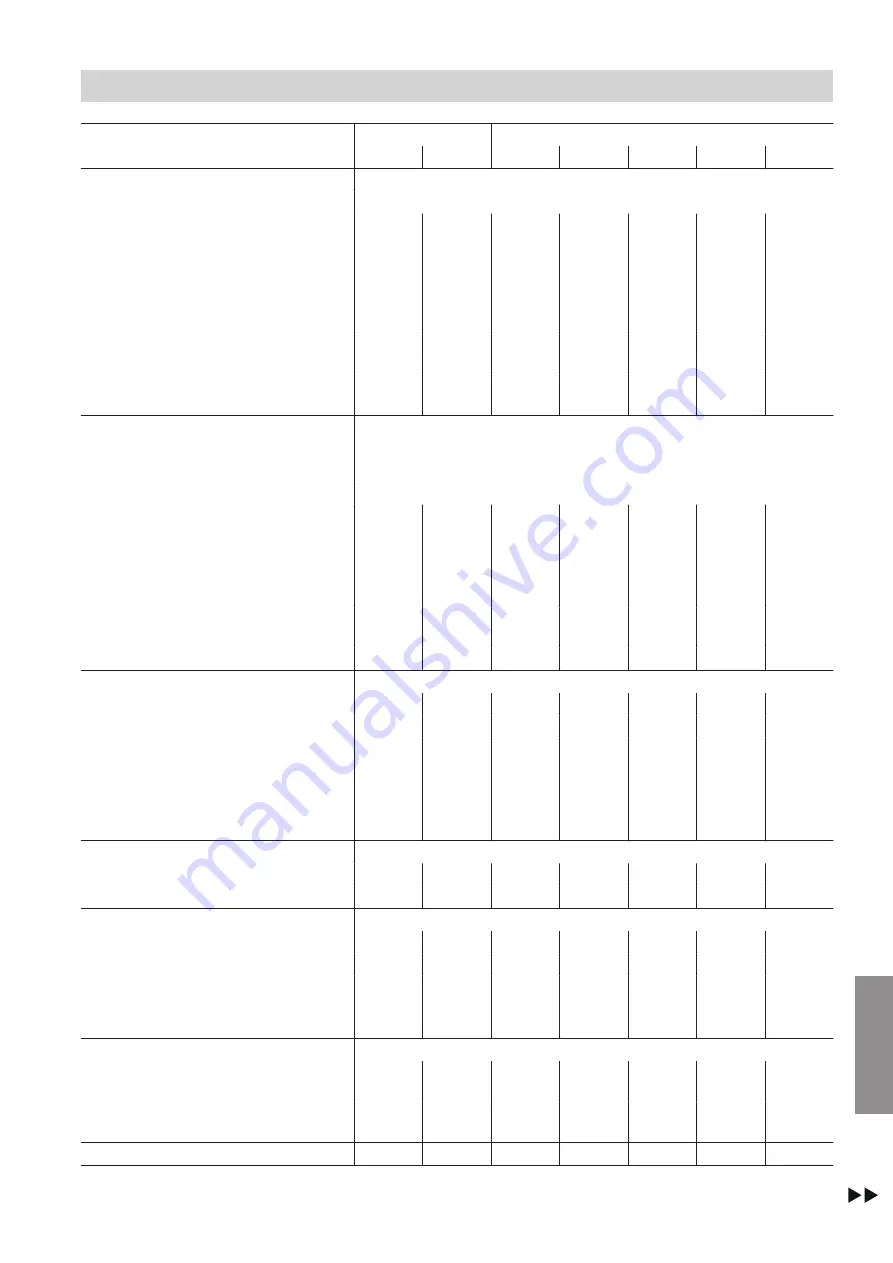
63
Type BW
1-stage 301.
2-stage 302.
CS090
CS120
CS090
CS110
CS140
CS180
CS230
Electrical values, heat pump
Rated voltage, compressor
3/PE 400 V/50 Hz
Compressor rated current
(B0/W35)
A
34.7
42.8
19.0
each
22.3
each
28.3
each
34.7
each
42.8
each
Starting current, compressor
(with starting current limiter)
A
155.0
204.0
87.0
each
112.5
each
136.0
each
155.0
each
204.0
each
Starting current, compressor
with stalled armature
A
310.0
408.0
174.0
each
225.0
each
272.0
each
310.0
each
408.0
each
Heat pump fuse protection
(compressor and consumer)
A
80
100
80
100
125
160
200
Max. operating current, com-
pressor
A
65.4
82.6
68.0
80.0
97
130.8
165.2
Electrical values, control unit
Rated voltage
1/N/PE 230 V/50 Hz
Fuse protection (internal)
1 x B16A
Fuse
6.3 AH (slow)/250 V
Rated output
W
1000
1000
1000
1000
1000
1000
1000
Max. power consumption,
stage 1
W
25
25
25
25
25
25
25
Max. power consumption,
stage 2
W
20
20
20
20
20
Max. power consumption,
stages 1 and 2
W
45
45
45
45
45
Protection class/IP rating
IP 20
IP 20
IP 20
IP 20
IP 20
IP 20
IP 20
Refrigerant circuit
Refrigerant
R410A
R410A
R410A
R410A
R410A
R410A
R410A
Refrigerant charge
kg
15.8
17.5
14.8
16.5
24.8
31.5
41.5
Permiss. operating pressure,
low pressure side
bar
18
18
18
18
18
18
18
Permiss. operating pressure,
high pressure side
bar
45
45
45
45
45
45
45
Number of compressors
1
1
2
2
2
2
2
Permiss. operating pressure
Primary circuit
bar
6
6
6
6
6
6
6
Secondary circuit
bar
6
6
6
6
6
6
6
Dimensions
Total length
mm
1343
1343
1343
1343
1932
1932
1932
Total width
mm
911
911
911
911
911
911
911
Width without side panels
(transport dimension)
mm
850
850
850
850
850
850
850
Total height
mm
1650
1650
1650
1650
1650
1650
1650
Connections
Primary circuit flow and return
(brine side)
Ø
3"
(DN 80)
3"
(DN 80)
3"
(DN 80)
3"
(DN 80)
3"
(DN 80)
3"
(DN 80)
3"
(DN 80)
Secondary circuit flow and re-
turn (heating side)
Ø
2½"
(DN 65)
2½"
(DN 65)
2½"
(DN 65)
2½"
(DN 65)
2½"
(DN 65)
2½"
(DN 65)
2½"
(DN 65)
Weight
kg
770
870
720
910
1180
1280
1425
Specification
Specification, Vitocal 300-G
(cont.)
5789 986 GB
Appendix