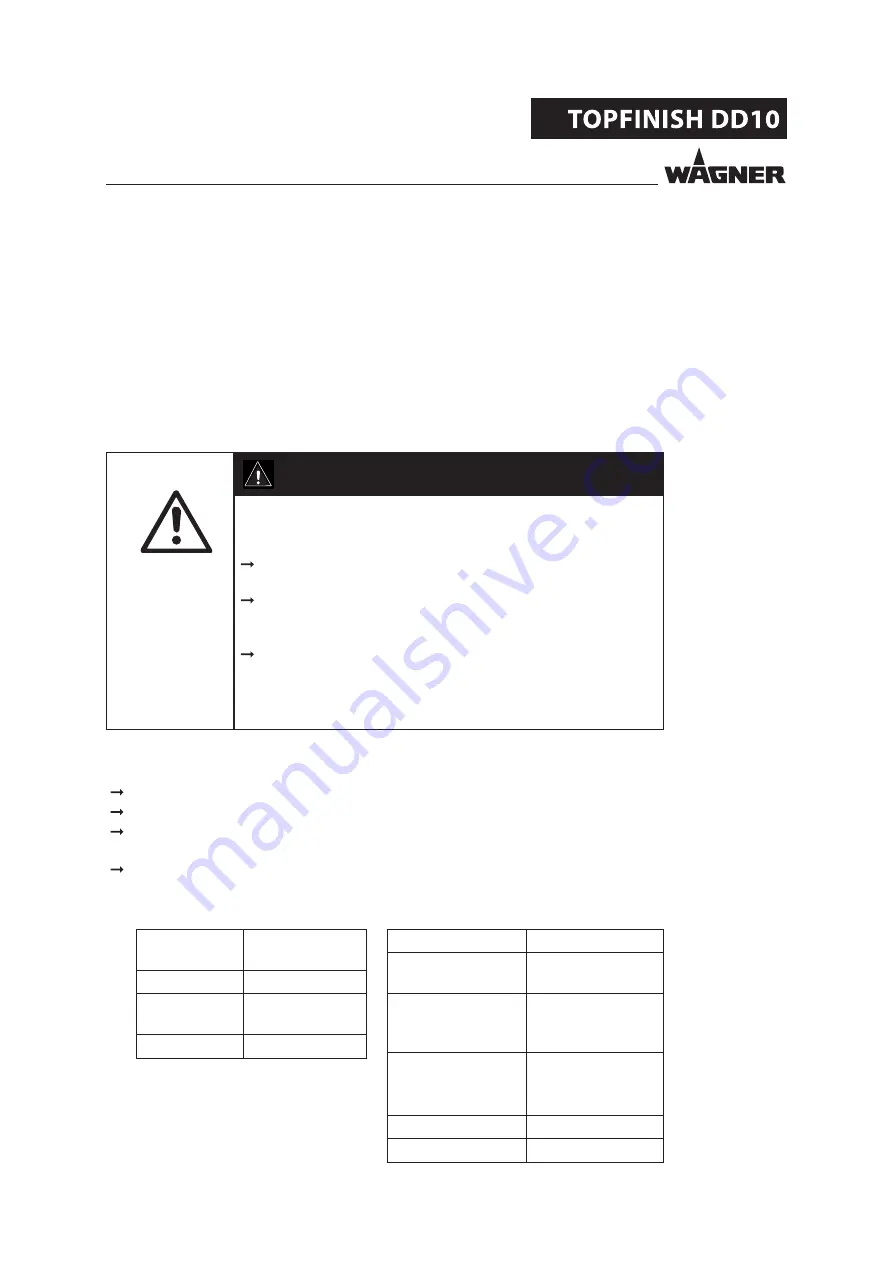
35
OPERATING MANUAL
VERSION 09/2016
ORDER NUMBER DOC 2366672
8.2.3.1
GROUNDING CHECK
Daily
Before starting work, carry out a visual check to ensure that the grounding connection is present in the
device and in all relevant components.
8.2.3
SAFETY CHECKS
WAGNER recommends having all spraying devices checked annually by a technical expert (e.g., a WAGNER
service technician) for safety reasons.
Bursting hose, bursting threaded joints!
Danger to life from injection of product and from fl ying parts.
Ensure that the hose material is chemically resistant to the
sprayed products and the used fl ushing agents.
Ensure that the spray gun, threaded joints, and product hose
between the device and the spray gun are suitable for the
generated pressure.
Ensure that the following information can be seen on the hose:
-
Manufacturer
- Permissible operating pressure
- Date of manufacture.
DANGER
The service life of the complete hoses between product pressure generator and application device is reduced
due to environmental infl uences even when handled correctly.
Check hoses, pipes, and couplings every day and replace if necessary.
Before every commissioning, check all connections for leaks.
Additionally, the operator must regularly check the complete hoses for wear and tear as well as for
damage at intervals that he/she has set. Records of these checks must be kept.
The complete hose is to be replaced as soon as one of the two following intervals has been exceeded:
– 6 years from the date of the hose crimping (see fi tting embossing).
– 10 years from the date of the hose imprinting.
Fitting
embossing
Meaning
xxx bar
Pressure
yymm
Crimping date
(year/month)
XX
Internal code
Hose imprinting
Meaning
WAGNER
Name /
Manufacturer
yymm
Date of
manufacture (year/
month)
xxx bar (xx MPa)
Pressure
e.g., 270 bar (27
MPa)
XX
Internal code
DNxx (e.g., DN10)
Nominal diameter
8.2.3.2
PRODUCT HOSES, TUBES AND COUPLINGS