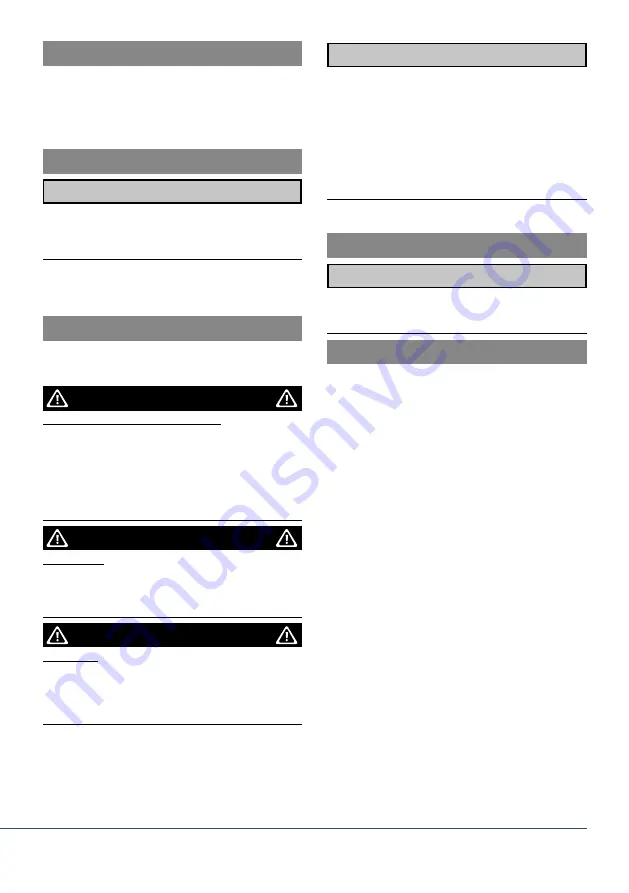
15
5. OPERATION
6. PUTTING OUT OF OPERATION
7. MAINTENANCE AND CLEANING
8. DISPOSAL
9. WARRANTY
ʸ
Consult the documentation for the welding components.
ʸ
As liquid-cooled cable assemblies start to leak when they
overheat, the coolant recirculator should continue running
for approx. 5 min. after welding.
ʸ
The specified maintenance intervals are guidance values
and refer to single-shift operation.
ʸ
Only qualified personnel are permitted to perform work on
the device or system.
ʸ
Check the coolant hoses, seals and connectors for damage
or leaks and replace if necessary.
ʸ
Check and clean the power contact surfaces on the torch
neck and torch neck seat.
ʸ
Check and wear your personal protective equipment.
ʸ
Remove any adhering weld spatter.
ʸ
Ensure that all threaded fittings are tight.
ʸ
Do not dispose of the device with household waste.
ʸ
For disposal, observe the local regulations, laws, provisions,
standards and guidelines.
7.1 Replacing the torch neck
-> 4.1. SETTING UP THE TORCH on page 13
Scheduled maintenance and cleaning are prerequisites for a
long service life and trouble-free operation.
1. Open the shielding gas cylinder.
2. Switch on the power source.
3. Switch on the coolant recirculator for MT W.
4. Rinse the shielding gas lines.
5. Start the welding process by pressing and holding the
torch trigger.
1. Wait until the shielding gas post-flow time has passed.
2. Close the shut-off-valve for the gas supply.
3. Switch off the power source.
4. Switch off the coolant recirculator.
NOTICE
NOTICE
NOTICE
Risk of injury due to unexpected start-up
The following instructions must be adhered to throughout all
maintenance, servicing, assembly, disassembly and repair work:
ʸ
Switch off the power source.
ʸ
Close off the gas supply.
ʸ
Close off the coolant supply.
ʸ
Disconnect the coolant supply and return hoses.
ʸ
Close off the compressed air supply.
ʸ
Disconnect all electrical connections.
Electric shock
Dangerous voltage due to defective cables.
ʸ
Check all live cables and connections for proper installation
and damage.
ʸ
Replace any damaged, deformed or worn parts.
Risk of burns
Risk of burns from hot coolant and hot surfaces.
ʸ
Switch off the coolant recirculator before starting mainte-
nance, servicing, assembly, disassembly or repair work.
ʸ
Allow the welding torches to cool down.
ʸ
Wear the correct protective gloves.
DANGER
DANGER
DANGER
This product is a Böhler Welding product. voestalpine Böhler
Welding GmbH guarantees that the product has been manu-
afactured without defects and offers factory manufacturing
and functional warranty for this procduct upon delivery in line
with current state-of-the-art technology and the current regu-
lations. To the extent that Böhler Welding is responsible for a
deficiency in the product, Böhler Welding shall be obliged to
choose, at its own discretion, to either repair the defect or
deliver a replacement at its own expense. The warranty covers
manufacturing faults, but not damage resulting from natural
wear and tear, overloading or improper use. The warranty
period is defined in the General Terms and Conditions. Excep-
tions in the case of specific products are regulated separately.
Warranty will also be rendered invalid if spare parts and wearing
parts are used that are not Böhler Welding parts and if the
product has been repaired improperly by the user or a third
party. Wearing parts are excluded in general from the warran-
ty. In addition, Böhler Welding is not liable for damage caused
by using our products. Questions about warranty and service
can be addressed to the manufacturer or our distributors. For
more information, www.voestalpine.com/welding
English
- English -