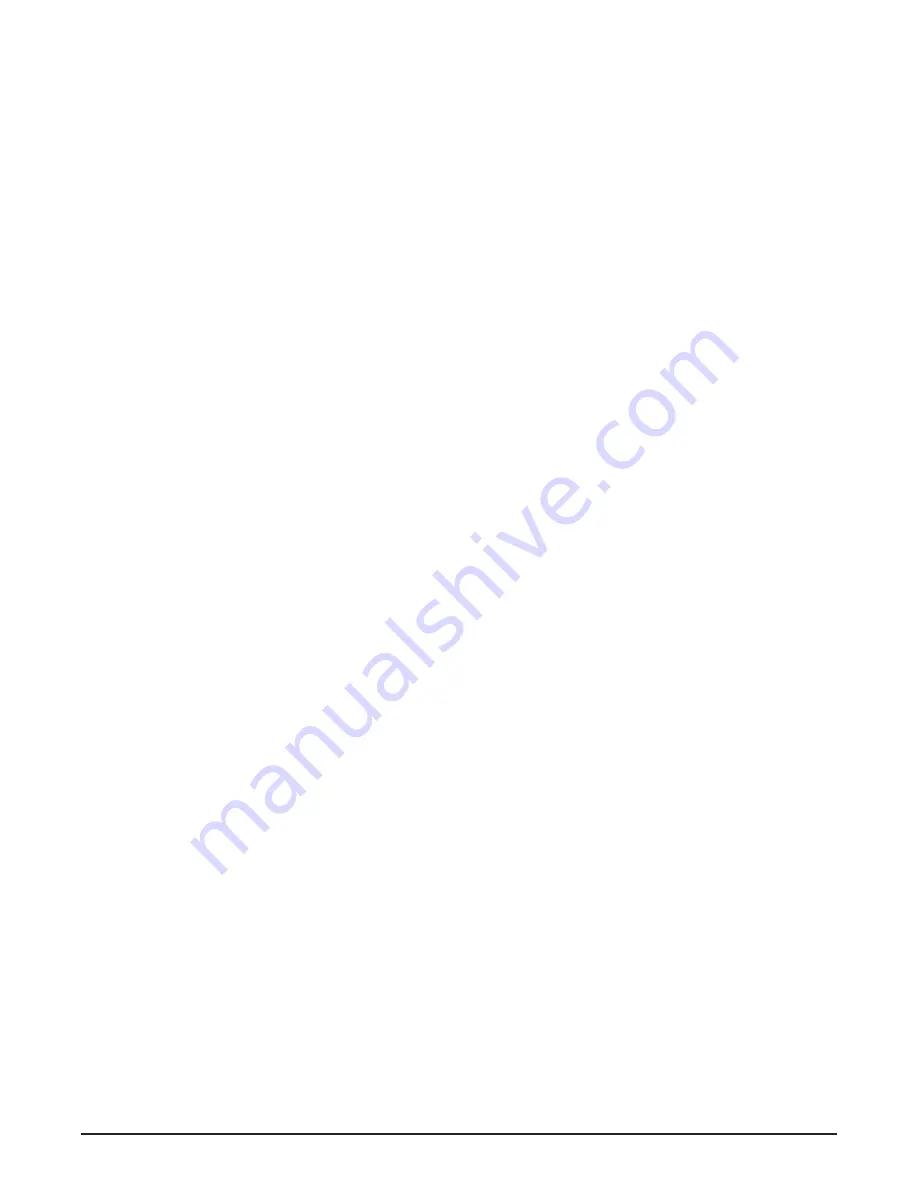
Owner’s Manual #513851
8
CBB Model Machines
E.
Product will be ready to serve in 40-60 minutes.
The time it takes to be ready is dependent upon
many variables including the mix temperature
when poured into the tank, the amount of sugars
and butterfat in the mix and the temperature setting
on the machine.
F.
When the display reads “READY TO SERVE” the
product is ready, pull the spigot handle open to
serve.
3.6 REMOVING MIX FROM MACHINE
To remove the mix from the machine, refer to the follow-
ing steps:
A.
Press the Cold Selection button until the display
shows Motor On.
B.
Drain the mix by repeatedly opening and closing
the spigot. A container should be placed under
the spigot to collect the liquid mix.
D.
When the mix is drained, fi ll the tank with 1 gallon
of cool tap water. After 30 seconds open the spigot
to drain the water out of the machine.
C.
Use Stera-Sheen or equivalent sanitizing solution
according to manufacturer’s instructions to
provide a 100 parts per million strength solution.
Any sanitizer must be used only in accordance
with the manufacturer’s instructions.
D.
Pour the sanitizer into the tank.
E.
After 5 minutes, drain the sanitizer out of the
freezing cylinder.
F.
Press the Auger Movement button to stop the
auger. Press the Main Power Switch to turn the
machine off.
3.7 DISASSEMBLY OF MACHINE PARTS
Inspection for worn or broken parts should be made each
time the machine is disassembled. All worn or broken
parts should be replaced to ensure safety to both the
operator and the customer and to maintain good machine
performance and a quality product.
NOTE
The frequency of cleaning the machine and ma-
chine parts must comply with local health regula-
tions.
After the mix has been removed from the machine, follow
the steps below to disassemble the parts.
A.
Remove the spigot by pulling the pivot arms
slightly outwards to disengage them from the
handle knobs.
NOTE
Pull both arms at the same time to prevent them
from twisting and breaking.
B.
Remove the spigot handle by tilting it back and
pulling upwards.
C.
Remove the rosette cap.
D.
Remove the tank fastening knobs from the tank
clamps. Unclamp and remove the tank from the
machine. Remove the gasket from the bottom of
the tank. Remove the auger support and gasket
from the tank.
E.
Pull the horizontal auger towards the front of the
machine to remove it. Remove the gear from the
back of the auger.
F.
Unscrew the fastening nut from the top of the
vertical auger and remove the auger. Remove
the gear from the bottom of the auger.
G.
Remove the o-ring from the spigot assembly.
Remove the o-ring by squeezing the it upward
with a dry cloth. When a loop is formed, roll the
o-ring out of the groove.
H.
Remove condensate tray, drip tray and drip tray
grid.
3.8 CLEANING AND SANITIZING THE
MACHINE PARTS
Place all loose parts in a pan or container and take to
the wash sink for cleaning. Local and state health codes
dictate the procedure required. Some health codes require
a four-sink process (pre-wash, wash, rinse, sanitize, and
air-dry), while other codes require a three-sink process
(without the pre-wash step). The following procedures
are a general guideline only. Consult your local and state
health codes for procedures required in your location.
A.
Prepare Stera-Sheen or equivalent cleaner in
2 gallons of 90° to 110°F (32° to 43°C) water
following manufacturers instructions.
B.
Prepare sanitizing solution according to
manufacturer’s instructions to provide a 100 ppm
strength solution. Mix the sanitizer in quantities
of no less than 2 gallons of 90° to 110°F (32° to
43°C) water. Check the strength of the sanitizing
solution. Use a chlorine test strip and color chart
to make sure the solution has 100 ppm.
C.
Place all parts in the cleaning solution and clean
the parts with brushes and sponges. Rinse all
parts with clean 90° to 110°F (32° to 43°C) water.
Place the parts in the sanitizing solution.
D.
Remove the parts from the sanitizing solution and
allow them to air dry.
Summary of Contents for Stoelting CBB Series
Page 1: ...Model CBB OPERATORS MANUAL Manual No 513851 Rev 0 ...
Page 2: ......
Page 6: ......