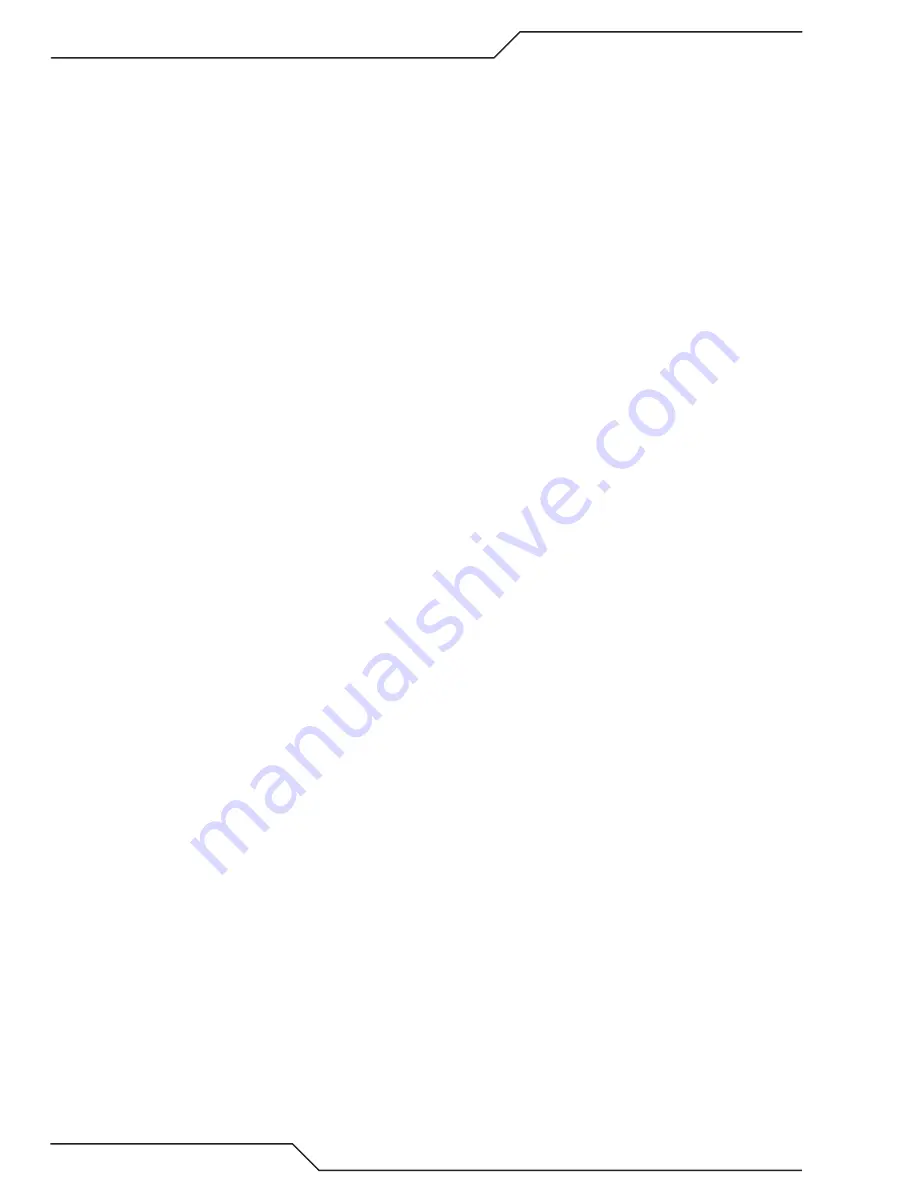
iCNC XT
5-14
OPERATION
Manual 0-5299
5.6.2 Up / Down Switches
All Up / Down switch (See upper box on the picture above)
All Up / Down switch drives all the selected stations up and down.
Individual Up / Down switches (See lower box on the picture above)
Individual Up / Down switches will drive the corresponding station up or down, if the station is selected.
5.6.3 Cutting Oxygen On/Off/Auto Switch
• ON position will open the cutting oxygen solenoid
• AUTO position will allow the cutting program to open the cutting oxygen solenoid when necessary
• OFF position will prevent the cutting program from opening the cutting oxygen solenoid valve.
Summary of Contents for iCNC XT
Page 4: ...TABLE OF CONTENTS ...
Page 14: ......
Page 20: ...iCNC XT 2 4 SPECIFICATIONS Manual 0 5299 2 4 Mechanical dimensions Neugart Gearboxes ...
Page 21: ......
Page 43: ......
Page 44: ......
Page 45: ......
Page 46: ......
Page 48: ......
Page 49: ......
Page 54: ...iCNC XT 3 34 INSTALLATION Manual 0 5299 This Page Intentionally Blank ...
Page 99: ......
Page 109: ......