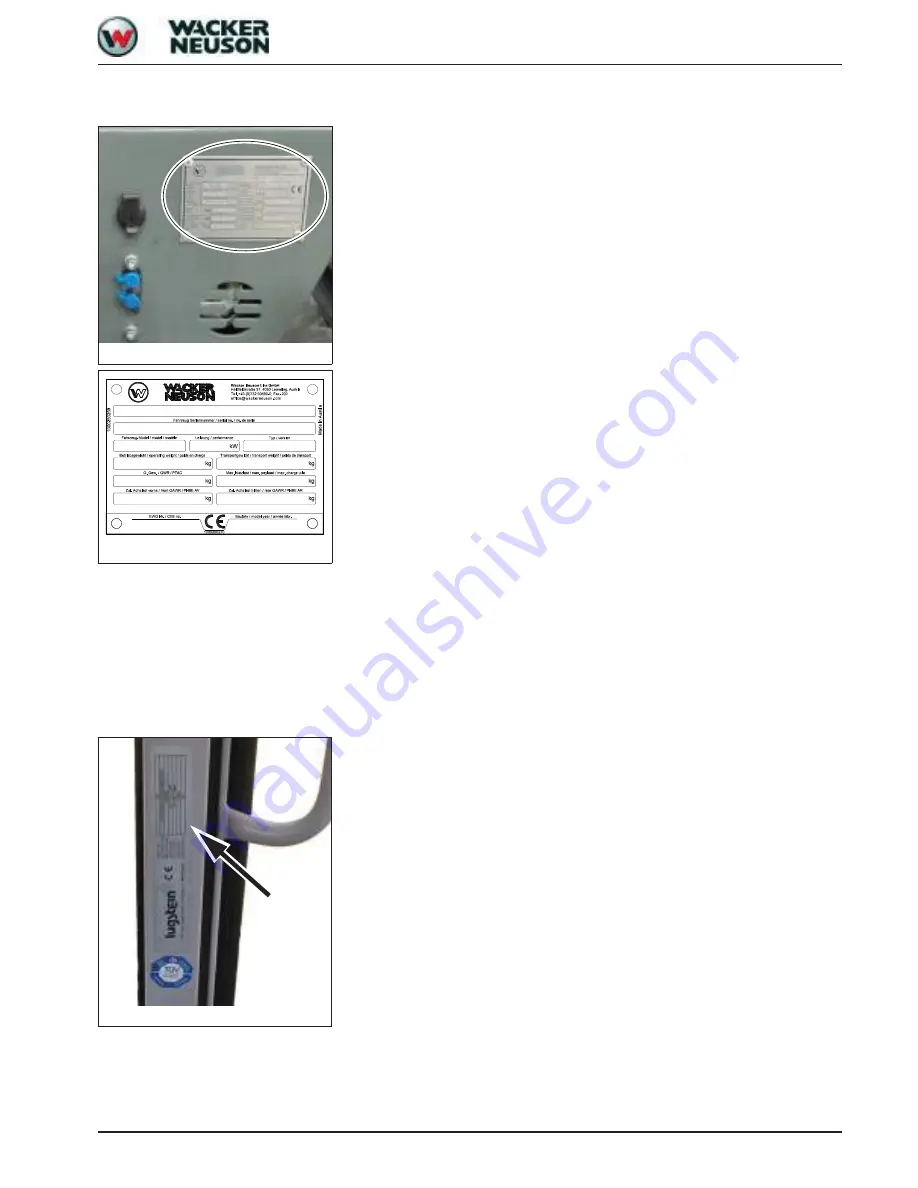
SHB 28Z3 EN – Edition 2.0 * 28z3s110.fm
1-5
Operation
1.4
Type labels and component numbers
Serial number
The serial number is stamped on the machine chassis. It is also located on the type label.
The type label is located at the front left on the machine chassis, under the control stand.
Type label information
Field below Wacker Neuson logo:
HYDRAULIC EXCAVATOR
Fahrzeug Seriennummer/serial no./no. de série:
Serial number of machine
Fahrzeug Modell/model/modèle:
Machine designation
Leistung/performance:
Engine output
Typ/version:
Machine type
Betriebsgewicht/operating weight/poids en charge:
Operating weight
Transportgewicht/transport weight/poids en transport:
Transport weight
G. Gew./GWR/PTAC:
Gross weight rating (admissible)
Max. Nutzlast/max. payload/max. charge utile:
Maximum payload
Zul. Achslast vorne/front GAWR/PNBE AV:
Front gross axle weight rating
Zul. Achslast hinten/rear GAWR/PNBE AR:
Rear gross axle weight rating
Option
EWG Nr./CEE no.:
EEC check number
Baujahr/model year/année fabr.:
Year of construction
Other information
– see chapter 2
Specifications
on page 2-2
Cab number
The type label (arrow) is located on the chassis of the cab, at the upper left beside the
door.
Fig. 1:
Type label: location
Fig. 2:
Type label
HYDRAULIC EXCAVATOR
Fig. 3:
Cab type label
Summary of Contents for 28Z3
Page 10: ...I 8 SHB 28Z3 EN Edition 2 0 28Z3s20IVZ fm...
Page 11: ...Operation...
Page 27: ...Specifications...
Page 46: ...2 20 SHB 28Z3 EN Edition 2 0 28z3s210 fm Specifications...
Page 47: ...Maintenance...
Page 113: ...Engine...
Page 132: ...4 20 SHB 28Z3 EN Edition 2 0 28z3s410 fm Engine...
Page 133: ...Hydraulic system...
Page 169: ...bersicht der Hydraulikpl...
Page 174: ......
Page 175: ...Electrical system...
Page 184: ...6 10 SHB 28Z3 EN Edition 2 0 28z3s610 fm Electrical system...
Page 185: ...Die Stromlaufpl ne und K Optionen...
Page 187: ......
Page 188: ......
Page 199: ...SHB 28Z3 EN Edition 2 0 28z3s612 fm 6 25 Electricalsystem...
Page 200: ...6 26 SHB 28Z3 EN Edition 2 0 28z3s612 fm Electrical system...
Page 201: ...Options...
Page 204: ...7 4 SHB 28Z3 EN Edition 2 0 28z3s710 fm Options Installation...
Page 230: ...7 30 SHB 28Z3 EN Edition 2 0 28z3s710 fm Options...
Page 231: ...PowerTilt PTS06...