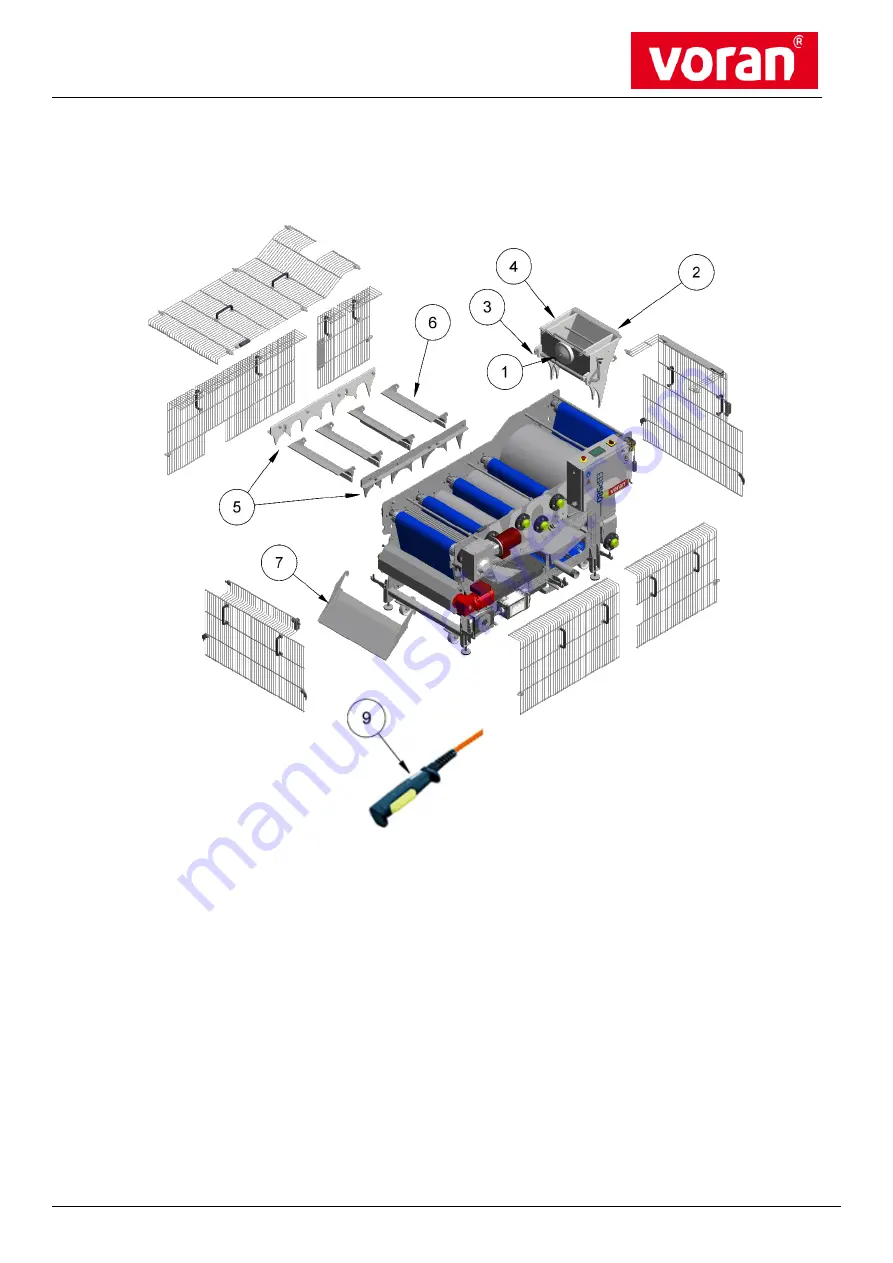
Single belt press EBP580
Version: 166000000, M0017267B_EN208-240-60D
Date: 28.11.2017
- 48 / 52 -
First clean any installed Washing Machine or serially connected mill and then clean the press as
follows:
Picture 10.5.1-1) Cleaning the Belt press
1.) Remove protective grating.
2.) Unscrew the cable from dosing switch (Fig. Pos. 1).
3.) Pull out safety end-switch (Fig. Pos. 2).
4.) Open the locking hooks (Fig. Pos. 3) and remove dosing tank (Fig. Pos. 4).
5.) Remove mash conveyor (Fig. Pos. 5), scrapers (Fig. Pos. 6) and end scrapers (Fig. Pos. 7).
6.) Start cleaning mode.