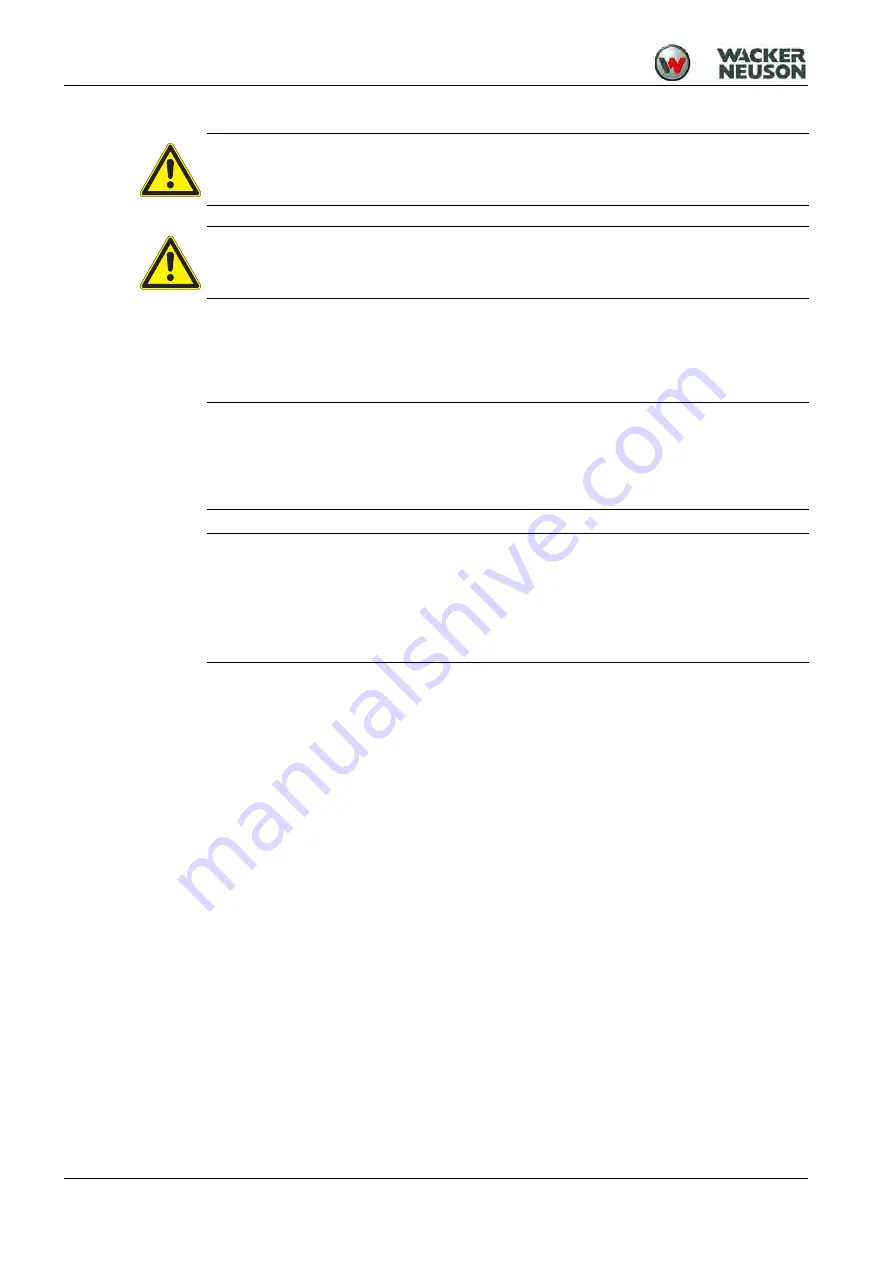
9 Maintenance
30
100_0202_mt_0013.fm
Cleaning the air cleaner
1. Remove the wing nuts and air cleaner cover.
2. Remove and separate the air cleaner cartridge.
3. Check both applications for holes and cracks and replace if damaged.
WARNING
Risk of fire and explosion!
Do not use any gasoline or cleaning solution to clean the air cleaner cartridge.
CAUTION
Do not run the engine without an air cleaner. This will quickly lead to engine wear.
NOTICE
Foam insert:
Wash out the insert in a solution of household detergent and warm water and then rinse
thoroughly. Allow the insert to dry and tip into clean motor oil. Press out excessive oil. If
too much oil remains in the insert, the engine will smoke during its first start.
NOTICE
Paper insert:
Gently tap the insert several times against a hard surface to remove excess grime. Blow
compressed air from the inside to the outside through the filter. Do not brush the dirt off as
it will get pressed into the fibers.
In the event of extreme dirt accumulation, replace the insert.
Summary of Contents for WP Series
Page 42: ...14 Emission control systems information and warranty 42 100_0000_0020 fm...
Page 47: ......
Page 48: ......