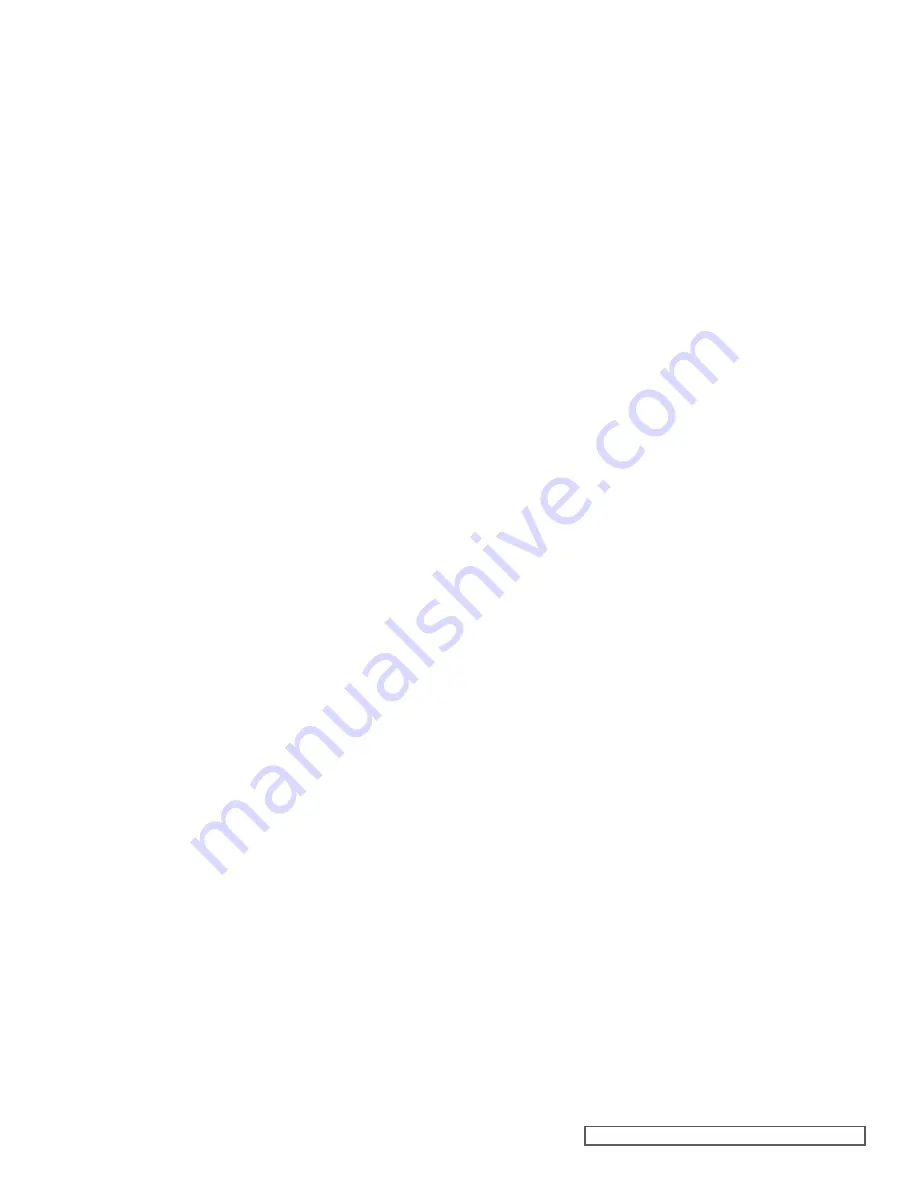
SECTION TSM
685.2
ISSUE
C
PAGE 15 OF 16
TROUBLESHOOTING
Some of the following may help pinpoint the problem:
Pump does not pump:
•
Pump has lost its prime from air leak or low level in
tank.
•
Suction lift is too high.
•
Pump is rotating in the wrong direction.
•
The strainer may be clogged.
•
The bypass valve is open, the pressure relief valve is
set too low or the pressure relief valve poppet is stuck
open.
•
Improper end clearance.
•
The pump is worn out.
•
Are there any changes in liquid, system or operation that
would influence pump or coupling performance, e.g. new
liquid, additional lines or process changes?
•
Temperature changes either in the liquid or the
environment.
•
The magnetic coupling is decoupling. Changes in
application (temperature, pressure, viscosity, etc.) may
require torque beyond coupling capabilities.
Pump starts, then loses its prime
:
•
The supply tank is empty.
•
Liquid is vaporizing in the suction line.
•
An air leak or air pocket in the suction line.
Pump is noisy
:
•
The pump is being starved (viscous liquid cannot get
to pump fast enough). Increase the suction pipe size,
reduce its length or slow down the pump.
•
The pump is cavitating (liquid vaporizing in suction line).
Increase suction pipe size or reduce its length.
•
Check alignment.
•
The magnetic coupling has decoupled. Shut off and
restart.
Pump is not delivering up to capacity:
•
The pump is starving or cavitating - increase suction
pipe size or reduce length or reduce pump speed.
•
The strainer is partially clogged.
•
An air leak somewhere in suction line.
•
The pump may be running too slow. Is motor the correct
speed and wired up correctly ?
•
The pressure relief valve is set too low, stuck open or
has a damaged poppet or seat.
•
The bypass line around the pump is partially open.
•
The pump is worn out or there is too much end
clearance.
Pump takes too much power (stalls motor):
•
The liquid is more viscous than the unit is sized to
handle.
•
The system pressure relief valve is set too high.
•
The bushings have frozen up or the liquid has set up in
the pump.