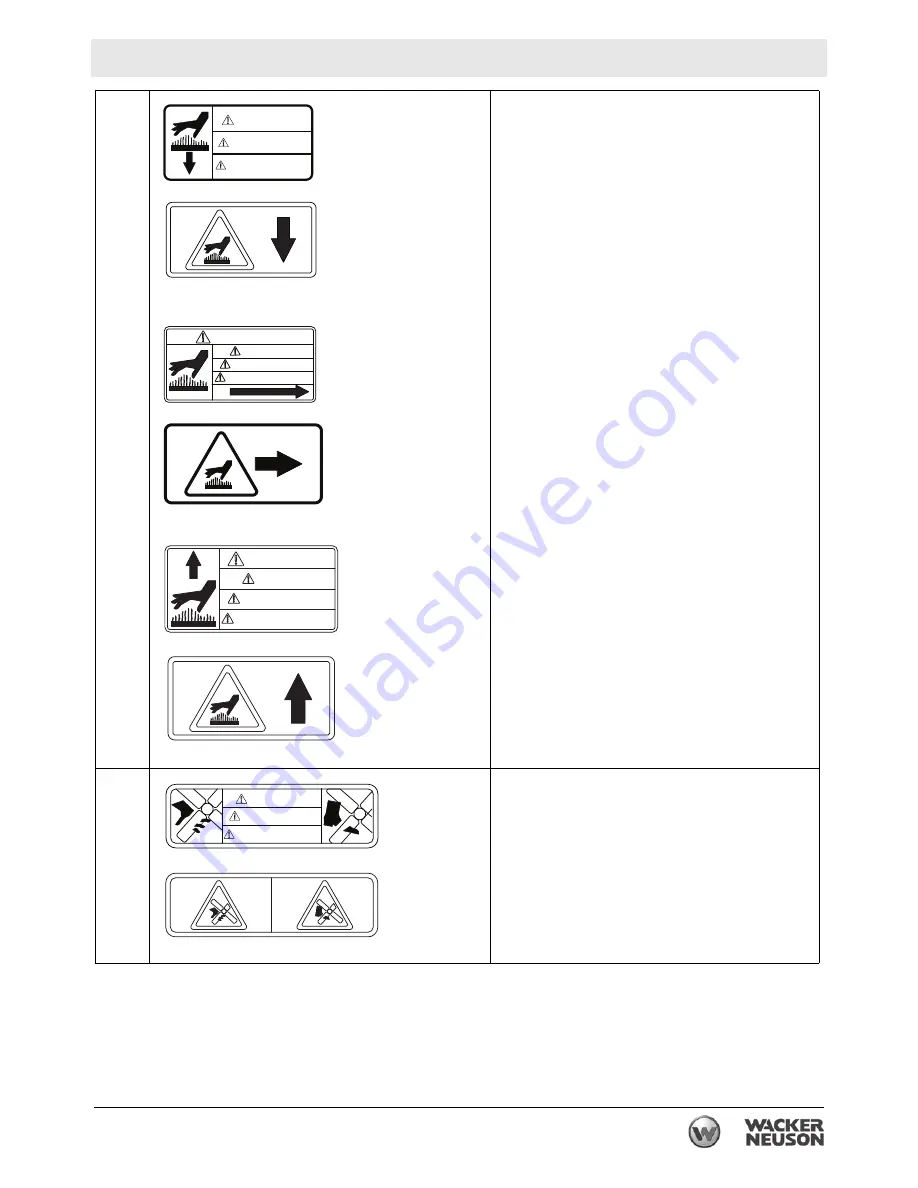
wc_si000970gb_FM10.fm
23
CRT48
Labels
F
WARNING
Hot surface
G
WARNING
Cutting hazard. Keep hands and feet away
from blades. Always replace blade guard.
117039
ADVERTENCIA
ADVERTENCIA
AVERTISSEMENT
AVERTISSEMENT
WARNING
WARNING
178713
178713
WARNUNG
WARNUNG
ADVERTENCIA
ADVERTENCIA
WARNING
WARNING
AVERTISSEMENT
AVERTISSEMENT
117037
117037
178732
178732
WARNING
WARNING
5200007832
5200007832
AVERTISSEMENT
AVERTISSEMENT
ADVERTENCIA
ADVERTENCIA
WARNUNG
WARNUNG
5200007834
5200007834
111453
111453
AVERTISSEMENT
AVERTISSEMENT
ADVERTENCIA
ADVERTENCIA
WARNING
WARNING
178740
178740
Summary of Contents for CRT48-35L
Page 6: ...6...
Page 10: ...Table of Contents CRT48 10...
Page 19: ...wc_si000969gb_FM10 fm 19 CRT48 Safety Information Notes...
Page 80: ...wc_td000668gb_FM10 fm 80 Technical Data CRT48 Notes...
Page 93: ......
Page 106: ...AEM_ConcretePowerTrowel qxd 7 23 03 6 31 AM Page 1...
Page 107: ...CRT 48 Schematics wc_tx004197gb_FM10 fm 107 14 Schematics Notes...
Page 114: ......
Page 115: ......