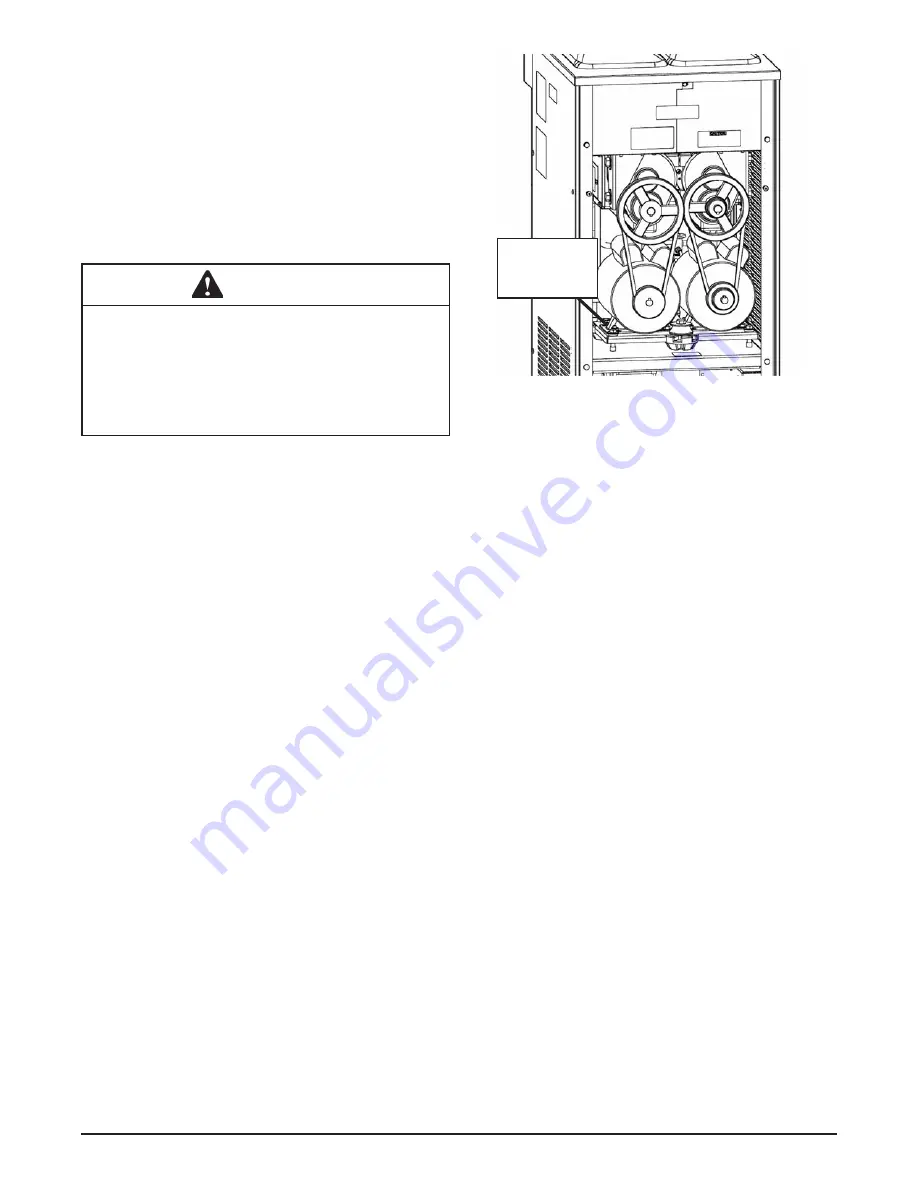
Service Manual #513659
38
Model F231
B. DRIVE MOTOR REMOVAL
1.
Disconnect machine from electrical supply before
removing any panels for servicing.
2.
Remove the back panel and the side panel.
3.
Remove the electrical cover plate from the back
of the motor.
4.
Identify (mark) wires and remove them from the
motor.
5.
Loosen the belt tension adjustment bolt and
remove the belt. (Refer to Figure 6-3)
7.
Remove the motor mounting bolts.
8.
Loosen the two allen head screws from the pulley.
9.
Remove the pulley and key from the motor shaft.
C. DRIVE MOTOR INSTALLATION
1.
Place the drive motor in position and install the
four mounting bolts.
2.
Place the pulley and key on the motor shaft.
NOTE
Do not tighten the pulley screws until after the belt
tension has been properly adjusted.
3.
Install the belt and tighten the tension adjustment
bolt.
4.
Use a Burroughs Belt Tension Gauge to set the
tension for the drive belt. Set the belt tension to
40-45 lbs.
5.
Using a straightedge, align the drive motor pulley
with the gearbox pulley. Tighten the two allen
head screws.
6.
Install wiring according to wiring diagram (located
behind the left side panel). Install electrical cover
plate on the motor.
7.
Install back and side panels.
6.3 DRIVE
MOTOR
The F231 has two drive motors. They are used to rotate
the auger assemblies. An internal, normally closed, cen-
trifugal switch starts the drive motor. The motors have an
internal thermal overload.
A. DRIVE MOTOR TEST
1.
Turn the machine off by pressing the Main Power
Off/On button and disconnect the machine from
the electrical supply.
2.
Remove the back panel and a side panel.
3.
Loosen the belt tension adjustment nut and remove
the belt.
4.
Connect power to the machine.
5.
Turn the machine on by pressing the Main Power
Off/On button.
6.
Press the right arrow, SET, then the SEL button
to access the technician level on the control.
7.
Activate the drive motor through the Left Output
Control or Right Output Control menus which are
located under Utilities in the Testing and Manual
Operation screen. Refer to Section 4 for details.
8.
Go to the Test Monitoring screen under Utilities.
The motor current should not be above 3.5 on
single phase machines or 3.8 on three phase
machines.
NOTE
The motor amps are based on 230VAC supply
voltage.
9.
After the test, stop the motor by exiting the Testing
and Manual Operation section. Turn the machine
off and disconnect from the electrical supply.
10.
Install the belt and tighten the tension bolt.
11.
Use a Burroughs Belt Tension Gauge to set the
tension for the drive belt. Set the belt tension to
40-45 lbs.
12.
Using a straightedge, align the drive motor pulley
with the gearbox pulley. Tighten the two allen
head screws.
WARNING
Hazardous voltage
Make sure the machine is off when disassembling
for servicing. The machine must be disconnected
from electrical supply before removing any access
panel. Failure to disconnect power before servicing
could result in death or serious injury.
Figure 6-3 Belt Tension Adjustment
Tension
Adjustment
Nut
Summary of Contents for Stoelting F231
Page 1: ...Model F231 SERVICE MANUAL Manual No 513659 Rev 2...
Page 2: ......
Page 16: ...Service Manual 513659 8 Model F231...
Page 34: ...Service Manual 513659 26 Model F231...
Page 50: ...Service Manual 513659 42 Model F231...
Page 61: ...Service Manual 513659 53 Model F231 8 8 WIRING DIAGRAMS...