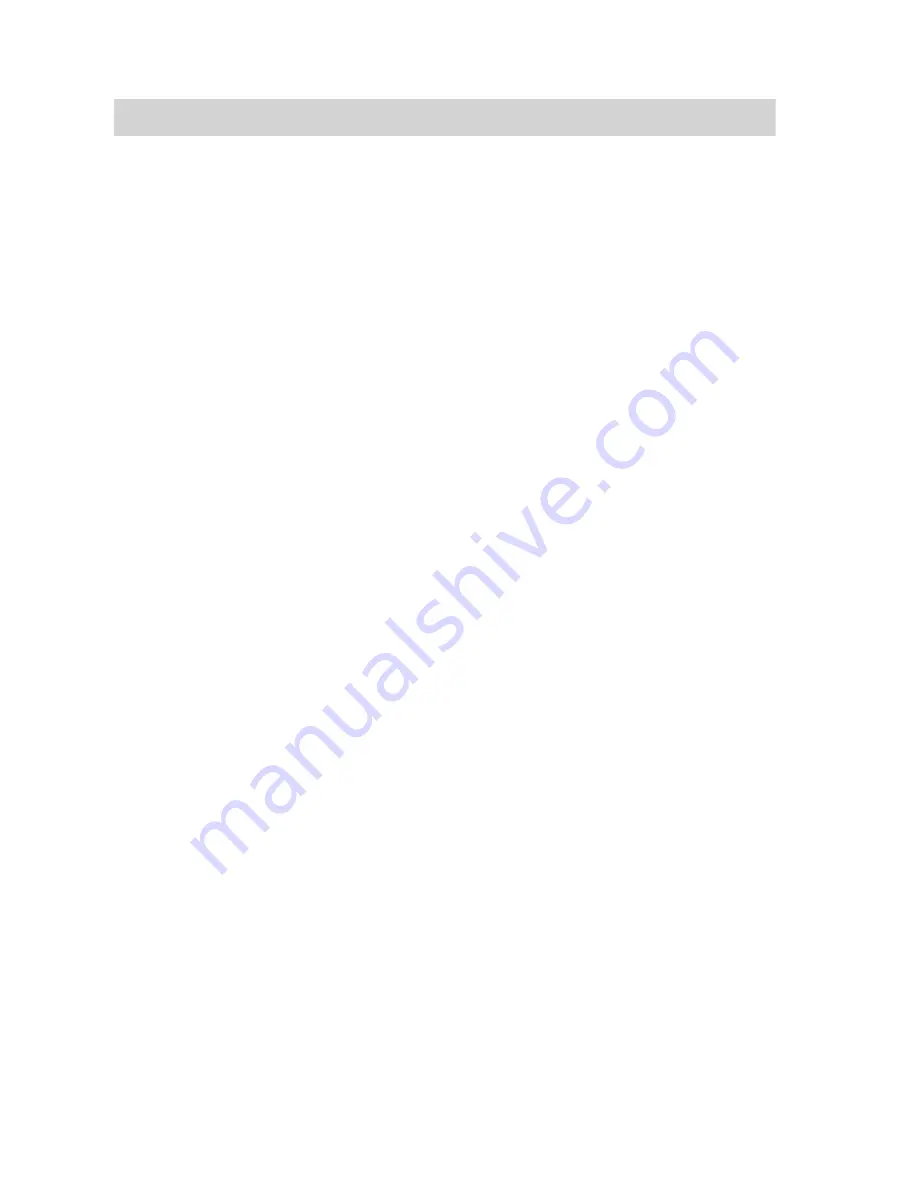
12
Pump-controlled pressure maintain-
ing systems
Note
Install a diaphragm expansion vessel
(DEV) as individual boiler protection in
heating systems with automatic pres-
sure maintaining equipment and/or dea-
eration systems (operating according to
the pressure reduction method for dea-
eration).
The diaphragm expansion vessel must
have the following minimum size (vol-
ume in litres), subject to the boiler output:
Up to 300 kW: 50 litres
Up to 500 kW: 80 litres
Up to 1000 kW: 140 litres
This diaphragm expansion vessel
reduces the frequency and severity of
pressure fluctuations; the runtime of the
pressure maintaining pump is improved
and therefore the operational reliability
and service life of system components is
increased.
Failure to observe these recommen-
dations may result in damage to the
boiler or to other system compo-
nents.
Carry out all checks in accordance with
the manufacturer's instructions. Limit
pressure fluctuations to the lowest pos-
sible differential. Cyclical pressure fluc-
tuations and more significant pressure
differentials point towards a system fault.
Immediately remedy such faults, other-
wise other heating system components
may become damaged.
Diaphragm expansion vessel
1.
Drain the system or close the cap
valve on the diaphragm expansion
vessel and reduce the pressure until
the pressure gauge indicates "0".
Note
The pre-charge pressure of the dia-
phragm expansion vessel (p
0
) is
made up of the static system pres-
sure (p
St
) (= static head) and a sup-
plement (p
0
= p
St
+ supplement).
The supplement is subject to the set-
tings of the high limit safety cut-out.
For a high limit safety cut-out setting
of
100 ºC: 0.2 bar
110 ºC: 0.7 bar
2.
If the pre-charge pressure of the dia-
phragm expansion vessel is lower
than the value calculated according
to the given formula, top up with nitro-
gen until this value has been ach-
ieved.
3.
Top up with water until the charge
pressure of the cooled system is 0.2
bar higher than the pre-charge pres-
sure of the diaphragm expansion
vessel.
4.
Mark this value on the pressure
gauge as the minimum charge pres-
sure.
Commissioning, inspection, maintenance
Further details regarding the individual steps
(cont.)
5692 909 GB
Summary of Contents for Vitocrossal 300 CT3 SERIES
Page 20: ...20 202 203 087 090 206 207 207 207 230 230 093 Parts lists Parts lists cont 5692 909 GB...
Page 21: ...21 C 237 216 208 234 220 209 210 222 217 Parts lists Parts lists cont 5692 909 GB...
Page 24: ...24 087 086 087 086 081 080 084 083 Parts lists Parts lists cont 5692 909 GB...
Page 33: ...33 5692 909 GB...
Page 34: ...34 5692 909 GB...
Page 35: ...35 5692 909 GB...