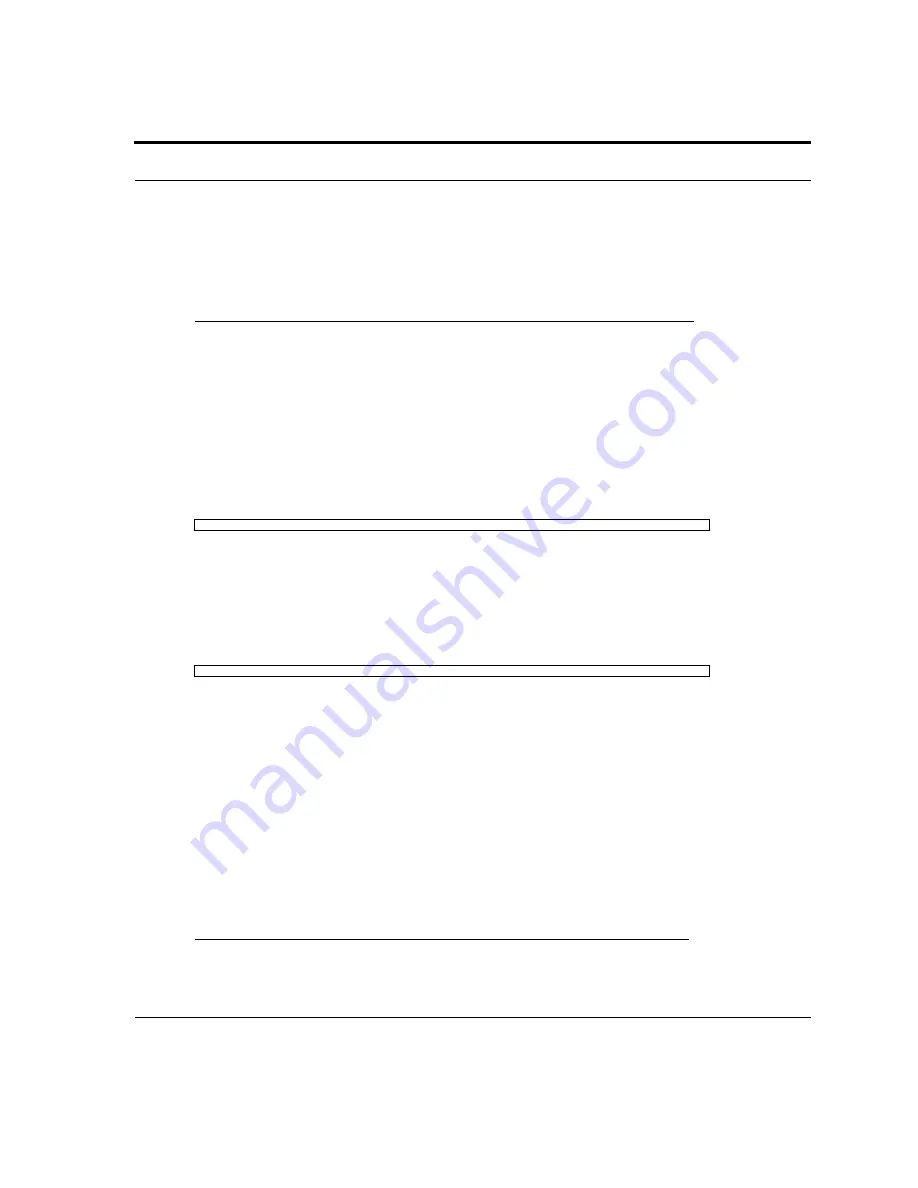
Oxeo PR LCP | 10-2022 | en
217
Argon IG-01
Safety Data Sheet
according to Federal Register / Vol. 77, No. 58 / Monday, March 26, 2012 / Rules and Regulations
05/17/2022
Argon IG-01
First-aid measures after skin contact
: IF ON SKIN (or clothing): Remove affected clothing and wash all exposed skin with water for at
least 15 minutes. If irritation develops or persists, get medical attention. Thaw frosted parts
with lukewarm water. Do not rub affected area. Get immediate medical advice/attention.
First-aid measures after eye contact
: IF IN EYES: Immediately flush with plenty of water for at least 15 minutes. Remove contact
lenses if present and easy to do so. Continue rinsing if pain, blinking, or irritation develops or
persists, get medical attention. Continue rinsing. Thaw frosted parts with lukewarm water. Do
not rub affected area. Get immediate medical advice/attention.
First-aid measures after ingestion
: IF SWALLOWED: rinse mouth thoroughly. Do not induce vomiting without advice from poison
control center. Get medical attention if you feel unwell.
4.2.
Most important symptoms and effects (acute and delayed)
Symptoms/effects
: May displace oxygen and cause rapid suffocation. Unconsciousness.
Symptoms/effects after inhalation
: May displace oxygen and cause rapid suffocation. Unconsciousness.
Symptoms/effects after skin contact
: May cause skin irritation. Contact with the product may cause cold burns or frostbite.
Symptoms/effects after eye contact
: Direct contact with eyes is likely to be irritating. Contact with the liquid may cause frostbite and
serious damage to eyes.
Symptoms/effects after ingestion
: May cause gastrointestinal irritation.
4.3.
Immediate medical attention and special treatment, if necessary
No additional information available
SECTION 5: Fire-fighting measures
5.1.
Suitable (and unsuitable) extinguishing media
Suitable extinguishing media
: Use extinguishing media appropriate for surrounding fire.
5.2.
Specific hazards arising from the chemical
Fire hazard
: Non-flammable gas.
Explosion hazard
: Contains gas under pressure; may explode if heated.
Reactivity
: No dangerous reactions known under normal conditions of use. In a fire or if heated, a pressure
increase will occur and the container may burst.
5.3.
Special protective equipment and precautions for fire-fighters
Firefighting instructions
: Exercise caution when fighting any chemical fire. Do not dispose of fire-fighting water in the
environment. Prevent human exposure to fire, fumes, smoke and products of combustion.
Protection during firefighting
: Do not enter fire area without proper protective equipment, including respiratory protection.
SECTION 6: Accidental release measures
6.1.
Personal precautions, protective equipment and emergency procedures
General measures
: Evacuate area. Keep upwind. Ventilate area. Spill should be handled by trained cleaning
personnel properly equipped with respiratory and eye protection.
6.1.1. For
non-emergency
personnel
Protective equipment
: Wear Protective equipment as described in Section 8.
Emergency procedures
: Evacuate unnecessary personnel.
6.1.2. For
emergency
responders
Protective equipment
: Wear suitable protective clothing, gloves and eye or face protection. For further information
refer to section 8: "Exposure controls/personal protection".
6.2. Environmental
precautions
Prevent entry to sewers and public waters. Notify authorities if liquid enters sewers or public waters. Avoid release to the environment.
6.3.
Methods and material for containment and cleaning up
For containment
: Stop leak if safe to do so.
Methods for cleaning up
: Exclude sources of ignition and ventilate the area. Ground equipment electrically. Use
explosion-proof equipment.
6.4. Reference
to other sections
See Sections 8 and 13.
Summary of Contents for Oxeo
Page 1: ...Installation and Maintenance Manual Oxeo Inert Gas Extinguishing System...
Page 10: ...Inst and Maint Manual Oxeo PR LCP F_101921 Rev 02 10 2022 en 4...
Page 32: ...Inst and Maint Manual Oxeo PR LCP F_101921 Rev 02 10 2022 en 26...
Page 42: ...Inst and Maint Manual Oxeo PR LCP F_101921 Rev 02 10 2022 en 36...
Page 134: ...Inst and Maint Manual Oxeo PR LCP F_101921 Rev 02 10 2022 en 128...
Page 148: ...Inst and Maint Manual Oxeo PR LCP F_101921 Rev 02 10 2022 en 142...
Page 156: ...Inst and Maint Manual Oxeo PR LCP F_101921 Rev 02 10 2022 en 150...
Page 176: ...Inst and Maint Manual Oxeo PR LCP F_101921 Rev 02 10 2022 en 170...
Page 206: ...Inst and Maint Manual Oxeo PR LCP F_101921 Rev 02 10 2022 en 200...
Page 220: ...Inst and Maint Manual Oxeo PR LCP F_101921 Rev 02 10 2022 en 214...
Page 221: ...Oxeo PR LCP 10 2022 en 215 15 SafetyDataSheet IG 01 Argon...
Page 228: ...Oxeo PR LCP 10 2022 en 222...
Page 229: ...Oxeo PR LCP 10 2022 en 223 16 SafetyDataSheet IG 100 Nitrogen...
Page 236: ...Oxeo PR LCP 10 2022 en 230...
Page 237: ......