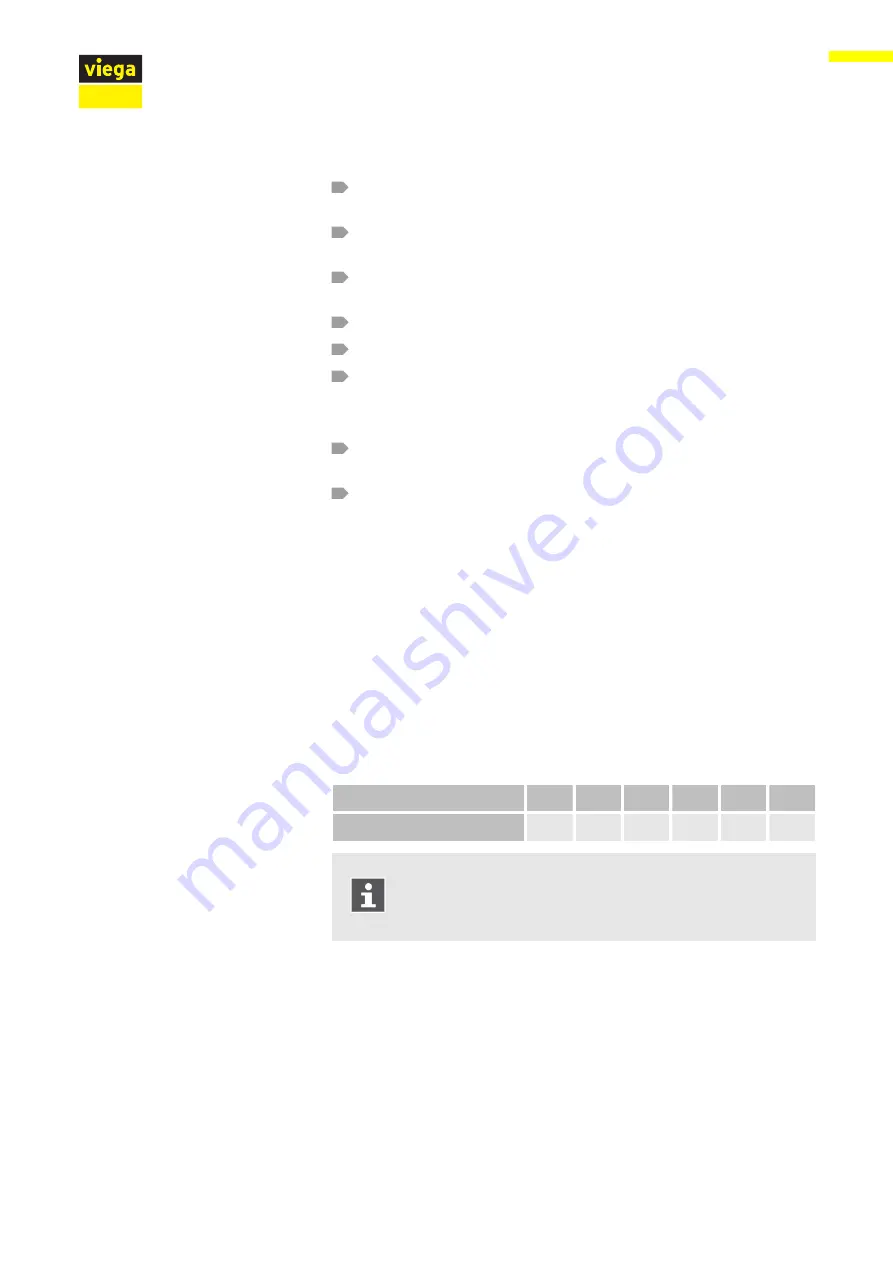
Use the wall bracket to perforate the pre-formed slits in the rear part
of the heat insulation from the front.
Place the wall bracket to the wall (opening pointing up) and fasten it
with dowel and screws.
Clip in the rear part of the heat insulation. Insert the hexagonal pro-
file of the ball valves in the hexagonal profile of the wall bracket.
Connect to the boiler / heating circuit.
Have an authorized technician connect the pump.
Fill the system and perform a leakage test. Ensure that all the air is
flushed out of the system.
If required, ventilate the pump separately.
Set the 3-way valve to the desired supply temperature. Use the ther-
mometer to check the supply temperature.
Pull the rear part of the heat insulation towards the station and clip
in the front part of the heat insulation.
3.3
Control
3.3.1
Setting the underfloor supply temperature
If maximum power (nominal power) is required, set the boiler supply
temperature at least 15 °C higher than the desired supply temperature
in the underfloor circuit.
The setting handwheel of the mixer valve has a scale of 1 to 6 and
allows for continuous setting of a supply temperature between 15 and
55 °C. Refer to the table below for the respective target temperature:
Scale value
1
2
3
4
5
6
Target temperature in °C
15
27
32
37
48
55
The recommended setting range for underfloor heating is
level 3–6 (32–55 °C).
3.4
Disposal
Separate the product and packaging materials (e. g. paper, metal,
plastic or non-ferrous metals) and dispose of in accordance with valid
national legal requirements.
Handling
Compact control station preset value
11 from 11