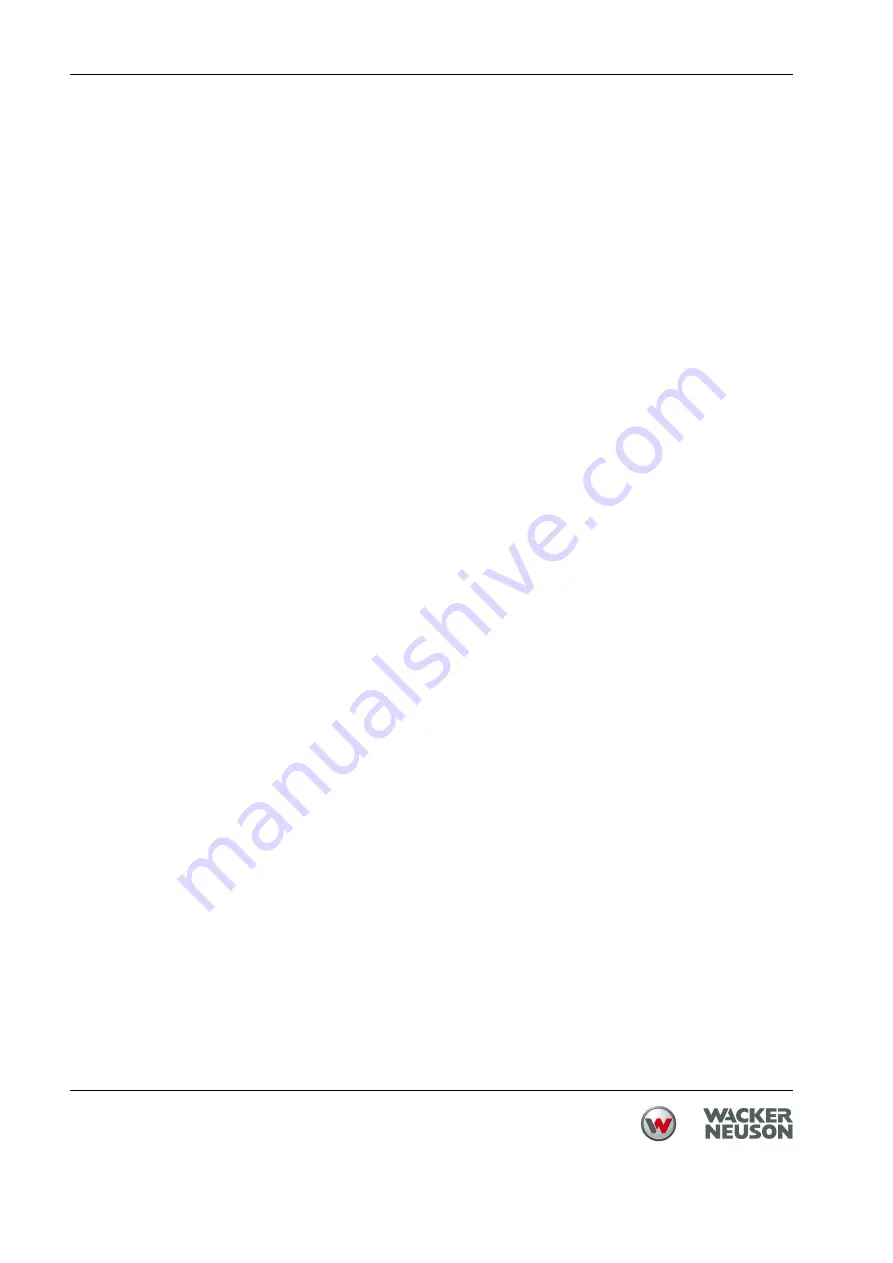
5 Structure and function
26
This procedure is hydraulically controlled with the control handle (3) on the guide
handle head (4).
The drive motor (13) attached to the upper mass (5) powers the exciter (9). The
torque is transferred non-positively by the centrifugal clutch (7) and the exciter
V-belt (8).
When the motor speed is low, the centrifugal clutch (7) interrupts the power flow
to the exciter (9) which allows the drive motor (13) to idle properly. The speed of
the drive motor (13) can be varied at the throttle lever (2).
The upper mass (5) and the base plate (10) are connected to each other via
4 vibration-damping vibration dampers (6). This damping prevents very high fre-
quencies from being transferred to the upper mass (5). This maintains proper
functioning of the drive motor (13) despite a high compaction capacity.
Depending on machine type, the drive motor may also include an electronic start-
er in addition to the recoil starter.
The combustion air is aspirated via an air cleaner. The condition of the air clean-
er can be checked using the air cleaner maintenance indicator.
Summary of Contents for DPU 3050H
Page 46: ...9 Maintenance 46 8 Close filler hole and use a torque wrench to tighten it to 100 Nm...
Page 48: ...9 Maintenance 48 11 If necessary retighten the screws...
Page 60: ...13 Technical data 60...
Page 62: ......
Page 63: ......