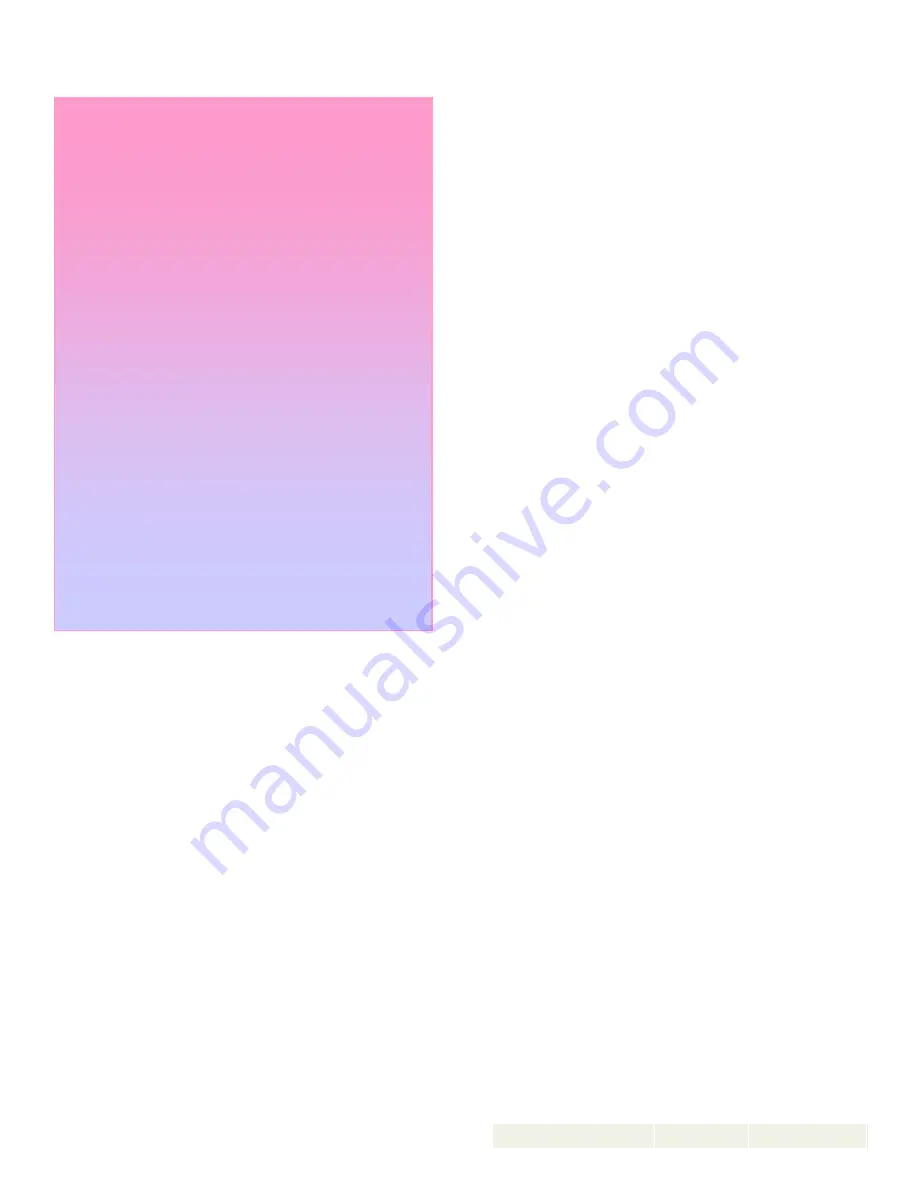
ROTATION:
Viking pumps operate equally well in a clockwise
or counterclockwise rotation. Shaft rotation determines which
port is suction and which is discharge. Port in area where
pumping elements (gear teeth) come out of mesh is suction
port.
PRESSURE RELIEF VALVES:
1.
Viking pumps are positive placement pumps and must be
provided with some sort of pressure protection. This may
be a relief valve mounted directly on the pump, an inline
pressure relief valve, a torque limiting device or a rupture
disk.
2.
There are relief valve options available on those pump
models designed to accept a relief valve. Options may
include a return to tank relief valve and a jacketed relief
valve. Pumps equipped with a jacketed head plate are
generally not available with a relief valve.
3.
If pump rotation is to be reversed during operation,
pressure protection must be provided on
both
sides of
pump.
4.
Relief valve adjusting screw cap must always point
towards suction side of pump. If pump rotation is
reversed, remove pressure relief valve and turn end for
end.
Refer to Figures 1 and 2.
5.
Pressure relief valves cannot be used to control pump
flow or regulate discharge pressure.
DANGER
BEFORE OPENING ANY VIKING PUMP
LIQUID CHAMBER (PUMPING CHAMBER,
RESERVOIR, RELIEF VALVE ADJUSTING
CAP FITTING, ETC.) BE SURE:
1.
THAT ANY PRESSURE IN CHAMBER
HAS BEEN COMPLETELY VENTED
THROUGH SUCTION OR DISCHARGE
LINES OR OTHER APPROPRIATE
OPENINGS OR CONNECTIONS.
2.
THAT THE DRIVING MEANS (MOTOR,
TURBINE, ENGINE, ETC.) HAS BEEN
"LOCKED OUT" OR MADE NON-
OPERATIONAL SO THAT IT CANNOT
BE STARTED WHILE WORK IS BEING
DONE ON PUMP.
3.
THAT YOU KNOW WHAT LIQUID THE
PUMP HAS BEEN HANDLING AND
THE PRECAUTIONS NECESSARY TO
SAFELY HANDLE THE LIQUID.
OBTAIN A MATERIAL SAFETY DATA
SHEET (MSDS)
FOR THE LIQUID TO
BE SURE THESE PRECAUTIONS ARE
UNDERSTOOD
FAILURE TO FOLLOW THE ABOVE
LISTED PRECAUTIONARY MEASURES
MAY RESULT IN SERIOUS INJURY OR
DEATH.
For additional information on pressure relief valves, refer to
Technical Service Manual TSM000 and Engineering Service
Bulletin ESB-31.
SPECIAL MECHANICAL SEALS:
Extra care should be taken
in repair of pumps with mechanical seals. Read and follow all
special information supplied with pump.
MAINTENANCE
Series 123 and 4123 pumps are designed for long, trouble-
free service life under a wide variety of application conditions
with a minimum of maintenance. The points listed below will
help provide long service life.
LUBRICATION:
External lubrication must be applied slowly
with a handgun to all lubrication fittings every 500 hours of
operation with multi-purpose grease, NLGI # 2. Do not over-
grease. Applications involving very high or low temperatures
will require other types of lubrication.
Refer to Engineering
Service Bulleting ESB-515
. Consult factory with specific
lubrication questions.
PACKING ADJUSTMENT
:
New packed pumps require initial
packing adjustment to control leakage as packing “runs in”.
Make initial adjustments carefully and do not over-tighten
packing gland. After initial adjustment, inspection will reveal
need for packing gland adjustment or packing replacement.
Refer to instructions under DISASSEMBLY, page 4,
and
Assembly, page 5, regarding repacking pump.
CLEANING PUMP:
Keep pump as clean as possible. This
will facilitate inspection; adjustment and repair work and help
prevent overlooking a dirt covered grease fitting.
STORAGE:
If pump is to be stored, or not used for six months
or more, pump must be drained and a light coat of non-
detergent SAE 30 weight oil must be applied to all internal
pump parts. Lubricate fittings and apply grease to pump shaft
extension. Viking suggests rotating pump shaft by hand one
complete revolution every 30 days to circulate the oil.
SUGGESTED REPAIR TOOLS:
The following tools must be
available to properly repair Series 123 and 4123 pumps.
These tools are in addition to standard mechanics’ tools such
as open end wrenches, pliers, screwdrivers etc. Most of the
items can be obtained from an industrial supply house.
1.
Soft Headed Hammer
2.
Allen Wrenches (some mechanical seals and set
collars)
3.
Packing hooks, flexible (packed pumps)
Large for 0.375 inch and up cross section packing
4.
Mechanical seal installation sleeve
2-751-005-630 for 2.4375 inch Q-M4123
5.
Bearing locknut spanner wrench
(Source: #471 J.H. Williams & Co. or equal)
6.
Spanner wrench, adjustable pin type for use on double
end caps (Source #482 J.H. Williams & Co or equal)
7.
Brass Bar
8.
Arbor Press
SPECIAL INFORMATION
SECTION TSM 151.2
ISSUE B
PAGE 2 OF 14