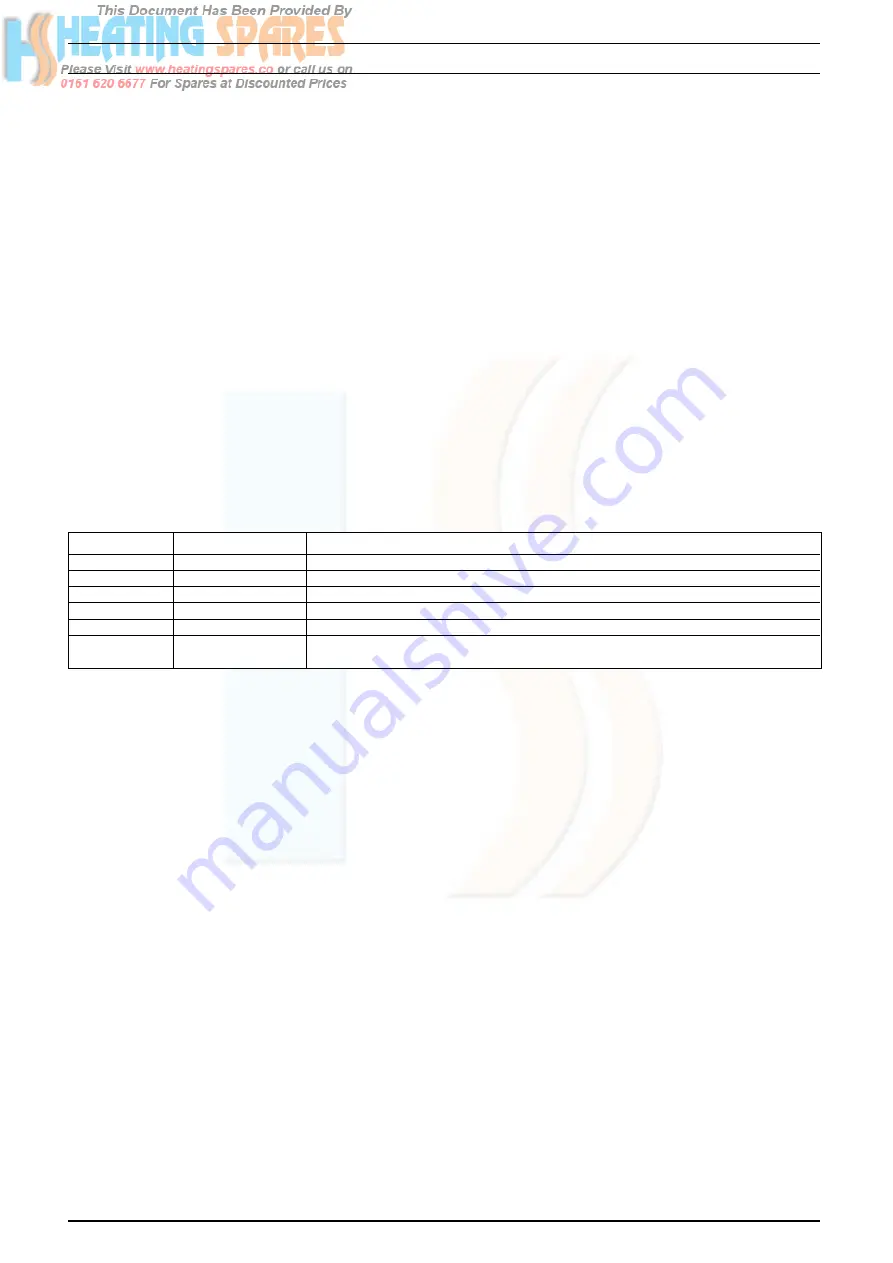
Supplied By www.heating spares.co Tel. 0161 620 6677
6
UNICA BHE
SECTION 3
GENERAL REQUIREMENTS (UK)
This appliance must be installed by a competent
person in accordance with the Gas Safety (In-
stallation & Use) Regulations.
3.1
RELATED DOCUMENTS
The installation of this boiler must be in accord-
ance with the relevant requirements of the Gas
Safety (Installation & Use) Regulations, the local
building regulations, the current I.E.E. wiring regu-
lations, the bylaws of the local water undertaking,
the Building Standards (Scotland) Regulation and
Building Standards (Northern Ireland) Regulations.
It should be in accordance also with any relevant
requirements of the local authority and the rel-
evant recommendations of the following British
Standard Codes of Practice.
3.2
LOCATION OF APPLIANCE
The appliance may be installed in any room or
internal space, although particular attention is
drawn to the requirements of the current I.E.E.
wiring regulations, and in Scotland, the electrical
provisions of the Building Regulations, with respect
to the installation of the appliance in a room or
internal space containing a bath or shower.
When an appliance is installed in a room or internal
space containing a bath or shower, the appliance
or any control pertaining to it must not be within
reach of a person using the bath or shower.
The location chosen for the appliance must permit
the provision of a safe and satisfactory flue and
termination. The location must also permit an
adequate air supply for combustion purposes and
an adequate space for servicing and air circulation
around the appliance. Where the installation of the
appliance will be in an unusual location special
procedures may be necessary, BS 6798 gives
detailed guidance on this aspect.
A compartment used to enclose the appliance
must be designed and constructed specifically for
this purpose. An existing compartment/cupboard
may be utilised provided that it is modified to suit.
Details of essential features of compartment/
cupboard design including airing cupboard
installations are given in BS 6798.
3A.2
LOCATION OF APPLIANCE
The appliance may be installed in any room or
internal space, although particular attention is
drawn to the requirements of the current ETCI
National Rules for Electrical Installations, and I.S.
813, Annex K.
When an appliance is installed in a room or internal
space containing a bath or shower, the appliance
or any control pertaining to it must not be within
reach of a person using the bath or shower.
The location chosen for the appliance must permit
the provision of a safe and satisfactory flue and
termination. The location must also permit an
BS 5440
PART 1
FLUES
BS 5440
PART 2
FLUES & VENTILATION
BS 5449
PART 1
FORCED CIRCULATION HOT WATER SYSTEMS
BS 5546
INSTALLATION OF GAS HOT WATER SUPPLIES FOR DOMESTIC PURPOSES
BS 6798
INSTALLATION OF BOILERS OF RATED INPUT NOT EXCEEDING 60kW
BS 6891
LOW PRESSURE INSTALLATION PIPES
BS 7074
PART 1
APPLICATION, SELECTION, AND INSTALLTION OF EXPANSION VESSELS
AND ANCILLARY EQUIPMENT FOR SEALED WATER SYSTEMS
adequate air supply for combustion purposes and
an adequate space for servicing and air circulation
around the appliance. Where the installation of the
appliance will be in an unusual location special
procedures may be necessary, refer to I.S. 813 for
detailed guidance on this aspect.
A compartment used to enclose the appliance
must be designed and constructed specifically for
this purpose. An existing compartment/cupboard
may be utilised provided that it is modified to suit.
3.3
GAS SUPPLY
The gas meter – as supplied by the gas supplier –
must be checked to ensure that it is of adequate
size to deal with the maximum rated input of all the
appliances that it serves. Installation pipes must
be fitted in accordance with BS 6891.
Pipe work from the meter to the appliance must
be of adequate size. Pipes of a smaller size than
the appliance gas inlet connection must not be
used. The installation must be tested for tightness
in accordance with BS6891.
If the gas supply serves more than one appliance,
it must be ensured that an adequate supply is
maintained to each appliance when they are in
use at the same time.
3.4
FLUE SYSTEM
The terminal should be located where the disper-
sal of combustion products is not impeded and
with due regard for the damage and discoloration
that may occur to building products located nearby.
The terminal must not be located in a place where
it is likely to cause a nuisance (see fig. 4).
In cold and/or humid weather, water vapour will
condense on leaving the terminal; the effect of
such pluming must be considered.
If installed less than 2m above a pavement or
platform to which people have access (including
balconies or flat roofs) the terminal must be
protected by a guard of durable material.
The guard must be fitted centrally over the termi-
nal. Refer to BS 5440 Part 1, when the terminal is
0.5 metres (or less) below plastic guttering or 1
metre (or less) below painted eaves.
3.5
AIR SUPPLY
The following notes are intended for general guid-
ance only. This appliance is a room-sealed, fan-
flued boiler, consequently it does not require a
permanent air vent for combustion air supply.
When installed in a cupboard or compartment,
ventilation for cooling purposes is also not required.
3.6
WATER CIRCULATION
Detailed recommendations are given in BS 5449
Part 1 and BS 6798. The following notes are for
general guidance only.
3.6.1
PIPEWORK
It is recommended that copper tubing to BS 2871