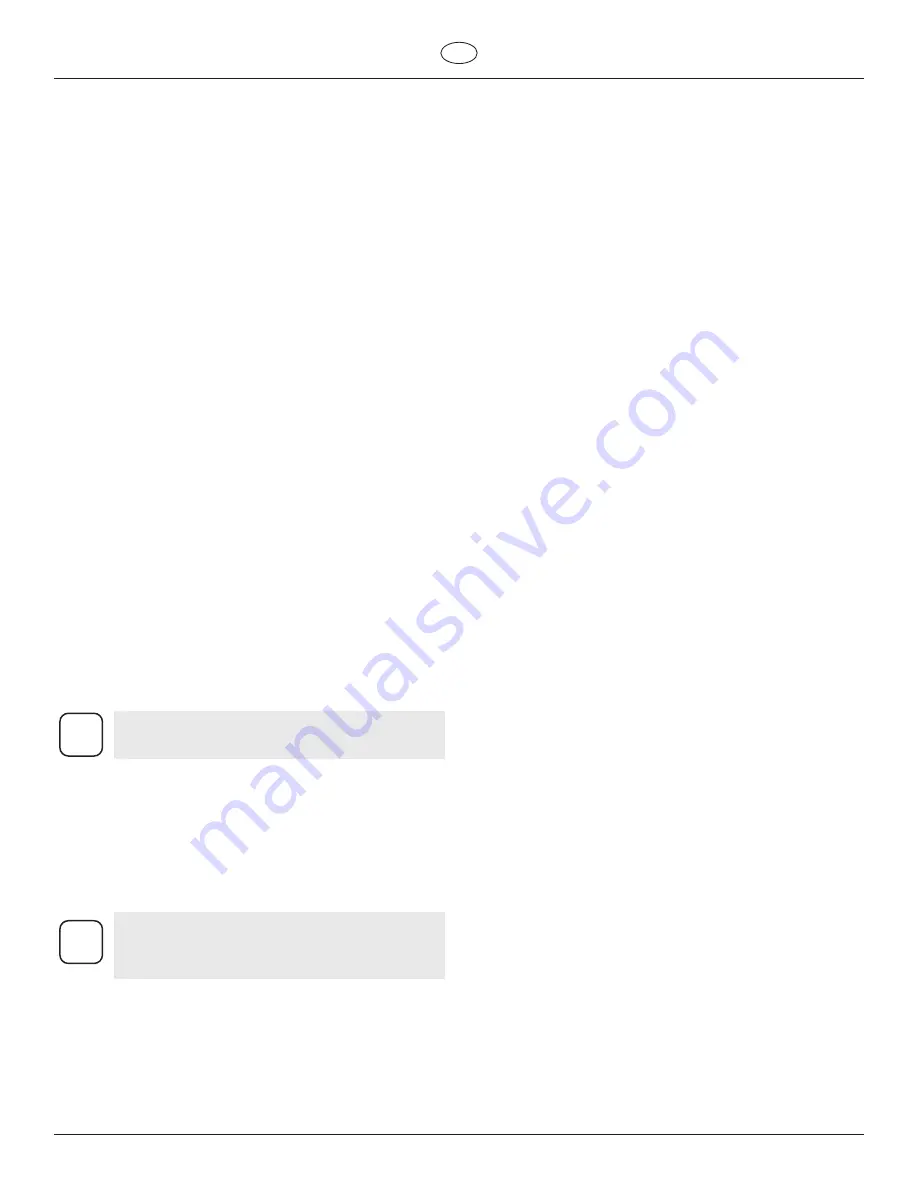
6
P20
GB
Safety regulations
Description of unit
Work or repairs at the electrical equipment:
These may only be carried out by a skilled electrician. No liability is
assumed for incorrect installation.
A list of the materials used in the construction of the equipment
will be made available on request to validate compatibility with the
coating materials to be used.
Operating Temperature
This equipment will operate correctly in its intended ambient, at a
minimum b10°C and +40°C.
Relative Humidity
The equipment will operate correctly within an environment at 50%
RH, +40°C. Higher RH may be allowed at lower temperatures.
Measures shall be taken by the Purchaser to avoid the harmful effects
of occasional condensation.
Altitude
This equipment will operate correctly up to 2100 m above mean sea
level.
Transportation and Storage
This equipment will withstand, or has been protected against,
transportation and storage temperatures of -25°C to +55°C and for
short periods up to +70°C.
It has been packaged to prevent damage from the effects of normal
humidity, vibration and shock.
2.
General view of application
2.1
Application
All painting jobs in the workshop and on the building site, small
dispersion work with the spray gun or inter nally fed Airless roller.
Examples of objects of spraying
Doors, door frames, balustrades, furniture, wooden cladding, fences
radiators (heating) and steel parts, internal ceilings and walls.
2.2
Coating materials
Processible coating materials
i
Pay attention to the Airless quality of the coating
materials to be processed.
Dilutable lacquers and paints or those containing solvents, two-
component coating materials, dispersions, latex paints.
No other materials should be used for spraying without
WAGNER’
s
approval.
Filtering
Despite suction filter and insertion filter in the spray gun, filtering of
the coating material is generally advisable.
Stir coating material before commencement of work.
i
Attention: Make sure, when stirring up with motor-
driven agitators that no air bubbles are stirred in. Air
bubbles disturb when spraying and can, in fact, lead
to interruption of operation.
Viscosity
With this unit it is possible to process highly viscous coating materials
of up to around 20.000 MPa·s.
If highly viscous coating materials cannot be taken in by suction, they
must be diluted in accordance with the manufacturer’s instructions.
Two-component coating material
The appropriate processing time must be adhered to exactly. Within
this time rinse through and clean the unit meticulously with the
appropriate cleaning materials.
Coating materials with sharp-edged additional materials
These have a strong wear and tear effect on valves, high-pressure
hose, spray gun and tip. The durability of these parts cane be reduced
appreciably through this.
3.
Description of unit
3.1
Airless process
The main areas of application are thick layers of highly viscous
coating material for large areas and a high consumption of material.
A piston pump takes in the coating material by suction and conveys it
to the tip. Pressed through the tip at a pressure of up to a maximum
of 214 bar (21.4 MPa), the coating material is atomised. This high
pressure has the effect of micro fine atomisation of the coating
material.
As no air is used in this process, it is described as an AIRLESS process.
This method of spraying has the advantages of finest atomisation,
cloudless operation and a smooth, bubble-free surface. As well as
these, the advantages of the speed of work and convenience must
be mentioned.
3.2
Functioning of the unit
In the following there is a short description of the technical
construction for better understanding of the function.
Wagner P20 units are electrically driven high-pressure spraying units.
A gear unit transfers the driving force to a crankshaft. The crankshaft
moves the pistons of the material feed pump up and down.
The inlet valve is opened automatically by the upwards movement
of the piston. The outlet valve is opened when the piston moves
downward.
The coating material flows under high pressure through the high-
pressure hose to the spray gun. When the coating material exits from
the tip it atomizes.
The pressure control knob controls the volume and the operating
pressure of the coating material.