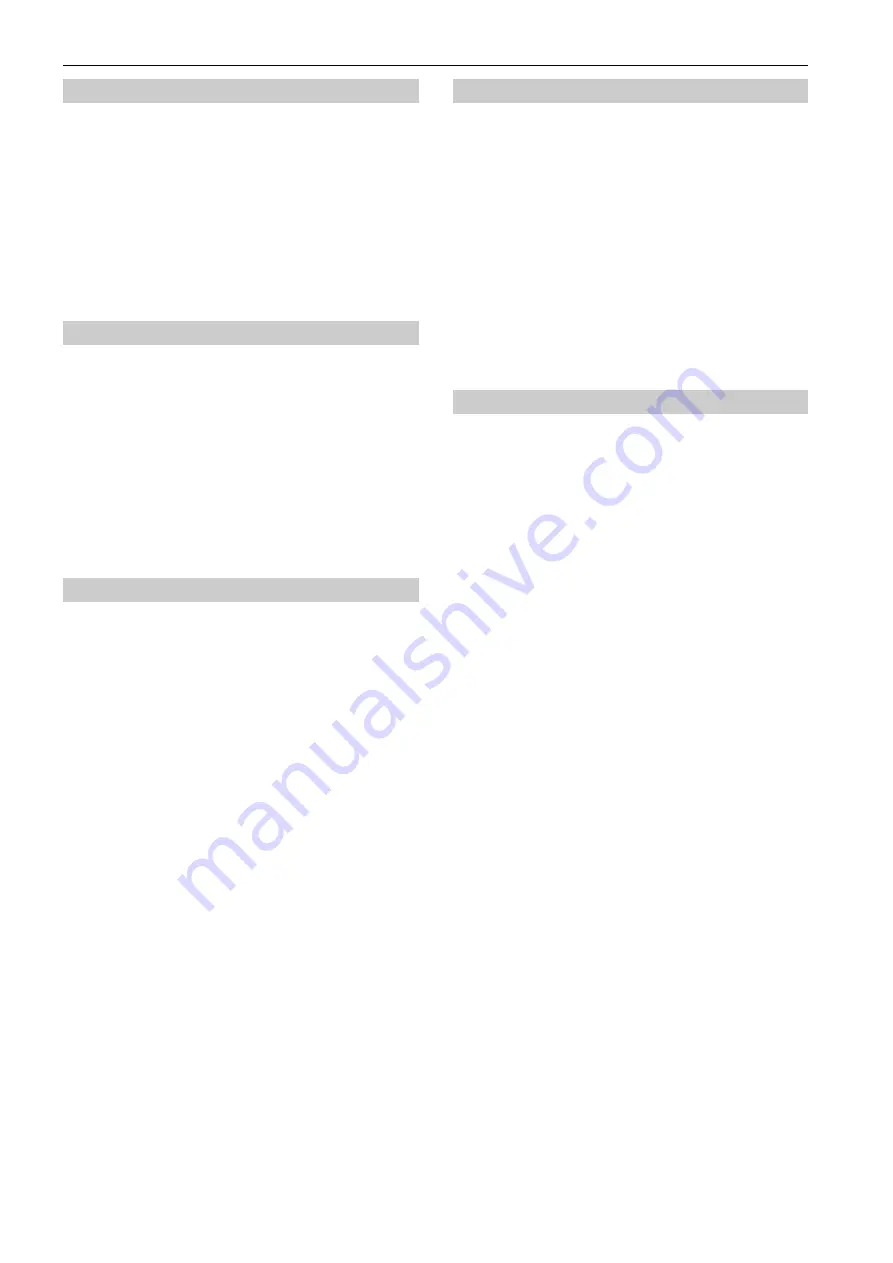
74
Diagnostic function
Code 2.3 Fuel injection pump
Cause: The actuator is drawing excessive, too little or no
current.
Consequence: The engine stops.
Corrective action:
• Check the connections for the injection pump (the actua-
tor) and the control module.
• Erase the diagnostic trouble code (DTC).
• Start the engine.
• Contact an authorized workshop if the fault persists.
Code 2.4 Engine speed (RPM) sensor
Cause: The engine speed (RPM) sensor transmits no sig-
nal to the control module at start.
Consequence: The engine does not start/The starter mo-
tor is not activated.
Corrective action:
• Check the connections for the engine speed (RPM) sen-
sor, the starter relay and the control module.
• Erase the diagnostic trouble code (DTC).
• Start the engine.
• Contact an authorized workshop if the fault persists.
Code 2.5 Engine speed (RPM) sensor
Cause: The engine speed (RPM) sensor transmits abnor-
mal values to the control module during operation.
Consequence: The engine stops.
Corrective action:
• Check the connections for the injection pump (the actua-
tor) and the control module.
• Erase the diagnostic trouble code (DTC).
• Start the engine.
• Contact an authorized workshop if the fault persists.
Code 2.6 Potentiometer
Cause: Short-circuit or open-circuit in the power supply to
the potentiometer in the control.
Consequence: The gear is disengaged and the engine
speed (RPM) is set to 1000 rpm.
NOTE! The fault applies to the relevant control position
(the boat can be driven from another control position if
there are multiple control positions).
Corrective action:
• Check the wiring and connections leading to the control.
• Erase the diagnostic trouble code (DTC).
• Start the engine.
• Emergency shifting is possible if the fault remains: See
the “Troubleshooting” chapter.
Code 2.7 Potentiometer
Cause: The control module receives no information from
the potentiometer in the control (applies to the potentiome-
ter for the engine speed lever in dual lever controls).
Consequence: The gear is disengaged and the engine
speed (RPM) is set to 1000 rpm.
NOTE! The fault applies to the relevant control position
(the boat can be driven from another control position if
there are multiple control positions).
Corrective action:
• Check the wiring and connections leading to the control.
• Erase the diagnostic trouble code (DTC).
• Start the engine.
• Emergency shifting is possible if the fault remains: See
the “Troubleshooting” chapter.
Summary of Contents for TAMD74C
Page 1: ...OPERATOR S MANUAL TAMD74C L P ...
Page 81: ...79 Notes ...
Page 82: ...80 Notes ...
Page 87: ......
Page 88: ...7740639 5 English 10 2000 ...