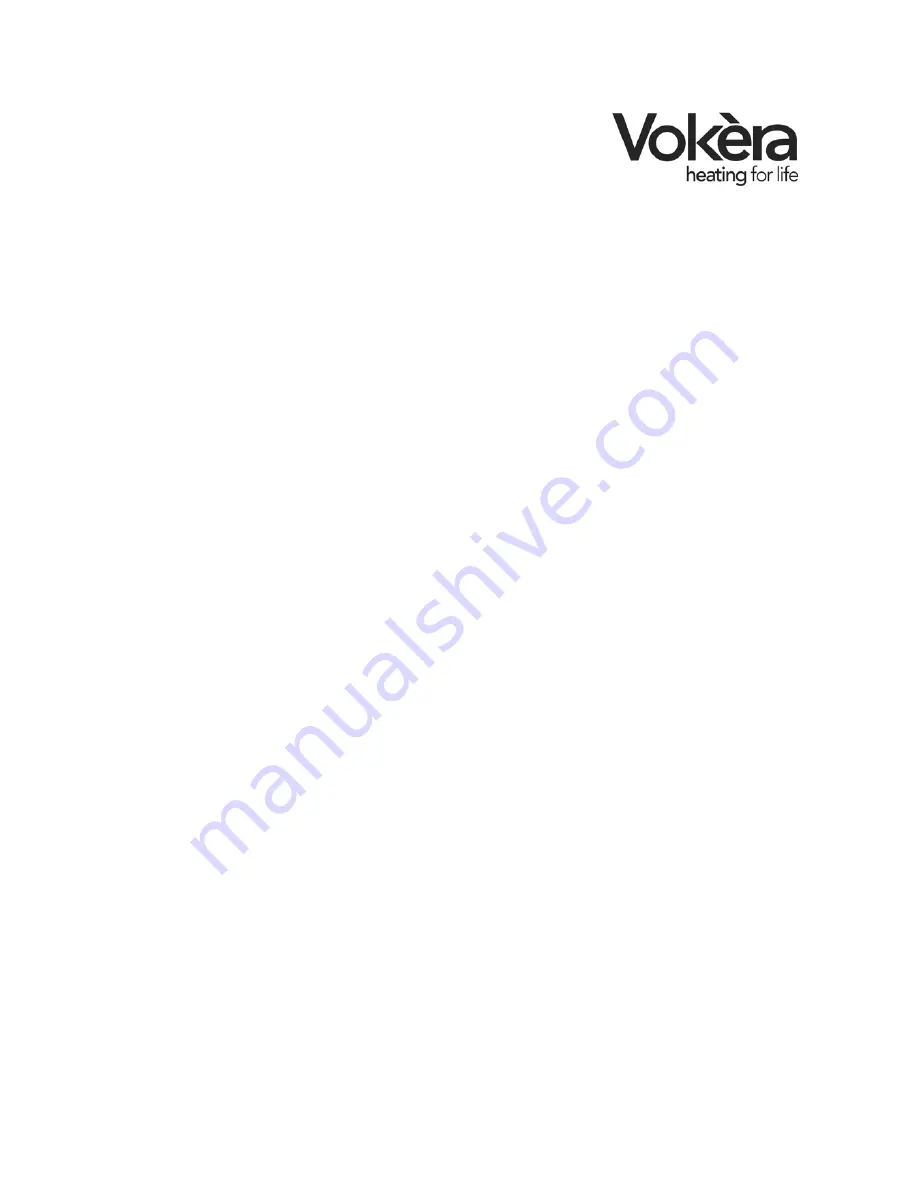
Cod. 20030102 - 02/11 - Ed. 0
Registered address:
Vokèra Ltd
Borderlake House
Unit 7 Riverside Industrial Estate
London Colney
Herts AL2 1HG
www.vokera.co.uk
www.vokera.ie
Sales, General Enquires
T
0844 391 0999
F
0844 391 0998
Vokèra Ireland
West Court, Callan
Co Kilkenny
T
056 7755057
F
056 7755060
Vokèra Limited reserve the right to change
specification without prior notice
Consumers statutory rights are not affected.
A Riello Group Company.
Company Reg No: 1047779