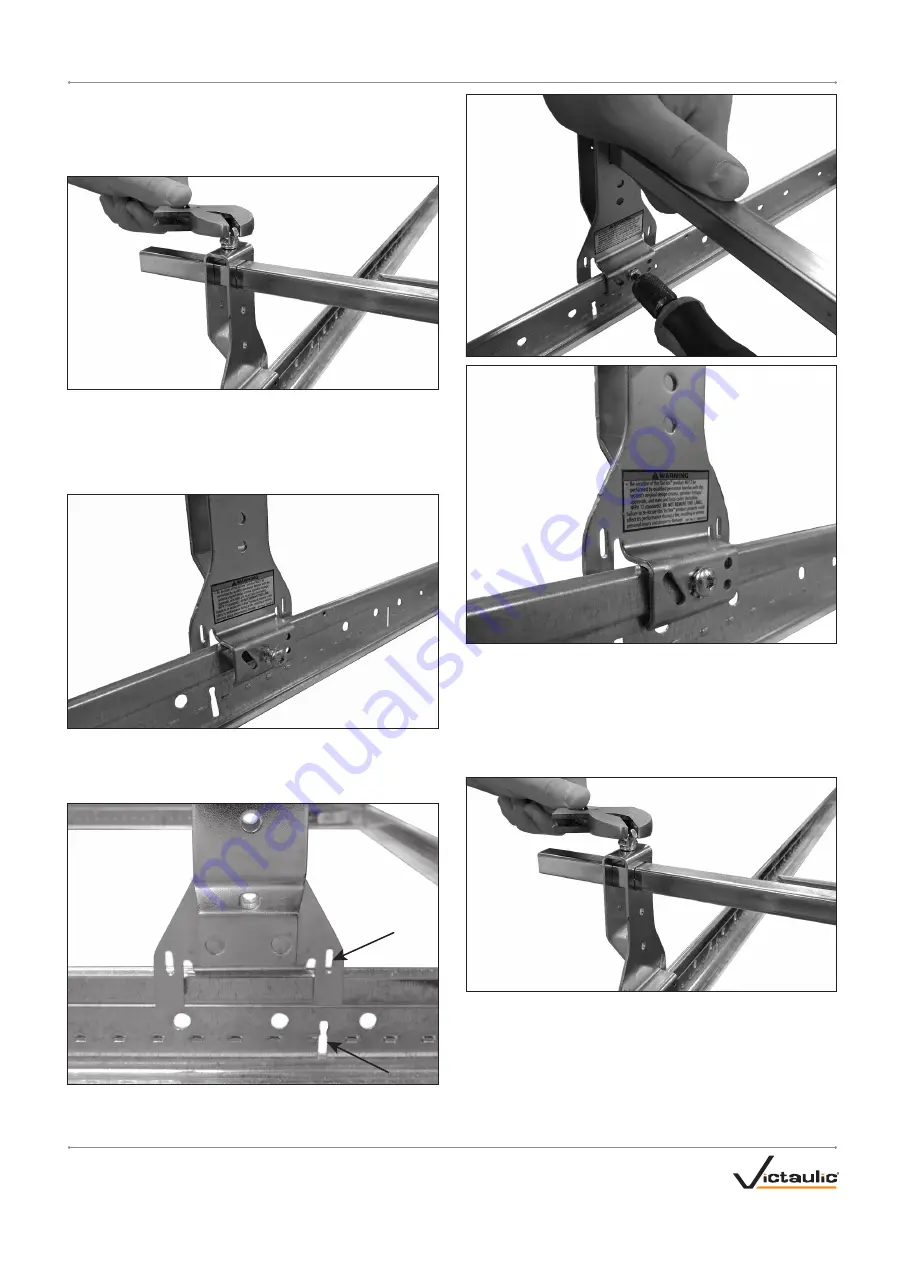
I-VICFLEX.AB1/AB2/AB10_8
REV_R
I-VICFLEX.AB1/AB2/AB10
/ Victaulic
®
VicFlex
™
Styles AB1/AB2/AB10 Brackets / Installation Instructions
INSTALLATION OF STYLE AB1, AB2, AND
AB10 BRACKETS FOR ASTM C635 CEILING
SUSPENSION SYSTEMS INSTALLED IN
ACCORDANCE WITH ASTM C636 STANDARDS
FOR STYLES AB1 AND AB2 BRACKETS ONLY:
For adjustment
purposes, the wing screw on top of the end bracket assembly can be
loosened to allow the end bracket to slide on the square bar. Tighten
the wing screw on top of the end bracket assembly to a torque of
36 inch-lbs/4 N•m (approximately 1/2 to 3/4 of a turn past hand-tight) to
secure the end bracket to the square bar.
1.
Attach the end brackets of the Style AB1, AB2, or AB10 Bracket
to the T-bar rails of an ASTM C635 ceiling suspension system
installed in accordance with ASTM C636 standards. Verify that the
ends of the Style AB1, AB2, or AB10 Bracket engage the rails.
Side Facing the
Opening of the
Center Gate
Assembly
1a.
For center-of-tile installations, align the end bracket with the
center-of-tile slot of the T-bar rail (with the side facing the opening
of the center gate assembly), as shown above.
1b.
Apply light downward pressure, as shown above, to maintain the
position of the end bracket flat against the T-bar rail. To secure
the end brackets to the T-bar rails, tighten the pre-installed sheet
metal screws using a T25 drive bit. Penetrate through the T-bar
rail until the end bracket is seated fully against the T-bar rail, as
shown above.
DO NOT over-tighten the screws. Over-tightening
will cause the screw to strip, resulting in an unsecured bracket
connection.
FOR STYLES AB1 AND AB2 BRACKETS ONLY:
Verify that the wing
screw on top of the end bracket assembly is tightened to a torque of
36 inch-lbs/4 N•m (approximately 1/2 to 3/4 of a turn past hand-tight).