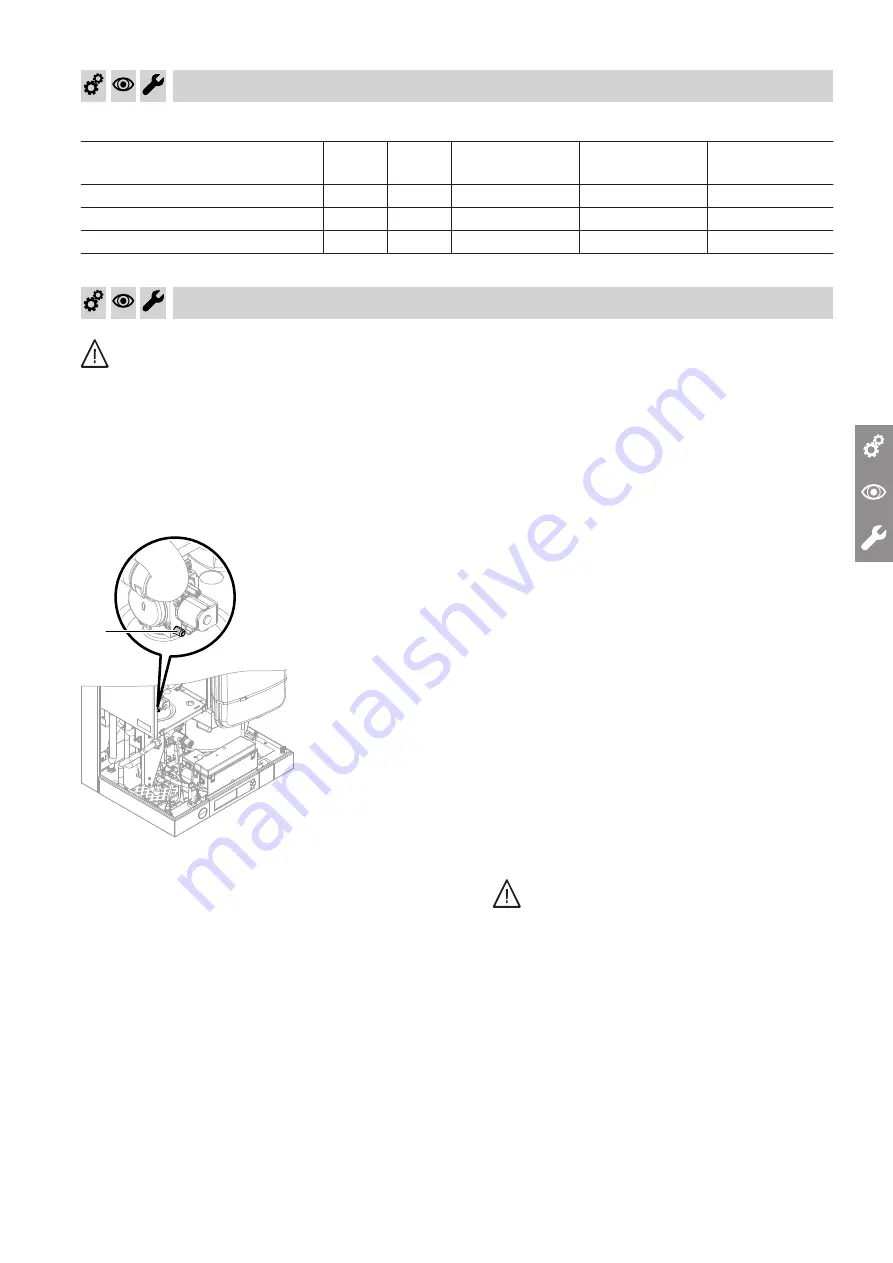
23
Selected gas type
Gas
type
Date
CO
2
content in
%
O
2
content in % CO content in
ppm
Delivered condition
G 20
7.5 - 10.5
< 1000
Changed to
< 1000
Changed to
< 1000
Checking the static pressure and supply pressure
Danger
CO formation as a result of incorrect burner
adjustment can have serious health implications.
Check the CO content before and after carrying
out work on gas appliances.
Operation with LPG
Purge the LPG tank twice on commissioning or
replacement. Vent the tank and gas connection line
thoroughly after purging.
A
Fig. 18
1.
Close the gas shut-off valve.
2.
Undo screw
A
inside test connector "IN" on the
gas train, but do not remove it. Connect the pres-
sure gauge.
3.
Open the gas shut-off valve.
4.
Check the static pressure.
Set value: max. 57.5 mbar (5.75 kPa)
5.
Start the boiler.
Note
During commissioning, the appliance can enter a
fault state because of airlocks in the gas line. After
approx. 5 s, tap and hold
"R"
for approx. 2 s to
reset the burner.
Ensure that enough heat is being drawn during the
testing and setting processes.
6.
Check the supply (flow) pressure.
Set value:
■
Natural gas: 20 mbar (2.0 kPa)
■
LPG: 50 mbar (5.0 kPa)
Note
Use a suitable tester with a resolution of at least
0.1 mbar (10 Pa) to check the supply pressure.
7.
Implement measures as indicated in the table
below.
8.
Shut down the boiler and close the gas shut-off
valve. Remove the pressure gauge and seal test
connector
A
with screw.
9.
Open the gas shut-off valve and start the appli-
ance.
Danger
Gas escaping from the test connector leads
to a risk of explosion.
Check gas tightness at test connector
A
.
Note
The maximum pressure drop between the gas shut-off
valve and test connector
A
at the gas train is
0.5 mbar (50 Pa).
Commissioning, inspection, maintenance
Changing the gas type
(cont.)
5697789
Summary of Contents for Vitodens 111-W
Page 5: ...5 13 Keyword index 58 Index Index cont 5697789...
Page 59: ...59 5697789...