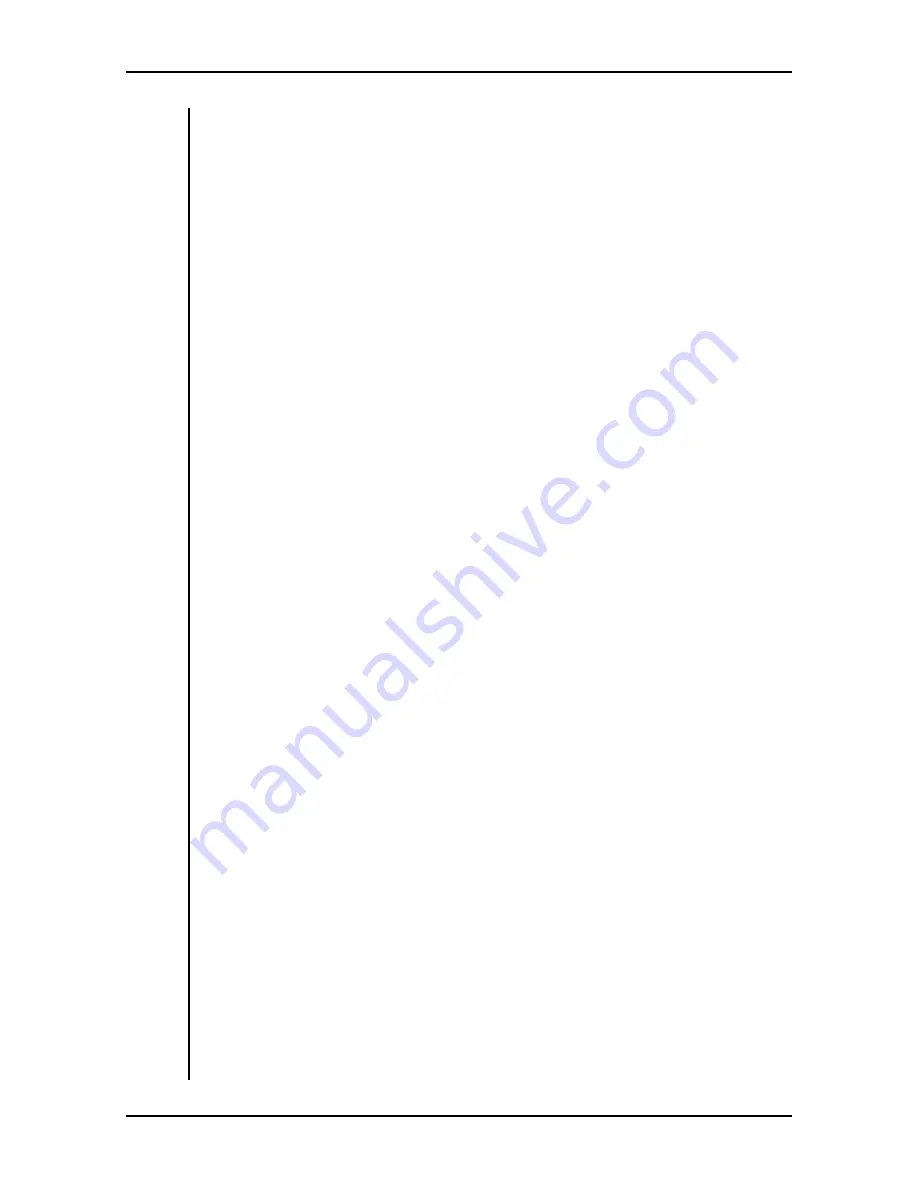
HS-105P
Maintenance And Repair
4-10
User Manual
that set the speed and accuracy characteristics of the lens servo. Several carriers
have been optimized by Vinten Inc. for popular lens types, and it is important
that you have the correct one installed for your lens. Four of the resistors (and a
0 ohm link) are in the focus servo and four (and a 0 ohm link) in the zoom servo.
Typically, the two servos have the same resistor values.
Two resistors in each servo (R84-1, R84-2, R84-7, R84-9) set the maximum cur-
rent to the lens motors to provide adequate power for fast response, without sup-
plying excess current that could shorten motor life. Vinten Inc. selects these
resistor values to match the lens motor specifications.
The third resistor in each servo (R84-5, R84-8) sets the tachometer gain. The
value affects the traverse speed of the servo, but is primarily used to prevent
overshoot. The value is chosen by providing a step voltage demand input to the
servo. When properly selected, the servo should move responsively, without
overshooting the end position. This will prevent the lens from slamming into the
end stops and causing excessive wear or damage.
The fourth resistor in each servo (R84-4, R84-6) sets the loop gain or stiffness.
A stiffer servo has more gain and produces greater repeatability. However, if the
gain is too high, the servo will start to buzz or oscillate or overshoot. You want
to set the gain as high as possible, but short of the point of oscillation. A conser-
vative procedure would be to take it up to the point of buzzing, and then drop
back to a resistor of half that value.
Head Indexing Procedure
At power up, the HS-105 has to reset the pan and tilt axes to known mechanical
positions. This is achieved by finding the edge of the pan shutter (coarse posi-
tioning) and then finding the pan index pulse (fine positioning). The same proce-
dure is then used for the tilt axis. After the indexing is finished, the head moves
to the position requested by the controller. If a controller is not connected, there
should be no movement after the indexing is complete.
As shown below, the pan shutter is a 180° metal vane which breaks the light
beam of an optosensor. The index position is at one end of the shutter - where
the optosensor transitions from open to blocked. The index pulse is a marker
within the incremental opto-encoder which is part of the motor assembly. The
tilt axis is identical. The sequence of events is:
1.
At power up, the head pans slowly in search of the pan shutter edge. When
the edge is found, the head pans (clockwise as viewed from above) more
slowly for a few degrees to find the index pulse from the motor encoder.
During the search for the index pulse, the LED DS1 will be on. The LED
goes out when the index pulse is found. The pan position is now reset.
2.
The tilt axis moves slowly in search of the tilt shutter edge. During this
search, the pan axis mimics the tilt movement. When the tilt shutter edge is
found, the head tilts (clockwise as viewed from the PCB side) more slowly
for a few degrees to find the index pulse from the tilt motor encoder. Tilt is
now reset.
Summary of Contents for HS-105P
Page 10: ...Table Of Contents x This page left blank intentionally ...
Page 11: ...User Manual 1 1 1 Safety Introduction ...
Page 21: ...User Manual 2 1 2 Operation ...
Page 23: ...User Manual 3 1 3 Installation ...
Page 25: ...HS 105P Installation User Manual 3 3 This page left blank intentionally ...
Page 31: ...HS 105P Installation User Manual 3 9 This page left blank intentionally ...
Page 33: ...HS 105P Installation User Manual 3 11 This page left blank intentionally ...
Page 50: ...HS 105P Installation 3 28 User Manual This page left blank intentionally ...
Page 51: ...User Manual 4 1 4 Maintenance And Repair ...
Page 57: ...HS 105P Maintenance And Repair User Manual 4 7 ...
Page 58: ...HS 105P Maintenance And Repair 4 8 User Manual ...
Page 65: ...HS 105P Maintenance And Repair User Manual 4 15 ...
Page 66: ...HS 105P Maintenance And Repair 4 16 User Manual ...
Page 67: ...HS 105P Maintenance And Repair User Manual 4 17 ...
Page 68: ...HS 105P Maintenance And Repair 4 18 User Manual ...
Page 69: ...HS 105P Maintenance And Repair User Manual 4 19 ...
Page 70: ...HS 105P Maintenance And Repair 4 20 User Manual This page left blank intentionally ...