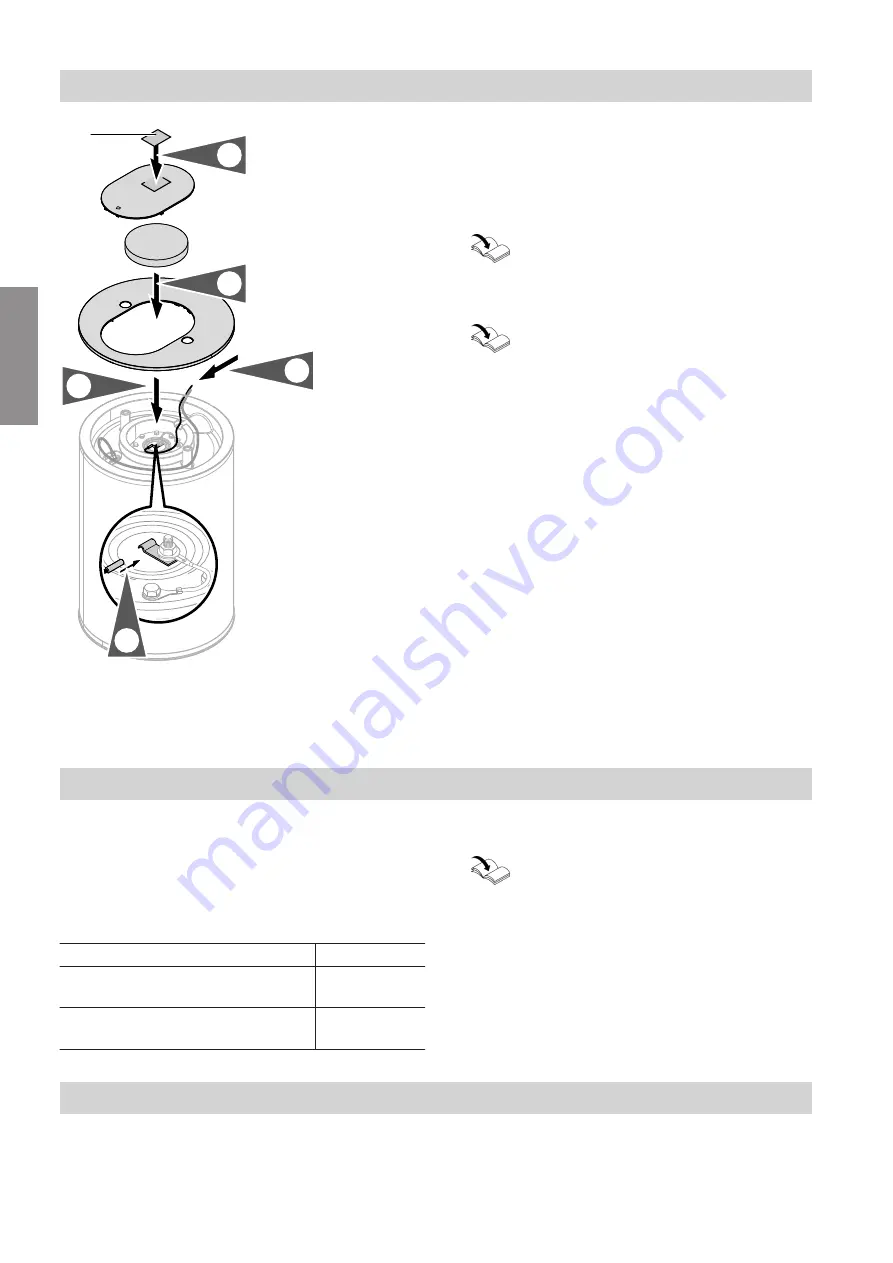
10
A
5.
3.
4.
2.
1.
Fig. 4
A
Type plate
1.
Route the thermometer lead through the groove in
the flange rim.
2.
Insert the thermometer sensor as far as it will go
into the clamping bracket.
Installation instructions, casing for covering
connecting leads/cables
6.
Secure the thermometer (accessory) to the wall.
Installation instructions for wall thermometer
Connections on the heating water side
■
Connect all pipework with detachable fittings.
■
Seal any connections that are not required with red
brass caps.
■
Adjust the temperature controller and high limit
safety cut-out so that the DHW temperature in the
DHW cylinder does not exceed 95 °C.
Permissible temperature
160 °C
Permissible operating pressure
10 bar
(1.0 MPa)
Test pressure
16 bar
(1.6 MPa)
1.
Connect the pipes on the heating water side:
Connection set installation instructions
2.
Only for heating water flow temperatures in excess
of 110 °C and if the system is not equipped with a
high limit safety cut-out: Install an additional type-
tested high limit safety cut-out.
For this, use a TR/HLSC combination device (tem-
perature limiter and high limit safety cut-out).
Connections on the DHW side
■
For connections on the DHW side, observe
DIN 1988 and DIN 4753 (
c
: SVGW regulations).
■
Seal in the drain valve at the drain connection and
check its function.
■
Connect all pipework with detachable fittings.
■
Seal any connections that are not required with red
brass caps.
Installation sequence
Thermometer sensor (if supplied), closing the appliance
6150560
Installation