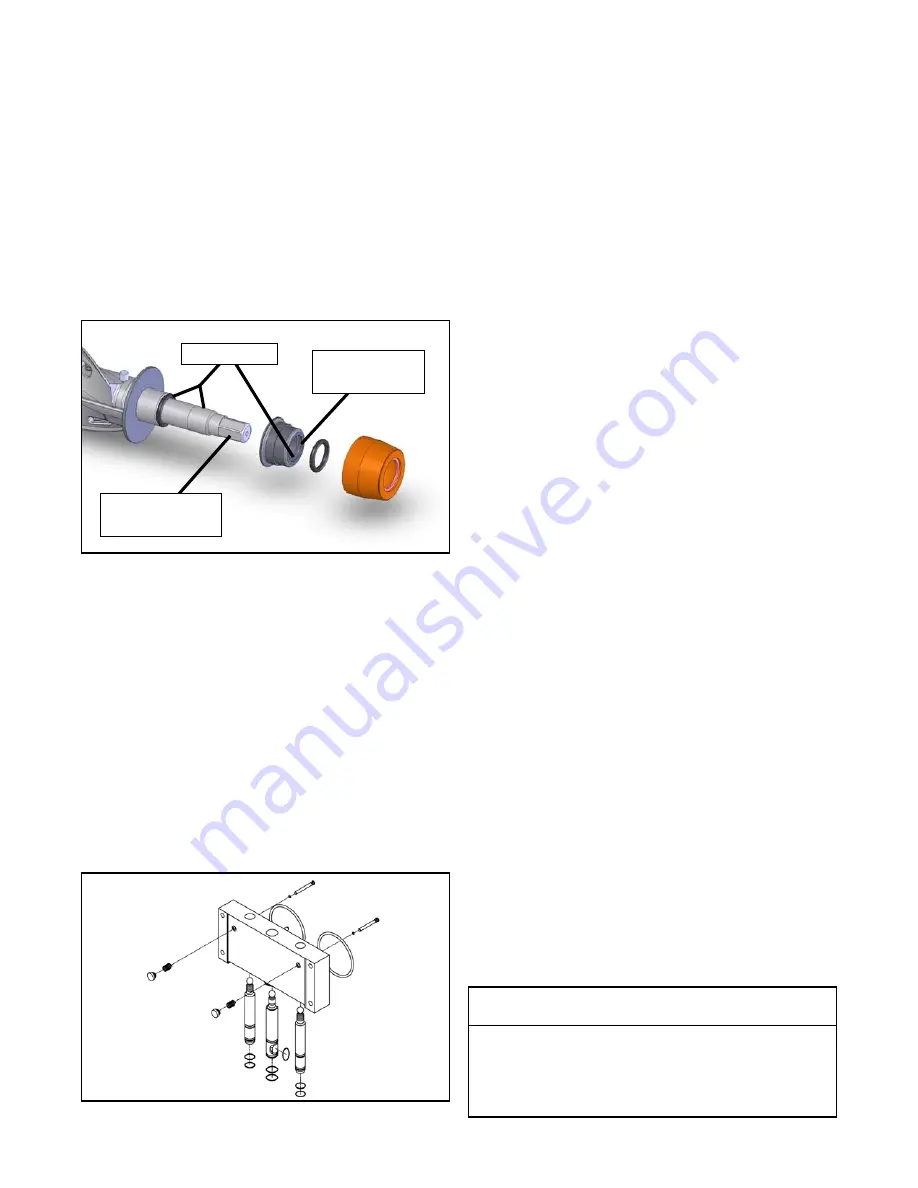
12
A.
Assemble all o-rings onto parts dry, without
lubrication. Then apply a thin film of sanitary
lubricant to exposed surfaces of the o-rings.
B.
Lubricate the rear seal area on the auger shaft with
a thin layer of sanitary lubricant. Install the rear
seal o-ring. Lubricate the outside of the rear seal o-
ring with sanitary lubricant.
C.
Install the stainless steel rear seal adapter into the
rear seal dry (without lubricant). Lubricate the
inside surface of the rear seal adapter, including
the adapter o-ring, and install it onto the auger
shaft. DO NOT lubricate the outside of the rear seal
adapter (Fig. 3-6).
D.
Lubricate the hex drive end of the auger with a small
amount of hex drive anti seize. A small container
of anti seize is shipped with the machine.
E.
Screw the springs onto the studs in the plastic
flights. The springs must be screwed into the
flights completely to provide proper compression.
F.
Install the two plastic flights onto the rear of the
auger and insert it part way into the freezing
cylinder.
G.
Install the remaining plastic flights, push the auger
into the freezing cylinder and rotate slowly until the
auger engages the drive shaft.
H.
Apply a thin layer of sanitary lubricant to the inside
and outside of the auger support bushing. Install
the bushing onto the auger support and install the
auger support into the front of the auger. Rotate
the auger support so that one leg of the support
points straight up.
H.
Assemble the air bleed valve o-ring onto the air
bleed valve. Position the o-ring into the groove
close to the wide part. Apply a thin film of sanitary
lubricant to the o-ring.
I.
Insert the air bleed valve into the back of the front
door. Install the compression spring onto the air
bleed valve then screw the knob on finger tight.
J.
Apply a thin layer of sanitary lubricant to the o-rings
on the spigot body and install the spigot body
through the bottom of the front door.
K.
Apply a thin film of sanitary lubricant to the door
seal o-ring and fit it into the groove on the rear of
the front door.
M.
Place the front door assembly on the mounting
studs and the push front door against the machine
carefully.
N.
Secure the front door to the machine by placing
the knobs on the studs and tightening until finger
tight. Do not overtighten. Proper o-ring seal can
be observed through the transparent front door.
3.9 SANITIZING
Sanitizing must be done after the machine is clean and just
before the machine is filled with mix. Sanitizing the night
before is not effective. However, you should always clean
the machine and parts after using it.
NOTE
The United States Department of Agriculture and
the Food and Drug Administration require that all
cleaning and sanitizing solutions used with food pro-
cessing equipment be certified for this use.
When sanitizing the machine, refer to local sanitary regu-
lations for applicable codes and recommended sanitizing
products and procedures. The frequency of sanitizing
must comply with local health regulations. Mix sanitizer
according to manufacturer’s instructions to provide a 100
parts per million strength solution. Mix sanitizer in quanti-
ties of no less than 2 gallons of 90°F to 110°F (32°C to
43°C) water. Allow sanitizer to contact the surfaces to be
sanitized for 5 minutes. Any sanitizer must be used only in
accordance with the manufacturer’s instructions.
CAUTION
Risk of Product Damage
Avoid prolonged contact of sanitizer with machine
parts. Sanitizer may cause corrosion of stainless
steel parts if there is prolonged contact.
Figure 3-7 Front Door
Figure 3-6 Rear Seal Assembly
Hex Drive
Anti Seize
Petrol-Gel
Place O-Ring
Inside Insert
Summary of Contents for STOELTING O431RC
Page 1: ...Model O431RC OPERATORS MANUAL Manual No 513664 Rev 2 ...
Page 2: ......
Page 34: ...28 ...
Page 38: ...32 ...