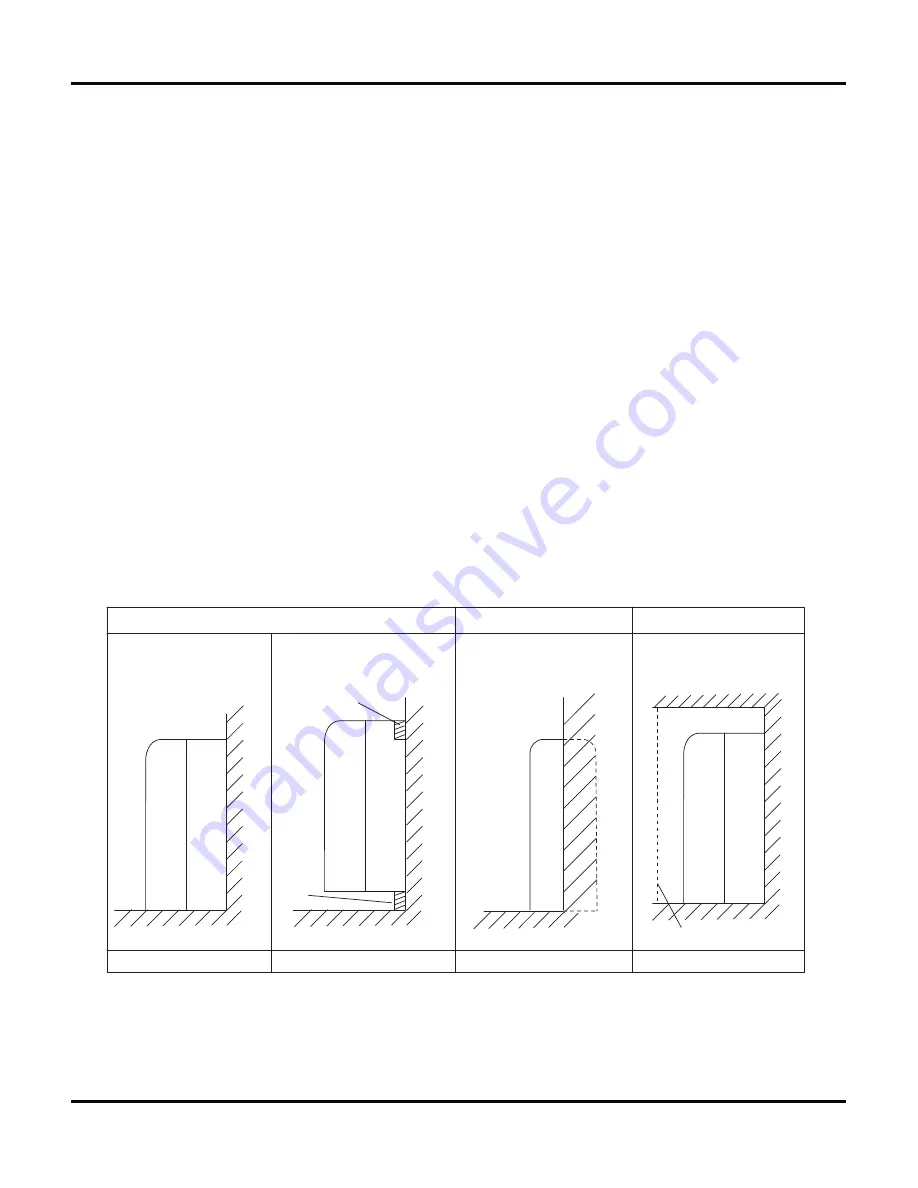
24
Installation Manual
7. Installation Manual
7.1 Choosing an Installation Site
Before choosing the installation site,obtain user approval.
Indoor unit
The indoor unit should be sited in a place where:
1) the restrictions on installation specified in the indoor unit installation drawings are met.
2) both air intake and exhaust have clear paths met.
3) the unit is not in the path of direct sunlight.
4) the unit is away from the source of heat or steam.
5) there is no source of machine oil vapour (this may shorten indoor unit life).
6) cool(warm) air is circulated throughout the room.
7) the unit is away from electronic ignition type fluorwscent lamps (inverter or rapid stert type) as they may shorten
the remote controller range.
8) the unit is at least 1 metre away from any television or radio set(unit may cause interference with the picture or
sound).
7.2 Indoor Unit Installation Drawings
The indoor unit may be mounted in any of the three styles shown here.
Exposed
Floor lnstallation
Wall Installation
Molding
Mounting plate
Half conceated
Concealed
Grid(field supply)
Summary of Contents for ACP-12CT35GECI
Page 1: ...ACP 12CT35GECI ACP 18CT50GECI Service manual ENG RoHS NNO 1 09 ...
Page 2: ......
Page 14: ...10 Constrction views 3 Construction Views 3 1 Indoor Unit Unit mm 700 215 600 398 205 22 ...
Page 56: ...52 Removal Procedure Steps Procedure 13 Remove motor Remove the motor motor ...
Page 66: ......
Page 67: ......
Page 68: ......