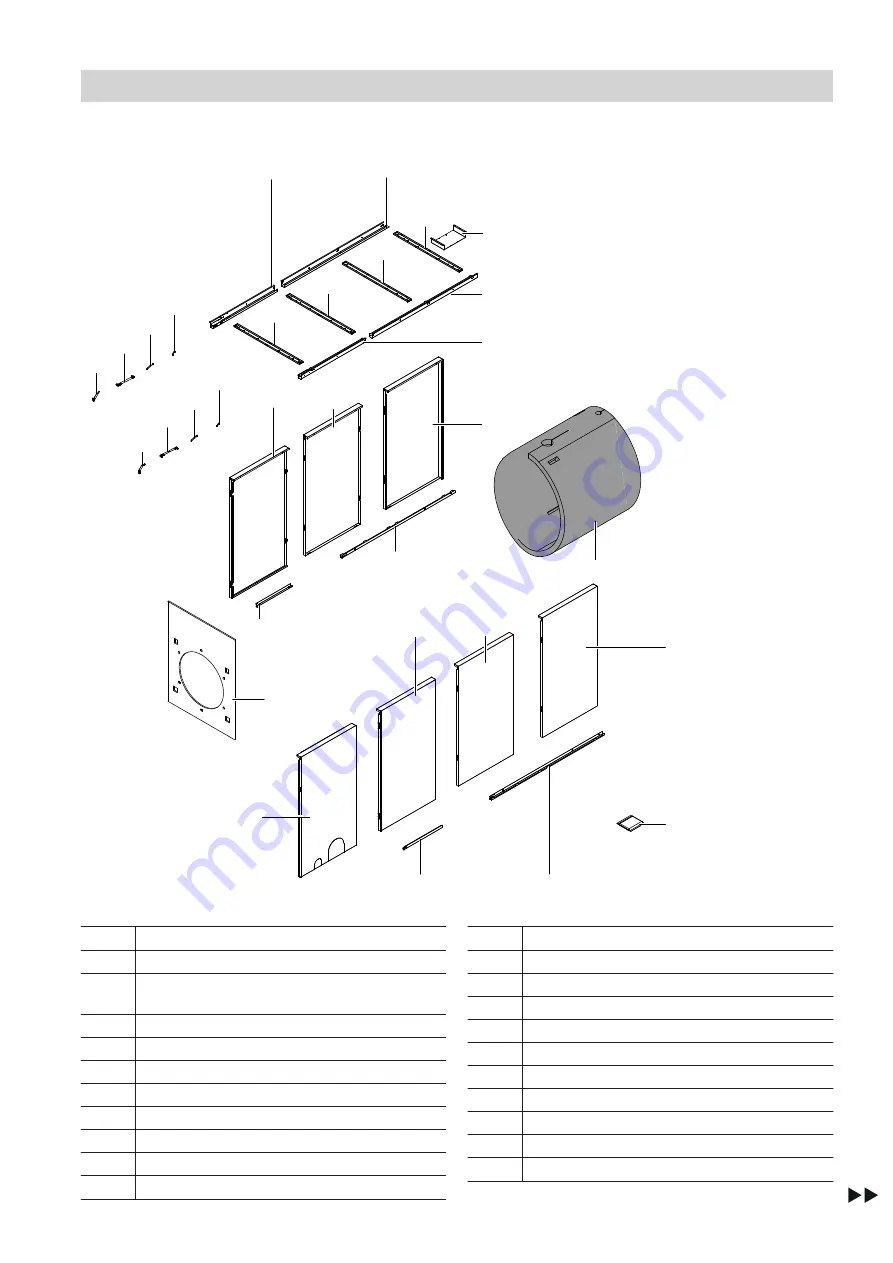
9
Thermal insulation, pack 2
0024
0020
0015
0025
0021
0013
0014
0010
0013
0013
0013
0009
0001
0012
0017
0022
0018
0011
0008
0008
0007
0007
0006
0006
0005
0005
0023
0026
0016
0040
0002
Fig. 5
Pos.
Part
0001
Thermal insulation mat, front
0002
Thermal insulation jacket, combustion cham-
ber module
0005
Fixing strut
0006
Gas spring
0007
Joint, long
0008
Joint, short
0009
Rail, short, top left
0010
Rail, short, top right
0011
Rail, top left
0012
Rail, top right
Pos.
Part
0013
Crossbar
0014
Distribution panel
0015
Extension, bottom left
0016
Extension, bottom right
0017
Rail, bottom left
0018
Rail, bottom right
0020
Centre side panel 1, left
0021
Centre side panel 2, left
0022
Side panel, back left
0023
Side panel, front right
Thermal insulation components
(cont.)
5833291
Summary of Contents for Vitocrossal CRU Series
Page 22: ...22 1 3 4 8 2 4x 3 5 2x 4 8 Fig 16 Fitting the crossbars 5833291...
Page 24: ...24 1 2 1 4 8 4 8 4 3 4 Fig 18 Fitting the side panels 5833291...
Page 26: ...26 4 A C M 6 x 20 B 2x 3 2x 1 2x 2 Fig 20 Fitting the top front panel cont 5833291...
Page 38: ...38 3 4x 4 2x 5 M6 x 10 2 1 4x Fig 32 Fitting the front side panels 5833291...
Page 40: ...40 4 2 5 1 2x 3 M 5 x 25 M 5 x 25 2x A Fig 34 A Type plate Fitting the front panel 5833291...
Page 41: ...41 Vitocrossal type CRU service instructions Commissioning 5833291...
Page 42: ...42 S System examples 5 Keyword index 5833291...
Page 43: ...43 5833291...