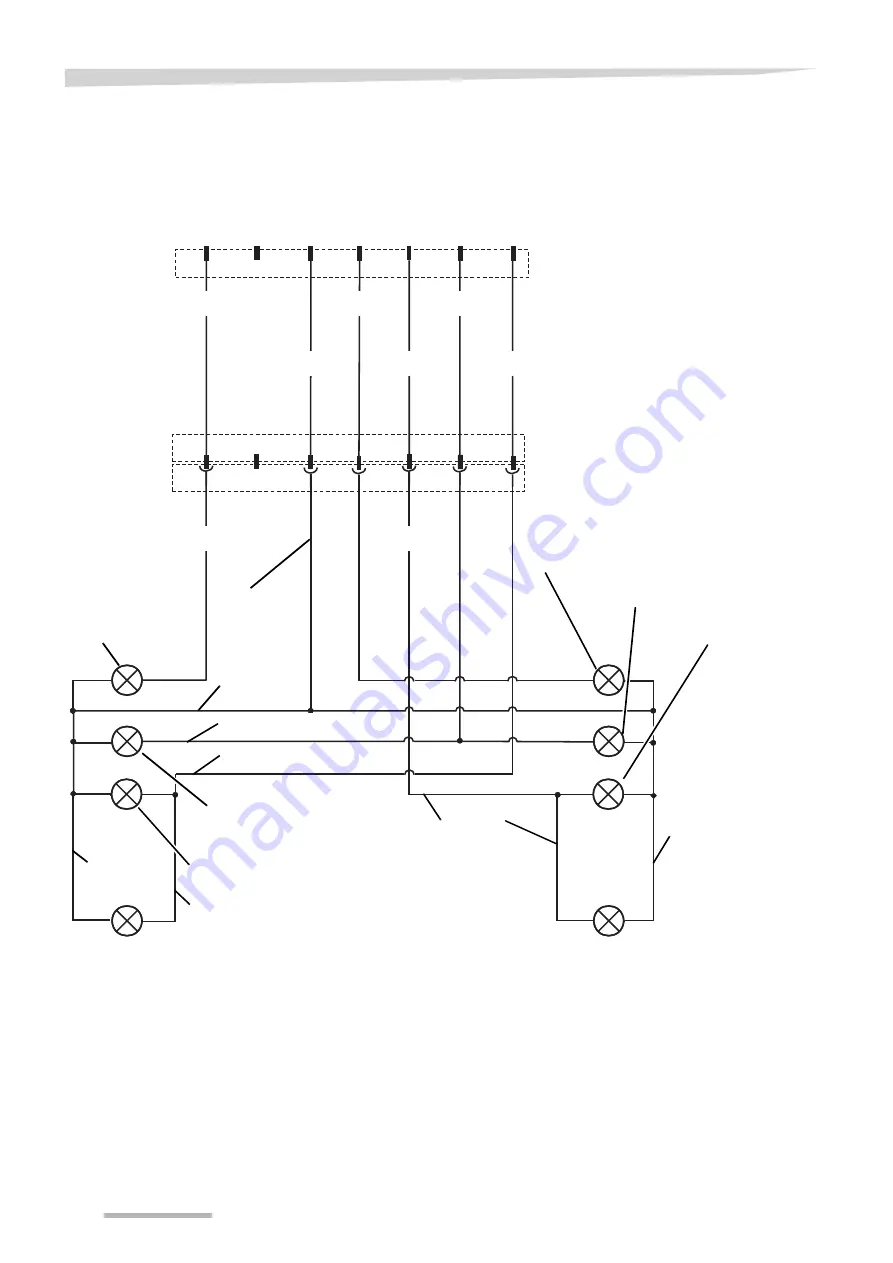
60
Circuit diagrams
Lighting circuit
diagram
1/L
2/54g
3/31
4/R
5/58R 6/54
7/58L
Yellow
white
green
brown
Red
black
Right blinker
Right brake light
Right rear light
Right side light
Yellow
white
Red
brown
black
white
Left side light
white
black
black
Connector and socket
7-pin in accordance with ISO 1724
Left rear light
Left blinker
Left brake light
Earth
Connector
7-pin in accordance with ISO 1724