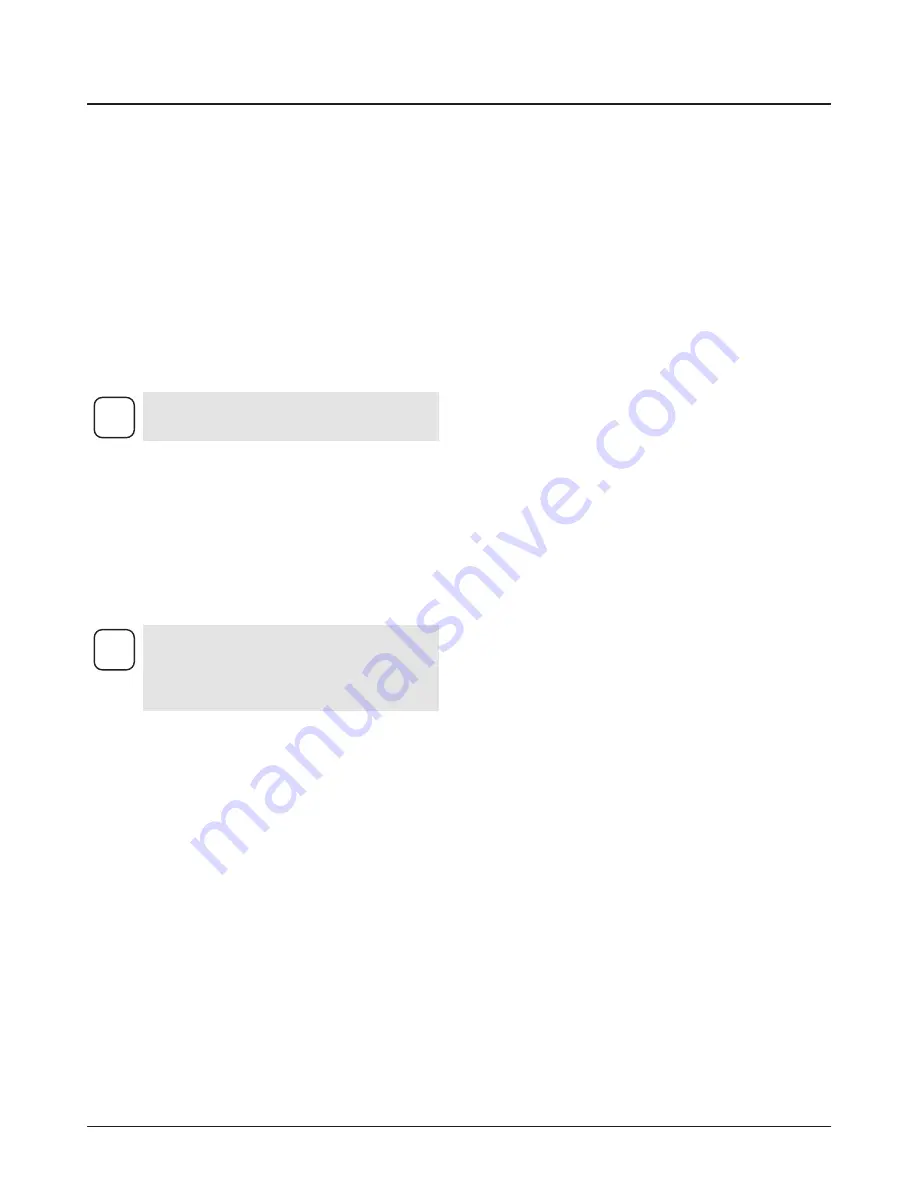
2.
General view of application
2.1
Application
All painting jobs in the workshop and on the building
site, small dispersion work with the spray gun or inter-
nally fed Airless roller.
Examples of objects of spraying
Doors, door frames, balustrades, furniture, wooden
cladding, fences radiators (heating) and steel parts, inter-
nal ceilings and walls.
2.2
Coating materials
Processible coating materials
Dilutable lacquers and paints or those containing sol-
vents, two-component coating materials, dispersions, la-
tex paints.
No other materials should be used for spraying without
WAGNER’s approval.
Filtering
Despite suction filter and insertion filter in the spray gun,
filtering of the coating material is generally advisable.
Stir coating material before commencement of work.
Viscosity
With this unit it is possible to process highly viscous
coating materials of up to around 20.000 MPa·s.
If highly viscous coating materials cannot be taken in by
suction, they must be diluted in accordance with the
manufacturer’s instructions.
Two-component coating material
The appropriate processing time must be adhered to ex-
actly. Within this time rinse through and clean the unit
meticulously with the appropriate cleaning materials.
Coating materials with sharp-edged additional
materials
These have a strong wear and tear effect on valves,
high-pressure hose, spray gun and tip. The durability of
these parts cane be reduced appreciably through this.
Attention:
Make sure, when stirring up with
motor-driven agitators that no air bubbles
are stirred in. Air bubbles disturb when
spraying and can, in fact, lead to interruption
of operation.
i
Pay attention to the Airless quality of the
coating materials to be processed.
i
3. Description of unit
3.1
Airless process
The main areas of application are thick layers of highly
viscous coating material for large areas and a high con-
sumption of material.
A piston pump takes in the coating material by suction
and conveys it to the tip. Pressed through the tip at a
pressure of up to a maximum of 230 bar (23 MPa), the
coating material is atomised. This high pressure has the
effect of micro fine atomisation of the coating material.
As no air is used in this process, it is described as an
AIRLESS process.
This method of spraying has the advantages of finest
atomisation, cloudless operation and a smooth, bubble-
free surface. As well as these, the advantages of the
speed of work and convenience must be mentioned.
3.2
Functioning of the unit
In the following there is a short description of the techni-
cal construction for better understanding of the function.
WAGNER ProSpray units are electrically driven high-
pressure spraying units.
A gear unit transfers the driving force to a crankshaft.
The crankshaft moves the pistons of the material feed
pump up and down.
The inlet valve is opened automatically by the upwards
movement of the piston. The outlet valve is opened
when the piston moves downward.
The coating material flows under high pressure through
the high-pressure hose to the spray gun. When the coat-
ing material exits from the tip it atomizes.
The pressure regulator controls the volume and the oper-
ating pressure of the coating material.
ProSpray 22
g
General view of application
Description of unit