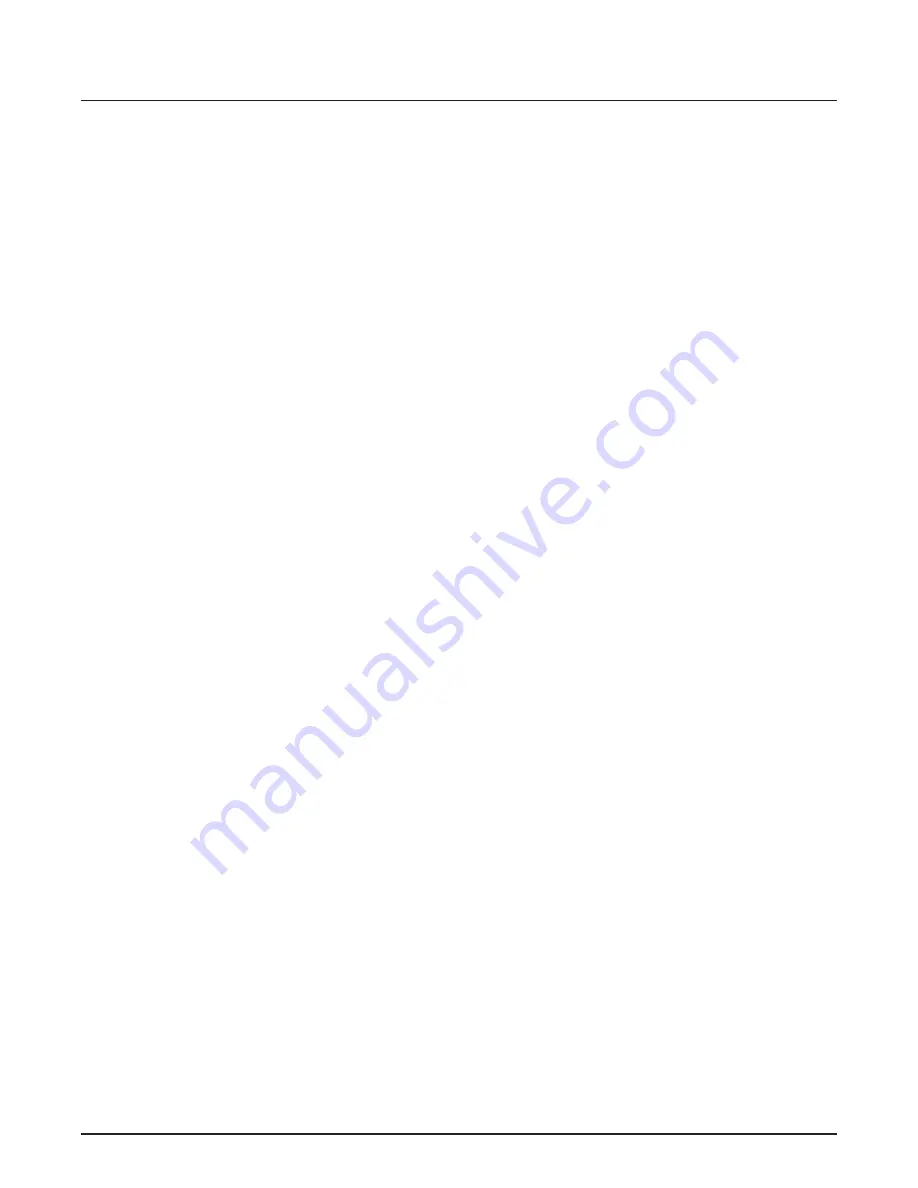
Owner’s Manual #513666
17
M202B Model Machines
Section 4 - Troubleshooting
4.1 ERROR CODES
When the machine experiences a problem, one of the
following error codes is displayed on the control panel.
Each error code directs you to the system location of the
malfunction.
ERROR CODE MALFUNCTION
1
Soft
2
High Torque
3
Extended Run Time
4
Clean
5
Barrel Sensor
6
Hopper Sensor
7
Drive Motor
8
Cab Sensor
9
High Pressure Cutout
10
Auxiliary Sensor
12
Hopper Sensor
13
Hopper Sensor
To return the machine to normal operation, any error
causing condition must be corrected and the Freezing
Cylinder Off/On switch must be placed in the OFF position
and back in the ON position before the machine returns
to normal operation.
4.2 TROUBLESHOOTING ERROR CODES
Error Code 1 - Soft Error
The Soft Error (E1) is an internal control board error
that is logged for future analysis. The refrigeration
is never stopped and the machine continues to
operate normally.
Error Code 2 - High Torque
If the control panel displays a High Torque Error
(E2), the drive motor is running at a high load for
10 or more seconds. Place the Freezing Cylinder
Off/On switch in the OFF position, wait until the
product in the barrel thaws to a reasonably soft
consistency and return the switch to the ON
position. If the error persists, contact White Glove
Service for further assistance.
Error Code 3 - Run Time
The Run Time Error (E3) occurs when the
compressor runs continuously for an extended
period. This error could happen if the cutout
value is not attained during “Standby Mode” or if
the “Ready” signal does not come on in “Custard
Mode” or “Italian Ice Mode”.
This error is generally caused by very low mix
levels in the hopper or from product breakdown.
Check the mix in the hopper. If the level mix is
low, add mix. If there is a possibility that the mix
has broken down, clean and sanitize the machine
and replace the mix with fresh product.
Ice crystals in the hopper can clog the mix inlet
system and prevent mix from entering the freezing
cylinder. Thoroughly thaw mix per manufacturer’s
recommendations. To check for ice crystals, pour
a small amount of product from the mix container
through a clean and sanitized sieve or strainer. If
ice crystals are in the mix, check temperature of
the walk-in cooler where the mix is stored.
If the error persists after attempting to clear it,
contact White Glove Service for further assistance.
Error Code 4 - Clean
If the machine is left in the Clean Mode for more
than 10 minutes, the control panel displays a Clean
Error (E4). This condition does not reflect a problem
with the machine itself. The Clean Error has been
programmed into the controller as a safeguard
to protect the machine from potential damage
caused by the machine being accidentally left
in “Clean Mode”. The control attempts to restart
itself after 5 minutes. The display then flashes and
reads Restart. To immediately clear the Clean Error,
place the Freezing Cylinder Off/On switch in the
OFF position and back in the ON position. After
the Clean Error has been cleared, the machine
starts a refrigeration cycle to protect the product
in case the clean button was pressed by mistake.