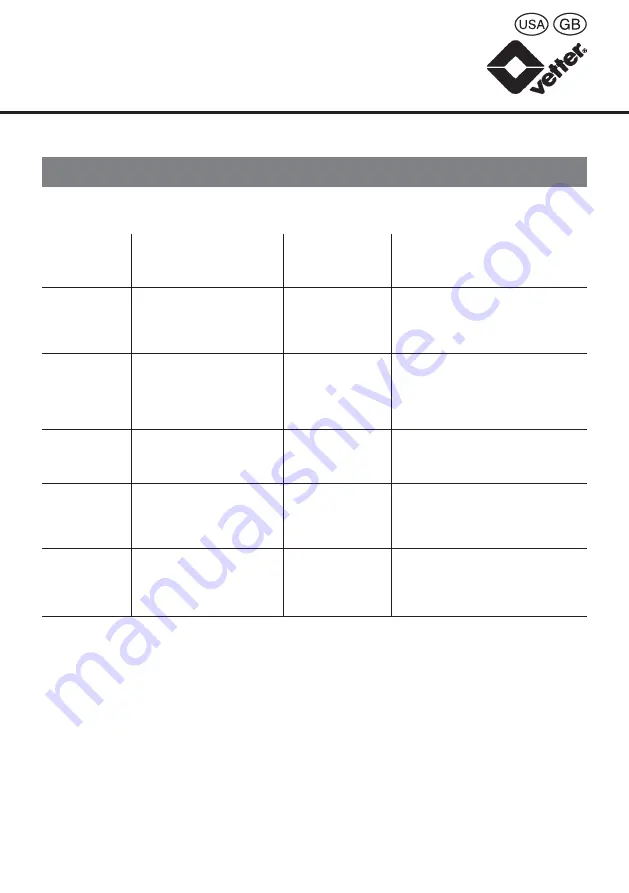
Time
Type of test
Tester
*
Basis
*
Interval
Before initial
Acceptance inspection
Work’s tester
Pressure Vessel Legislation § 9
commissioning
in manufacturer’s works
After receipt
Check on delivery
Qualified tester
DIN 14 152, Part 1, Item 5.2
by the user
After every
Visual and functional
Qualified tester
DIN 14 152, Part 1, Item 5.3.2
use
inspection
Annually
Visual and functional
Qualified tester
DIN 14 152, Part 1, Item 5.3.3
inspection
After repairs
Test on special
Qualified tester
Pressure Vessel Legislation § 11
occasions
*
Pressure Vessel Legislation and DIN 14152 Part 1 are only valid in Germany.
21
Table of recurrent tests