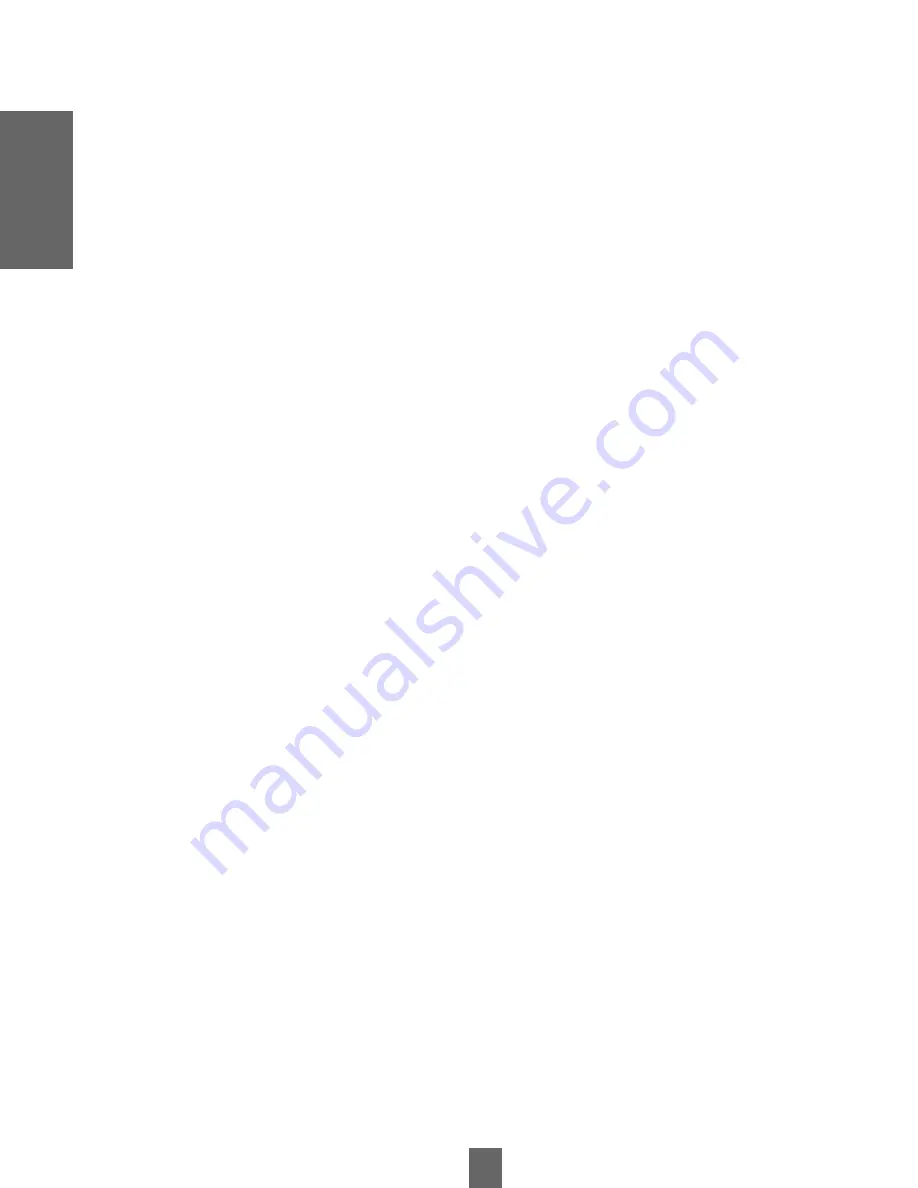
5
Inspection and
Storage
2.3
Medium-term storage (less than 2 months)
Perform the following:
1. Indoor storage is recommended.
2. The pump should be stored in an upright position. Although the pump can be shipped on its side.
3. The pump should be stored in a clean, dry place and should be protected from dirt and foreign matter. The storage
area should also be free from vibration.
4. If the pump is to be stored outdoors, it should be protected with a waterproof cover. However, the cover should not
seal the pump because air circulation is necessary to prevent condensation.
5. Rotate the shaft several 10 turns every week and inspect the general condition of the pump and equipment.
6. Before putting the equipment into operation, the watertight seal of the power cable should be checked.
7. Before putting into operation, the insulation should be measured if the equipment was exposed to wet storage
conditions.
2.4
Long Term Storage (greater than 2 months)
For safe storage and maintenance of new and standby pumps:
•
Do not stack other pieces of equipment on top of the pumps.
•
Repair any paint damage before storage caused by shipping damage.
•
Flush pumps with clean water when removing a pump from service for storage. Remove any solids
accumulated on any of the seals.
•
Dry any water present inside.
•
Rotate the shaft 10 turns every week and inspect the general condition of the pump and equipment. Maintain
written records of shaft rotation intervals when the storage period exceeds six months from the time of
shipment. Records should be available for inspection by VOGT personnel.
•
Do not store bearing carriers near areas that exhibit vibration or in dampness.
•
Drain and completely refill the oil chamber every six months with new recommended lubricant.
Inspection and
Storage
Summary of Contents for SSD Series
Page 1: ......